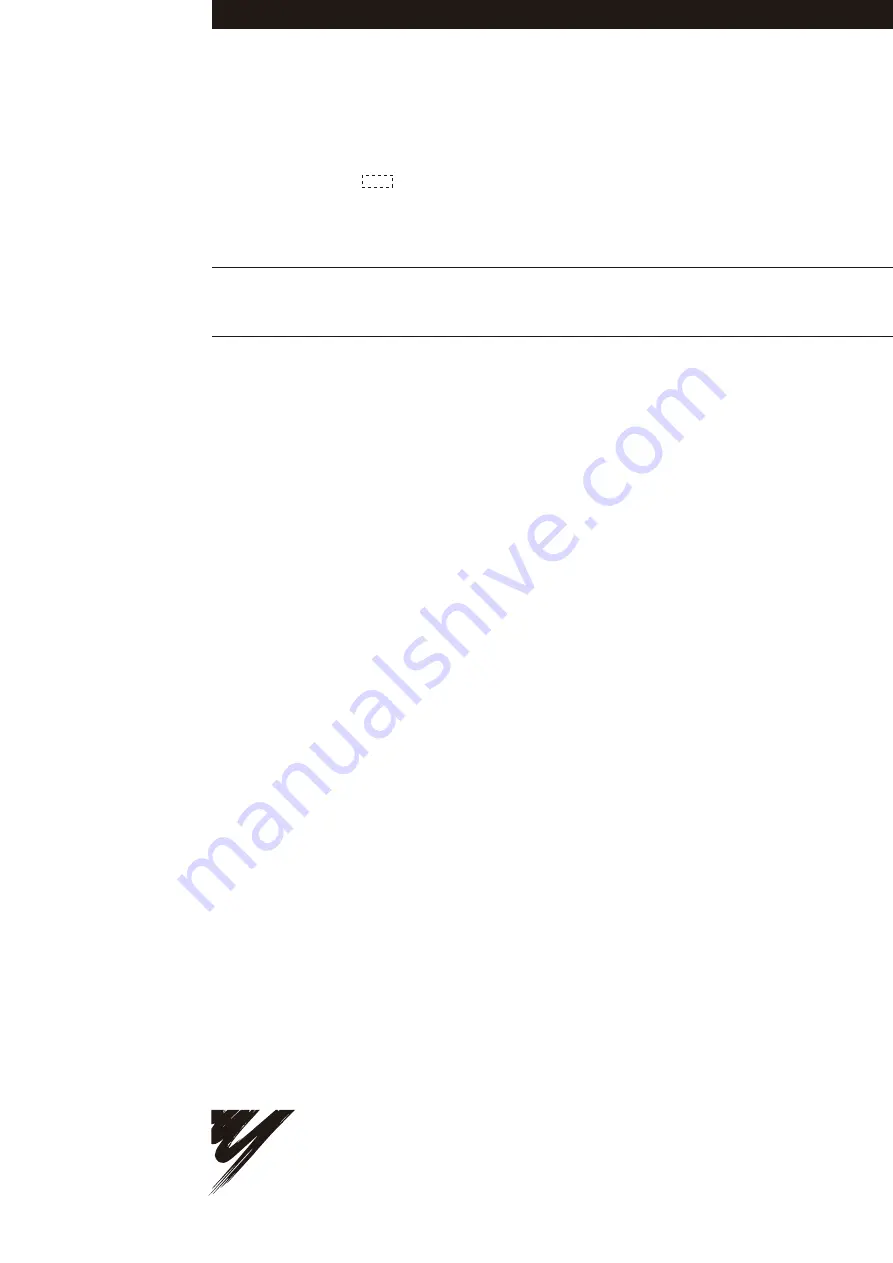
YASKAWA
Varispeed AC
INSTRUCTION MANUAL
MANUAL NO. TOEP C710636 00D
Matrix Converter for Environmentally Friendly Motor Drives
Model: CIMR-ACA
Upon receipt of the product and prior to initial operation, read these instructions
thoroughly, and retain for future reference.
200V Class 5.5 to 45kW ( 9 to 63kVA)
400V Class 5.5 to 75kW (10 to 114kVA)
YASKAWA