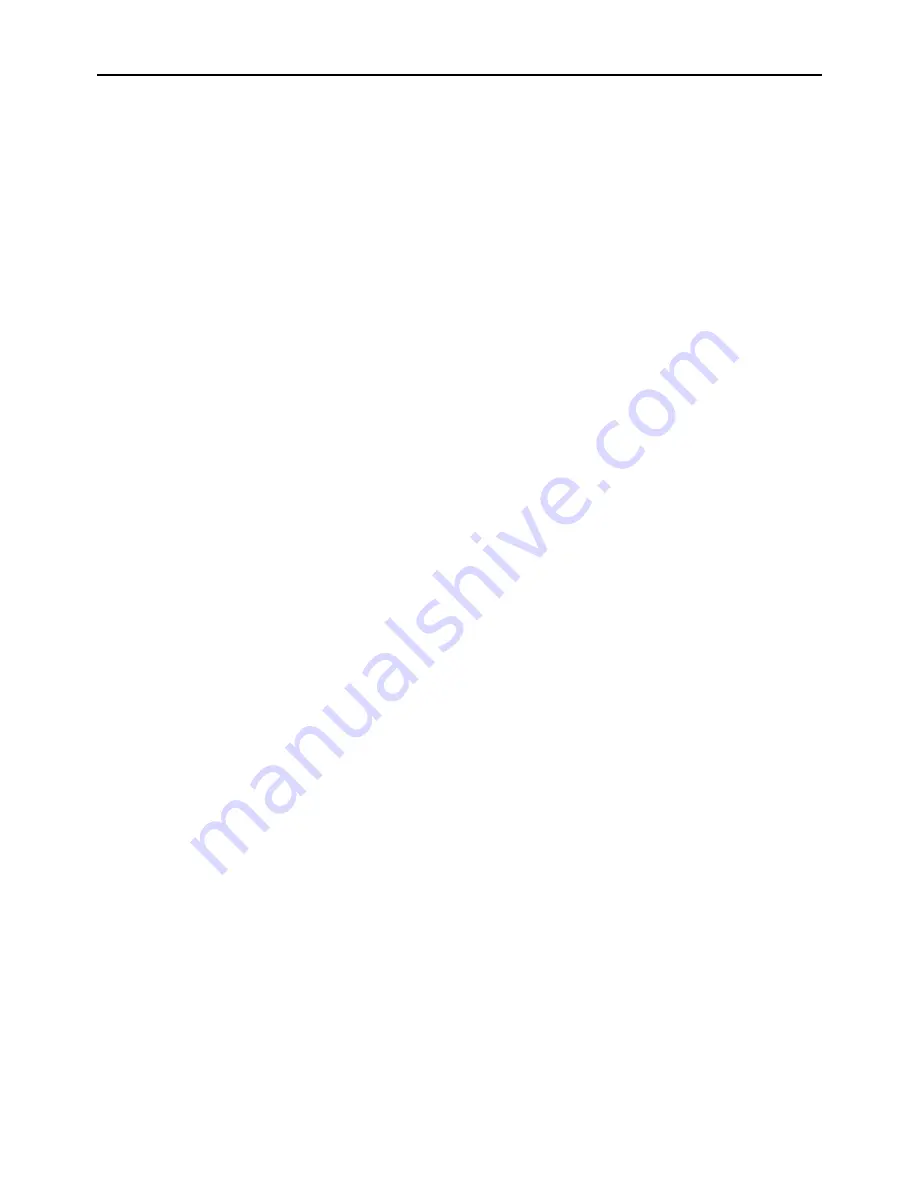
LUBRICATION POINTS AND LUBRICANT TYPES
.................................... 2-23
ENGINE................................................................................................... 2-23
COOLANT FLOW DIAGRAMS
..................................................................... 2-24
OIL FLOW DIAGRAMS
................................................................................. 2-28
CABLE ROUTING
......................................................................................... 2-33
CHAPTER 3
PERIODIC CHECKS AND ADJUSTMENTS
INTRODUCTION
.............................................................................................. 3-1
PERIODIC MAINTENANCE CHART FOR THE EMISSION CONTROL
SYSTEM
......................................................................................................... 3-1
GENERAL MAINTENANCE AND LUBRICATION CHART
............................ 3-2
SEAT, FENDERS AND FUEL TANK
.............................................................. 3-3
REMOVING THE FUEL TANK .................................................................. 3-9
REMOVING THE FUEL PUMP ................................................................. 3-9
INSTALLING THE FUEL PUMP.............................................................. 3-10
INSTALLING THE FUEL HOSE .............................................................. 3-10
ENGINE
......................................................................................................... 3-11
ADJUSTING THE VALVE CLEARANCE ................................................ 3-11
ADJUSTING THE ENGINE IDLING SPEED ........................................... 3-13
ADJUSTING THE THROTTLE LEVER FREE PLAY .............................. 3-14
ADJUSTING THE SPEED LIMITER........................................................ 3-15
CHECKING THE SPARK PLUG ............................................................. 3-16
CHECKING THE IGNITION TIMING....................................................... 3-17
MEASURING THE COMPRESSION PRESSURE .................................. 3-18
CHECKING THE ENGINE OIL LEVEL.................................................... 3-20
CHANGING THE ENGINE OIL ............................................................... 3-22
ADJUSTING THE CLUTCH CABLE........................................................ 3-25
CLEANING THE AIR FILTER ELEMENT................................................ 3-25
CHECKING THE THROTTLE BODY JOINT ........................................... 3-27
CHECKING THE FUEL HOSE ................................................................ 3-28
CHECKING THE BREATHER HOSES ................................................... 3-28
CHECKING THE COOLANT LEVEL....................................................... 3-29
CHANGING THE COOLANT................................................................... 3-29
CHECKING THE COOLING SYSTEM .................................................... 3-32
CHECKING THE COOLANT TEMPERATURE WARNING LIGHT ......... 3-33
CHECKING THE EXHAUST SYSTEM.................................................... 3-34
CLEANING THE SPARK ARRESTER .................................................... 3-34