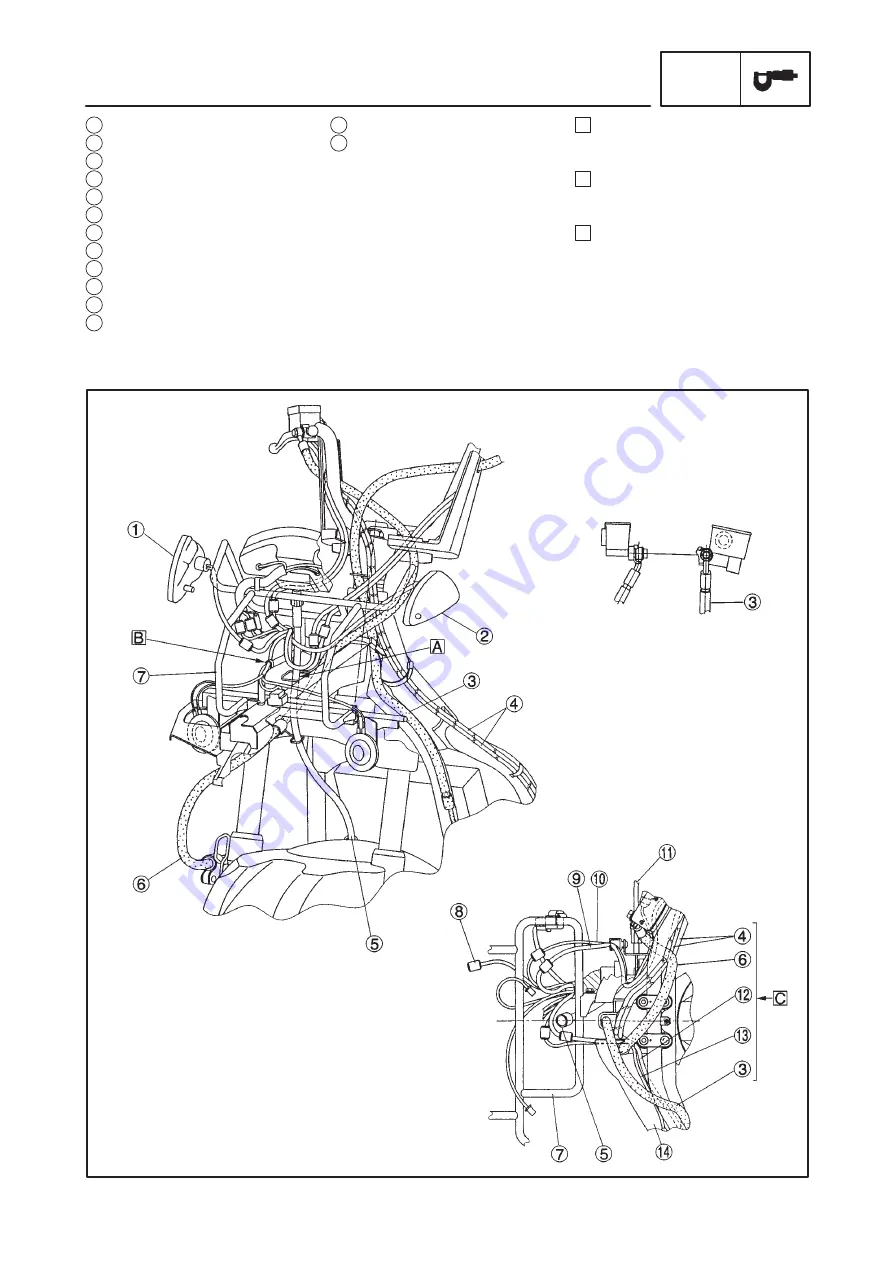
9
13
Rear brake switch lead
14
Handlebar under cover
CABLE ROUTING
SPEC
1
Front turn signal light (right)
2
Front turn signal light (left)
3
Rear brake hose
4
Throttle cable
5
Speedometer cable
6
Front brake hose
7
Headlight stay
8
Grip warmer lead
9
Handlebar switch lead (right)
10
Front brake switch lead
11
Seat lock cable
12
Handlebar switch lead (left)
A Pass the speedometer cable
and front brake hose through
the holder.
B Use a steel clamp on headlight
stay to fasten the headlight
lead and horn lead.
C Do not interfere each other
after installing the handleber
upper cover.