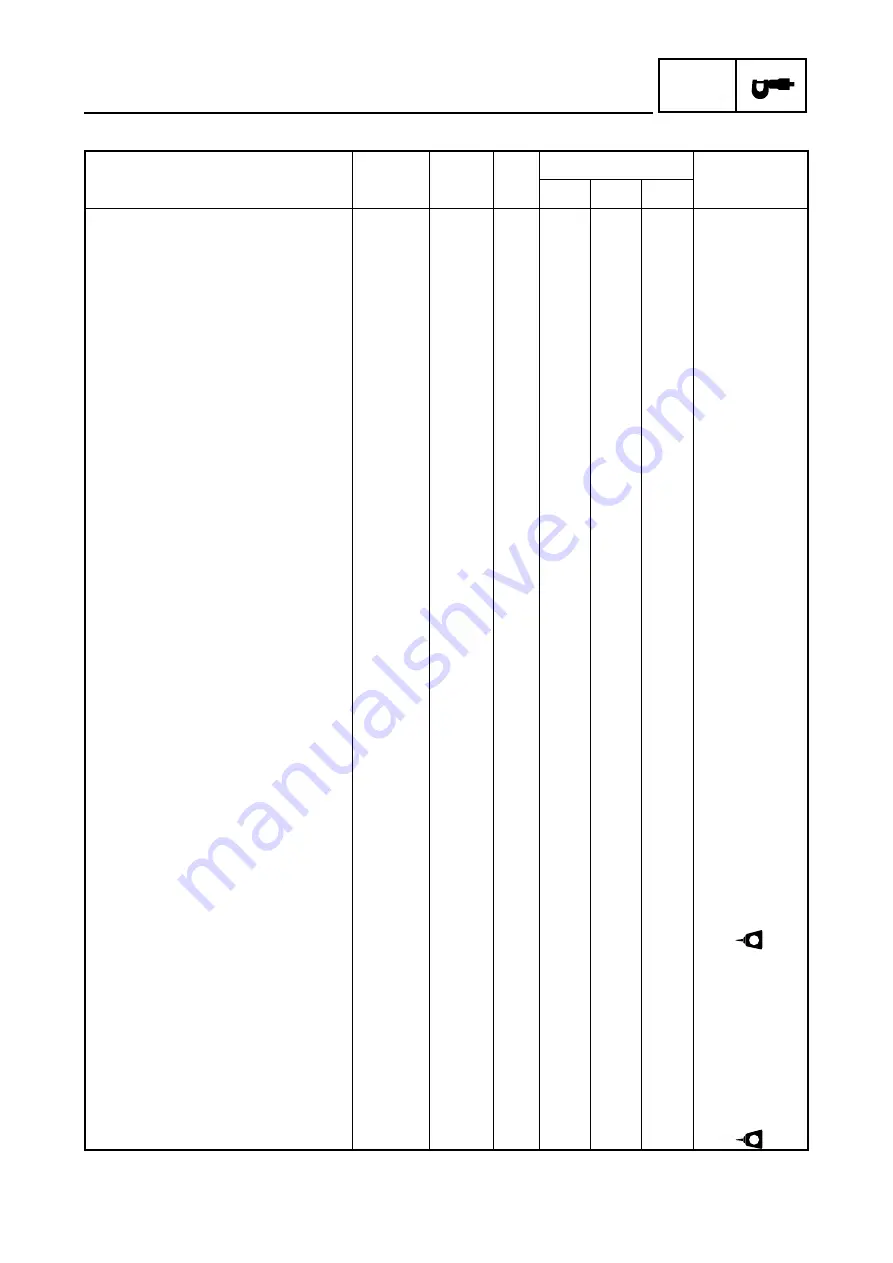
– 13 –
SPEC
Tightening torques
Part to be tightened
Part
name
Thread
size
Q’ty
Tightening torque
Remarks
Nm
m·kg
ft·lb
Cylinder head (exhaust pipe)
Stud bolt
M6
2
7
0.7
5.1
Cylinder head
Bolt
M10
4
32
3.2
23
Bolt
M8
2
20
2.0
14
Camshaft bearing retainer
Bolt
M6
2
8
0.8
5.8
Spark plug
—
M12
1
18
1.8
13
Oil gallery bolt
Bolt
M6
1
7
0.7
5.1
Cylinder
Bolt
M6
1
10
1.0
7.2
Starter pulley
Bolt
M10
1
55
5.5
40
Balancer driven gear
Nut
M16
1
60
6.0
43
Valve adjusting screw
Nut
M7
2
20
2.0
14
Tappet cover (intake)
Bolt
M6
2
10
1.0
7.2
Tappet cover (exhaust)
Bolt
M6
3
10
1.0
7.2
Camshaft sprocket
Bolt
M10
1
60
6.0
43
Camshaft sprocket cover
Bolt
M6
2
10
1.0
7.2
Timing chain tensioner cap
Bolt
M11
1
23
2.3
17
Timing chain tensioner
Bolt
M6
2
11
1.1
8.0
Timing chain guide (intake)
Bolt
M6
2
10
1.0
7.2
Oil strainer
Bolt
M5
2
4
0.4
2.9
Oil filter union bolt
—
M20
1
68
6.8
49
Oil filter cartridge
—
M20
1
17
1.7
12
Oil cooler
Bolt
M6
4
7
0.7
5.1
Oil cooler fan
Bolt
M6
3
6
0.6
4.3
Oil hose union bolt
—
M14
2
50
5.0
36
Oil hose (oil cooler side)
—
M16
2
21
2.1
15
Oil hose (crankcase side)
—
M16
2
35
3.5
25
Oil pump assembly
Bolt
M6
3
7
0.7
5.1
Oil pump housing
Screw
M5
1
5
0.5
3.6
Plate (oil pump driven gear)
Bolt
M6
2
7
0.7
5.1
Intake manifold
Bolt
M8
2
20
2.0
14
Crankcase
Bolt
M8
3
20
2.0 14
Bolt
M6
15
10
1.0
7.2
Oil drain bolt
Bolt
M12
1
23
2.3
17
Bearing retainer (right crankcase)
Bolt
M6
2
10
1.0
7.2
LT
Bearing retainer (left crankcase)
Torx
screw
M6
1
11
1.1
8.0
Crankcase oil passage plug
—
M14
1
25
2.5
18
Lead holder (stator assembly)
Bolt
M5
2
7
0.7
5.1
Drive belt case
Bolt
M6
9
10
1.0
7.2
Bearing housing (primary sheave)
Bolt
M6
4
10
1.0
7.2
Drive belt case cover
Bolt
M6
14
10
1.0
7.2
Crankcase cover
Bolt
M6
12
10
1.0
7.2
Stator assembly
Screw
M6
3
7
0.7
5.1
LT
MAINTENANCE SPECIFICATIONS
Summary of Contents for YFM350FAS
Page 1: ...YFM35FAS YFM350FAS 5UH2 AE1 SUPPLEMENTARY SERVICE MANUAL ...
Page 2: ......
Page 10: ......
Page 34: ... 24 SPEC 1 Crankshaft 2 Oil filter OIL FLOW DIAGRAMS ...
Page 116: ......
Page 117: ......
Page 118: ...YAMAHA MOTOR CO LTD 2500 SHINGAI IWATA SHIZUOKA JAPAN ...