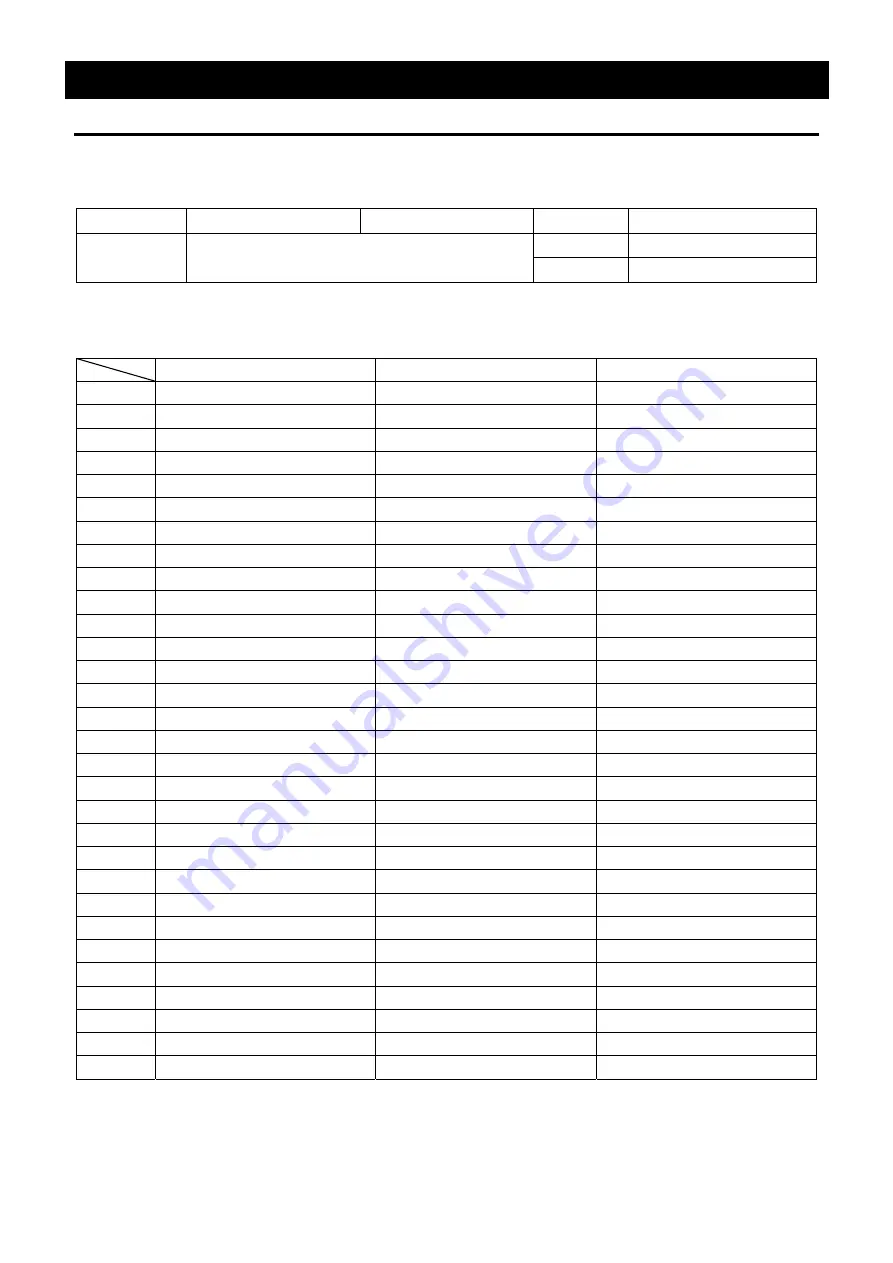
27
Operation Method
Program Operation
Programming Preparation Form 2
(Please use this form by making copies)
Register with:
PrG1 PrG2 PrG3
PAt1 PAt2 PAt3
No.
Date
Project Name
Programmer
Input Value
Temperature
(
℃
)
Time (min.)
Repeat Function
Step 1
:
To/Times
Step 2
:
/
Step 3
:
/
Step 4
:
/
Step 5
:
/
Step 6
:
/
Step 7
:
/
Step 8
:
/
Step 9
:
/
Step 10
:
/
Step 11
:
/
Step 12
:
/
Step 13
:
/
Step 14
:
/
Step 15
:
/
Step 16
:
/
Step 17
:
/
Step 18
:
/
Step 19
:
/
Step 20
:
/
Step 21
:
/
Step 22
:
/
Step 23
:
/
Step 24
:
/
Step 25
:
/
Step 26
:
/
Step 27
:
/
Step 28
:
/
Step 29
:
/
Step 30
:
/