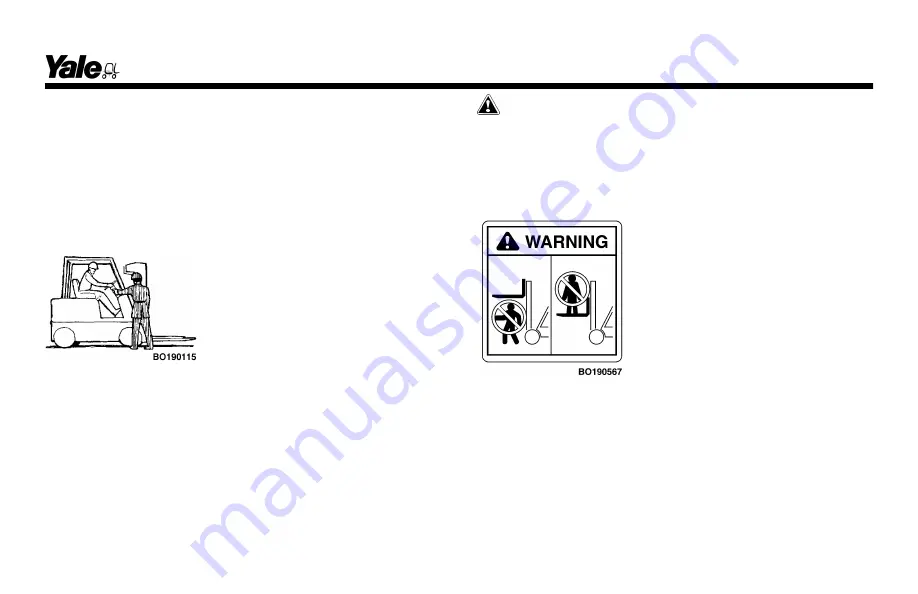
A lift truck is a special machine designed to do a much dif-
ferent job than an automobile. Because of the close areas in
which a lift truck operates and its other operating character-
istics (like rear wheel steering and tail swing), every operator
must receive additional training, even if they have a license
to drive an automobile.
The following discussion lists basic procedures applicable to
lift truck operation.
1.
AUTHORIZED AND TRAINED
OPERATOR ONLY. This means the
operator must be trained (see 29
CFR 1910.178 section I) to drive the
lift truck and it means that the oper-
ator must thoroughly understand the
procedures for lift truck operation. It also means that a quali-
fied person experienced in lift truck operation must guide the
operator through several driving and load handling opera-
tions before the operator attempts to operate the lift truck
alone. A basic education in proper driving and load handling
techniques is absolutely necessary to prepare the new oper-
ator for proper defensive driving and to expect the unexpec-
ted.
WARNING
This lift truck is designed for handling materials. A lift
truck is not designed to lift people. Do not use a lift truck
to lift people unless it has been determined that there is
no other practical option (scaffolds, elevated work plat-
forms, aerial baskets, etc.) to perform the needed work.
If a lift truck is used to elevate a
worker, a safety platform must be
attached to the forks and carriage.
The platform must be specially
built to meet or exceed the
requirements of ANSI/ITSDF
B56.1. It must have a solid floor
with a surface to prevent the feet
of the worker from slipping, hand
rail, toe board, and a screen or shield at least 2 m (7 ft)
high between the people on the platform and the lift
mechanism.
The combined weight of the platform, load, and person-
nel is not to exceed one-half of the capacity as indicated
on the nameplate of the truck on which the platform is
used.
Operating Procedures
75
Summary of Contents for Veracitor GCC040VX
Page 81: ...Figure 12 Seat Adjustment Full Suspension Operating Procedures 79...
Page 113: ...Figure 17 Kubota 2 5L LPG Engine Maintenance and Lubrication Points Maintenance Schedule 111...
Page 169: ...Figure 37 LPG Tank and Bracket Maintenance 167...
Page 203: ...Spacer 5 15 4 15 2 15 1 15 11 14...