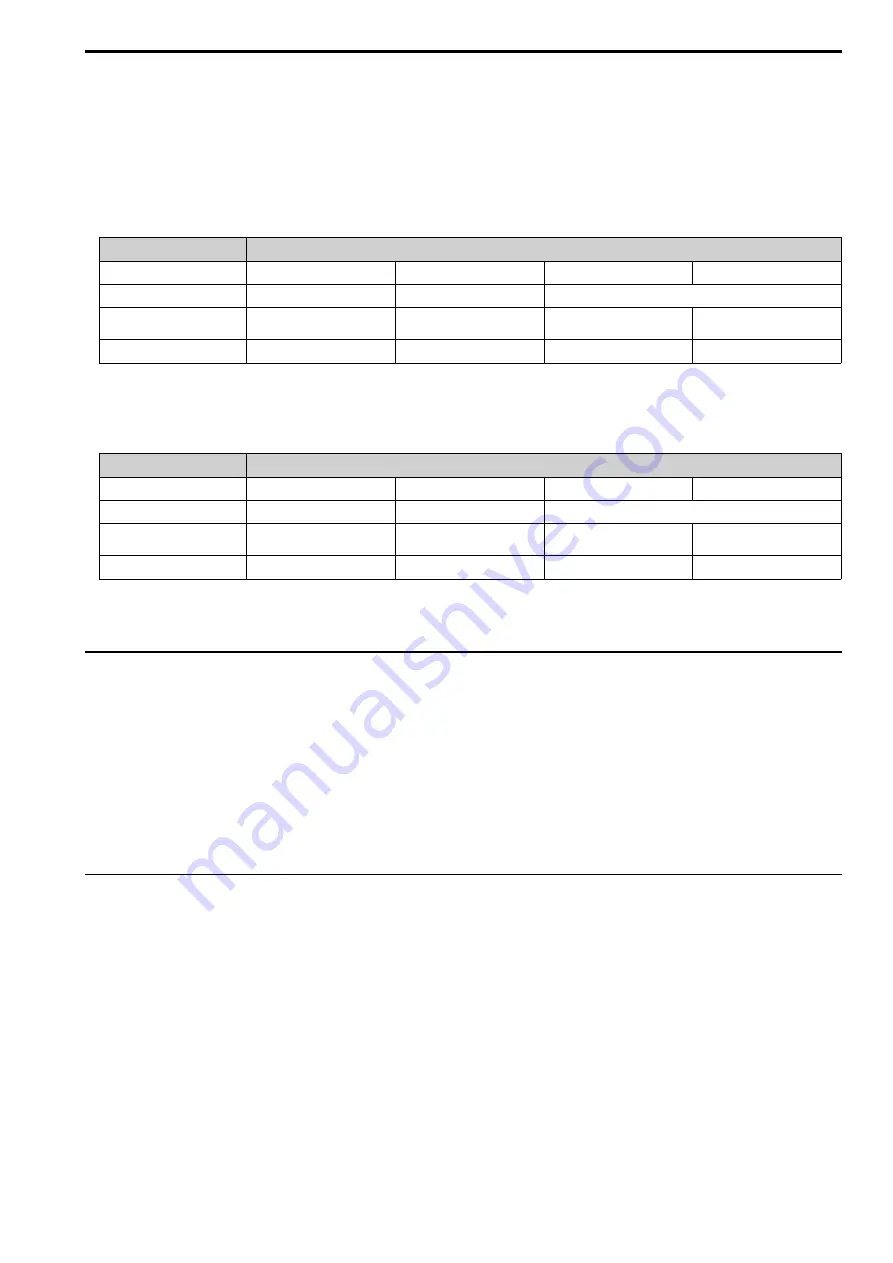
YASKAWA
SIEP C730600 83E CC-Link Technical Manual
27
Note:
1. When the multi-function input terminals are set up for Multi-Step Speed operation, parameters
d1-01 [Reference 1]
through
d1-16
[Reference 16]
take priority as the source of the frequency reference. (assuming that
F6-07 = 1 [Multi-Step Ref @ NetRef/ComRef =
Enable Multi-Step References]
).
2. Dash indicates that the setting has no effect on the reference source.
3. Refer to the technical manual for the drive the CC-Link option is connected to for more details on parameter settings.
D1000
•
Run Command Source
Table 7.3 Run Command Source Priority
-
Setting Status
NetCtrl
1
0
0
0
LOCAL/REMOTE Selection
-
LOCAL
REMOTE
b1-02 [Run Command Selection
1]
-
-
3
not 3
Run Command Source
PLC
Keypad
Option
Determined by
b1-02
Note:
Dash indicates that the setting has no effect on the reference source.
•
Voltage Reference Source
Table 7.4 Voltage Reference Source Priority
-
Setting Status
NetVol
1
0
0
0
LOCAL/REMOTE Selection
-
LOCAL
REMOTE
b1-18 [Run Command Selection
1]
-
-
3
not 3
Voltage Reference Source
PLC
Keypad
Option
Determined by
b1-18
Note:
1. Dash indicates that the setting has no effect on the reference source.
2. Refer to the instruction manual for D1000 the CC-Link option is connected to for more details on parameter settings.
◆
Monitor
You can monitor the operation status of the drive from a PLC.
Follow the following directions to monitor.
1.
Set the monitor code to remote register RW
W0
.
2.
Switch ON the RYC signal (request to execute the monitor code).
The data according to Monitor Code is stored in the buffer memory of the PLC.
Note:
For a list of monitor codes, write data drives, and setting ranges, refer to
Drive Monitor Codes on page 44
or
.
◆
Reading and Setting Parameters
The PLC can write drive parameters, read drive data and operation status, and change settings.
Follow the directions below.
1.
Set the command code to remote register RW
W2
.
Set the write data to RW
W3
as needed.
2.
Switch ON the RYF signal (request to execute the command code).
• The drive executes the process and reply data that correspond with the command code.
• Command codes for drive parameters should be calculated by adding the values shown below to the
MEMOBUS/Modbus register number.
– Read command code: MEMOBUS/Modbus re 1000 (Hex.)
– Write command code: MEMOBUS/Modbus re 2000 (Hex.)
Example: Acceleration time command code for
C1-01 [Acceleration Time 1]
is 200 (Hex.). Get the read
command code by adding 1000 (Hex.), yielding 1200 (Hex.).