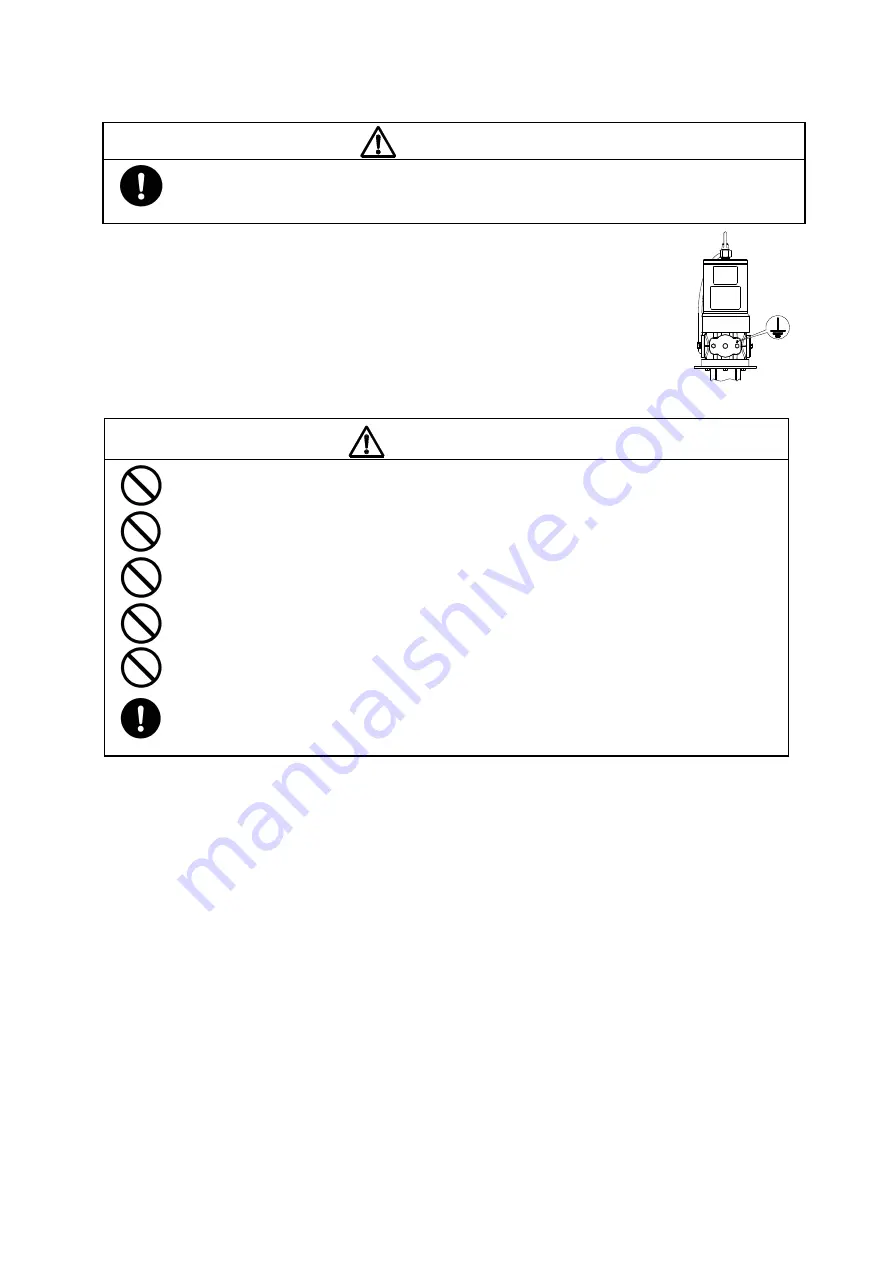
5
3.9 Connecting the ground wire
WARNING
- Make ground connection when working with flammable material or in explosive atmosphere. Rapid
pumping of material can result in static electrical charge. Also, be sure to provide proper ventilation
where a flammable atmosphere may exist.
1) When installing the pump, be sure to connect the ground wire at the
specified position. (Fig. 8)
2) Also connect ground wires to peripheral equipment and piping.
3) Use
2.0mm
2
minimum ground wire.
4. Operating Method
CAUTION
-
Keep your face away from the bleeder valve. Material may spurt out together with compressed air.
-
Do not exceed the maximum operating pressure of the pump (0.7MPa). Overpressure may cause a
product failure resulting in serious personal injury and/or property damage.
-
Keep your hand away from the three studs connecting the air motor and lower pump. Fingers can
get caught in the reciprocating plunger.
-
Keep your face away from the silencer. Compressed air is exhausted at high pressure, causing
moisture to freeze leading cause of injuries.
-
In case of a pump malfunction or shutdown, refer to “5.2 Troubleshooting” to judge the situation
thoroughly and disassemble the pump only as necessary.
-
Avoid allowing the pump to run dry as much as possible. The life expectancy of packings will be
reduced. The pump runs dry when a container becomes empty. Stop the pump immediately after
the material in a container is all gone.
4.1 Description of valve
- Pump Air Regulator (sold separately)
Function : Controlling air pressure for pump operation.
To operate : Clockwise turn will increase pressure. Counterclockwise turn will decrease pressure.
(It can be locked by pushing the knob in.)
Note
: The maximum allowable operating pressure of the pump is 0.7MPa. DO NOT exceed this limit.
Remark
: Discharge pressure can be calculated by multiplying the air pressure by the pump ratio.
- Air Valve, Pump (sold separately)
Function : Starting/Stopping the pump.
To operate : When the lever is parallel to the pipe, the valve is open. If the lever is perpendicular to the pipe,
the valve is closed.
Note
: In case of emergency, close the emergency stop valve attached to the air piping instead of this
valve.
4.2 Solvent cup (125 Type only)
1
)
The pump is equipped with a solvent cup to keep the packing from sticking to the plunger. Shut down the pump
and then fill the cup 2/3 full with suitable lubricant or solvent.
2
)
When lubricant in the cup runs out during operation, shut down the pump first and refill the cup.
Fig. 8
Position for connecting
the ground wire