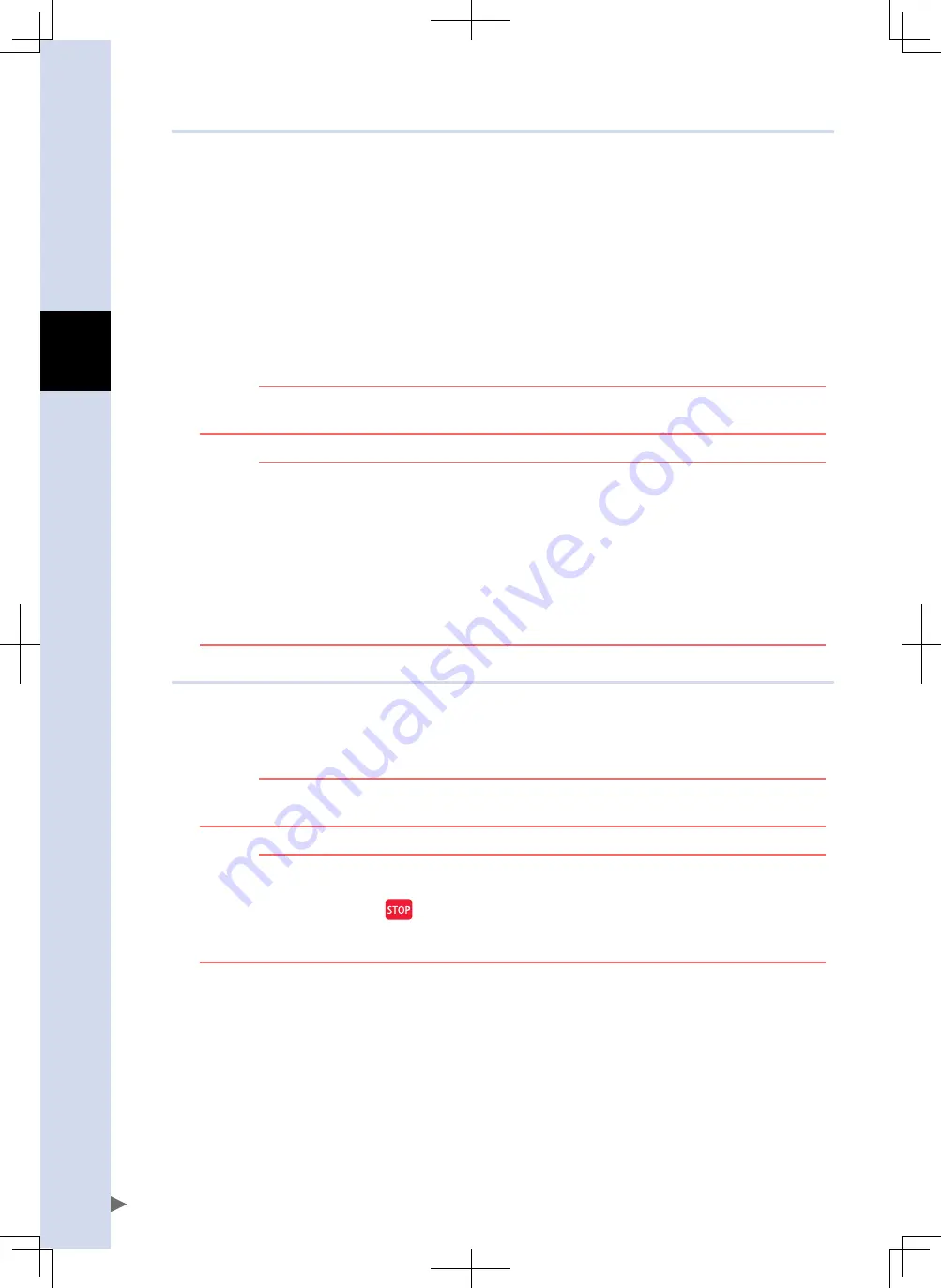
3
Robot settings
3-4
2.1.2 Mark method
In the mark method, the robot is moved to a position beforehand where the return-to-origin is performed and
this position is determined to the return-to-origin position.
There are two kinds of methods to move the robot to a position where the return-to-origin is performed as
described below. (See also "
■
Absolute reset flowchart" in "2.4.2 Mark method".)
Move the robot using the step operation in the servo on state.
1.
When the mark (sticker) that shows the origin position is seen from a position beyond the robot movement range, select
this step.
The origin position reset by means of the mark method is called “absolute reset”.
Move the robot by hand in the servo off state.
2.
When the mark (sticker) that shows the origin position is not seen from a position beyond the robot movement range,
select this step.
c
CAUTION
The absolute reset by means of the mark method can be executed using the programming box (PBX) or online
command. However, note that the absolute reset cannot be executed using the dedicated input.
c
CAUTION
When performing the absolute reset again at the previous absolute reset position, the deviation between the
origin position marks needs to be put in a certain range (repeatability allowable value)
(See the illustration showing the positional relationship between origin position stickers stated in "2.4.2 Mark
method" of this Chapter.)
If the absolute reset is performed at a position exceeding the repeatability allowable value or at a position
different from the previous absolute reset position, the position deviation may occur.
Use the origin position stickers supplied with the product so that the origin position can be reproduced correctly
within the allowable value.
In section "2.4.2.2 Absolute reset in servo off state (re-reset)" of this chapter, the "origin position repeatability
allowable value" indicates the origin position repeatability allowable value for each axis of the robot.
2.1.3 Sensor method (X-axis, Y-axis)
In the sensor method, the target axis is automatically operated for the return-to-origin, and the return-to-origin
is performed at the position where the proximity sensor provided on the target axis detects the detection area
(dog). The return-to-origin in the sensor method can be executed with the programming box (PBX), online
command, and dedicated input.
w
WARNING
SERIOUS INjURY MIGHT OCCUR FROM PHYSICAL CONTACT WITH THE ROBOT DURING OPERATION. NEvER ENTER
WITHIN THE ROBOT MOvEMENT RANGE DURING RETURN-TO-ORIGIN.
c
CAUTION
The origin cannot be detected in any axis which is not positioned on the plus side from the origin (see the Fig.
stated in step 5 of "2.3.2 Sensor method (X-axis, Y-axis)" in this Chapter) before starting the return-to-origin
operation. In this case, press the
key to interrupt the return-to-origin operation, move the target axis to the
plus side of the origin, and reperform the origin return operation. If the return-to-origin operation is not interrupted,
the robot will continue the operation and may collide with the mechanical stopper or a peripheral device.
Summary of Contents for YK-XR Series
Page 1: ...EWFK155120 E66 Ver 1 20 YAMAHA SCARA ROBOT Installation Manual YK XR Series YK400XR ...
Page 2: ......
Page 8: ......
Page 37: ......
Page 40: ......
Page 42: ......
Page 48: ......
Page 54: ......
Page 88: ......
Page 121: ...3 Robot settings 3 33 Sticker affixing positions example X X Y Y Y Y Y Y Z R 23305 FK 00 ...
Page 122: ......
Page 123: ...Chapter 4 Periodic inspecition Contents 1 Overview 4 1 2 List of inspection items 4 2 ...
Page 124: ......
Page 128: ......
Page 129: ...Chapter 5 Harmonic drive replacement period Contents 1 Overview 5 1 2 Replacement period 5 2 ...
Page 130: ......
Page 134: ......
Page 140: ......
Page 142: ......
Page 144: ......
Page 146: ......
Page 155: ......
Page 157: ......