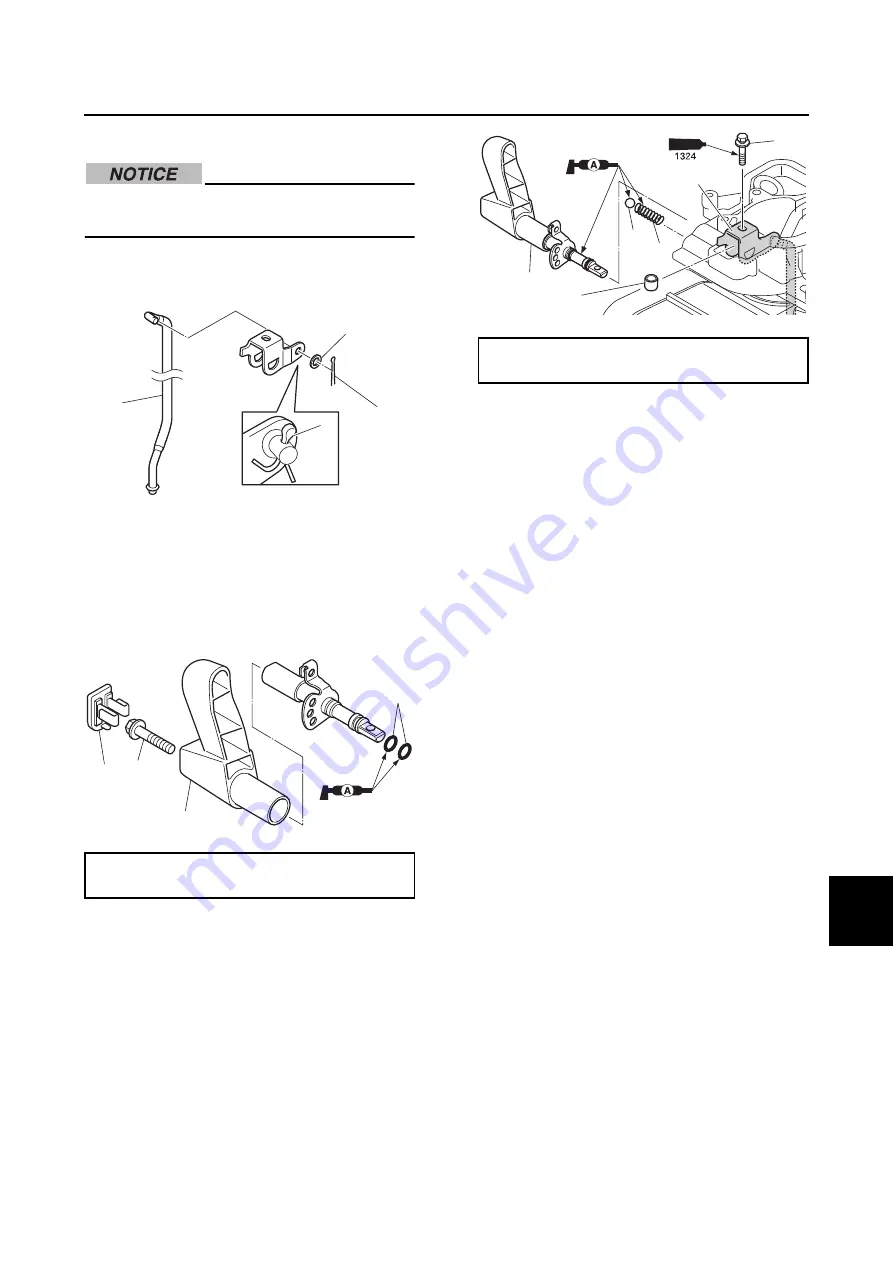
9-14
Upper case and shift lever
0
1
2
3
4
5
6
7
8
9
10
A
Installing the shift lever
Do not reuse a cotter pin or O-ring, always
replace it with a new one.
1.
Install the shift rod
a
, the washer
b
, and
a new cotter pin
c
.
2.
Install new O-rings
d
and the shift lever
e
.
3.
Tighten the shift lever bolt
f
to the
specified torque, and then install the cap
g
.
4.
Install the spring
h
, ball
i
, collar
j
,
bracket
k
, and shift lever
e
.
5.
Tighten the shift link bolt
l
to the
specified torque.
Shift lever bolt
f
:
19 N·m (1.9 kgf·m, 14.0 ft·lb)
c
b
a
c
d
f
g
e
Shift link bolt
l
:
3.5 N·m (0.35 kgf·m, 2.58 ft·lb)
i
e
l
k
h
j
Summary of Contents for F4B
Page 1: ...SERVICE MANUAL 6BV 28197 3M 11 F4B F5A F6C ...
Page 4: ......
Page 16: ...0 11 GEN INFO General information MEMO ...
Page 66: ...5 7 ELEC Electrical system MEMO ...
Page 160: ...8 19 LOWR Lower unit MEMO ...
Page 180: ...9 19 BRKT Bracket unit MEMO ...
Page 198: ...i 5 Index MEMO ...
Page 201: ......
Page 202: ...Jan 2019 ABE E_3 ...