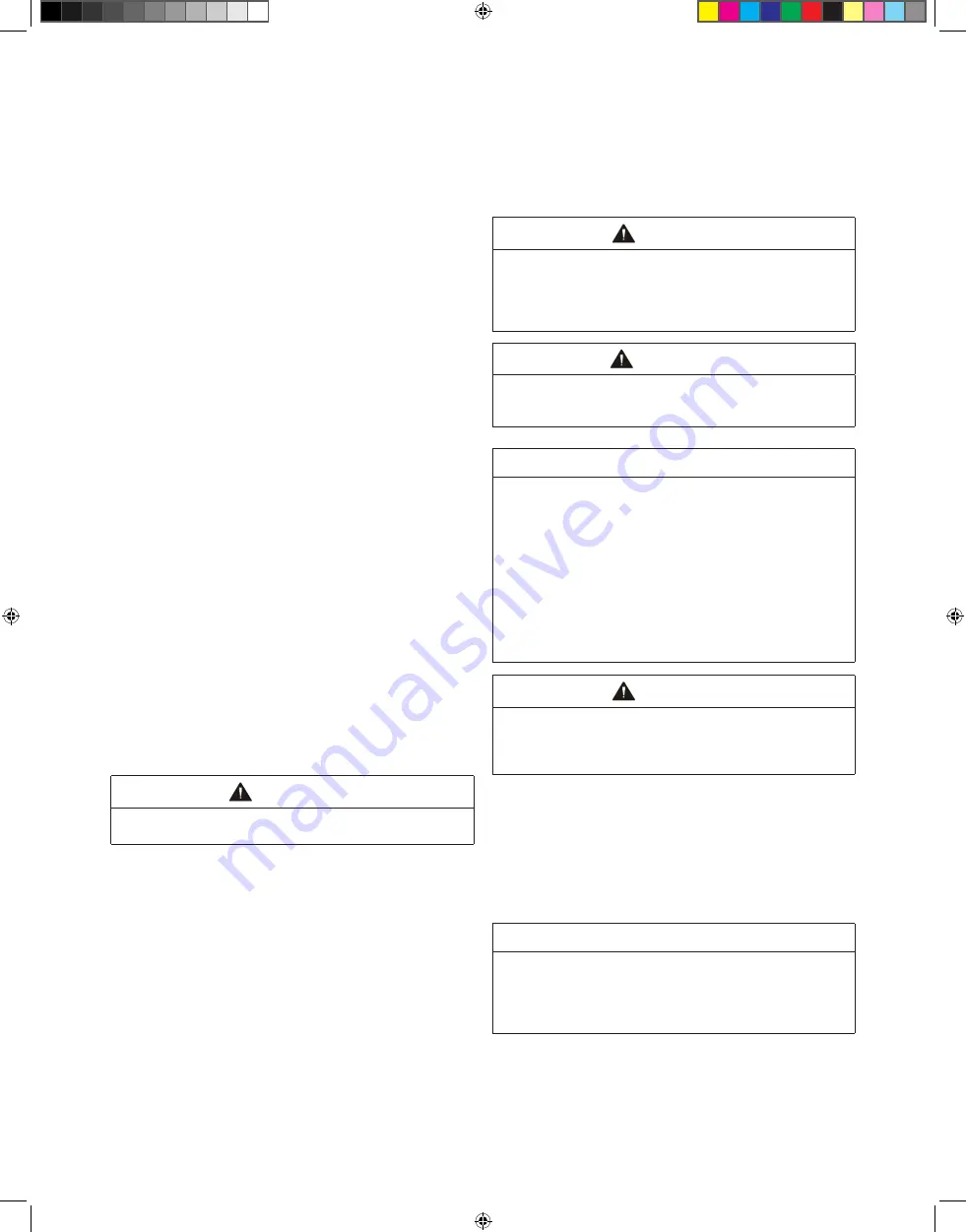
3
SINGLE & DOUBLE GIRDER TOP-RUNNING BRIDGES
WITH INDIVIDUAL MOTOR DRIVEN
END TRUCKS
P/N: 11532620 REV. AA
September 2018
GENERAL
These top running bridge cranes are designed to operate on parallel
crane runway beams with ASCE Rail from 25# to 105# rail or square
bar. Specific rail range is wheel diameter dependant. Motors are
designed for operation on three phase power supplies from 190 to
415 V-50 Hz and 200 to 575 V-60 Hz. Bridge motors and brakes
are designed and intended strictly for variable frequency control
operated by pushbutton pendant or radio control. Pendant may be
located and suspended from an independent festoon or attached
directly to the hoist and trolley. Standard under running single girder
plug & play crane kits described herein are built to 1 through 15
tonne capacities with spans to 60 feet (18.2 meter). Standard top
running double girder plug & play crane kits described herein are
built to 1 through 20 tonne with spans to 60 feet (18.2 meter). Higher
capacities & spans are available and reviewed upon individual
application. Cranes are designed per CMAA Specifications 70 and
74 to meet Class C Moderate Duty Service classification.
BASIC CONSTRUCTION
The basic construction of single and double girder bridges consist
of American Standard S, W Section or fabricated box girder(s) rigidly
connected to the top and side of each endtruck. Each endtruck
has a drive and trailer wheel which run on the runway rails. The
wheels are double flanged, flat tread with an integral rotating axle
supported by anti-friction bearings. Each endtruck is driven by a
helical gearmotor and brake. This drive engages the drive wheel by a
splined connection.
INSTALLATION
GENERAL
The runways on which these cranes will operate must be sufficiently
strong enough to support bridge crane, hoisting equipment and
rated load. Runway rails must be level and parallel. Reference CMAA
70/74 Table 1.4.2-1 for details. Rail joints must be smooth and held
firmly in alignment either by bolted splice bars or by welding. Rails
should be securely fastened to the runway beam.
INSTALLING BRIDGE CRANE
The installation of the crane on the runway shall be performed only
by a qualified crane installer.
For information regarding attaching, lifting and moving the loads
during installation, refer to ANSI B30.2-latest edition, Chapter
2-3 Overhead and Gantry Cranes (Top Running Bridge, Single
or Multiple Girder, Top Running Trolley Hoist; ANSI B30.17-latest
edition, Chapter 17-3 Overhead and Gantry Cranes (Top Running
Bridge, Single Girder, Underhung Hoist) and other applicable codes.
WARNING
Before installing the crane on the runway, lock the runway
conductor disconnect switch in the open (off) position.
Prior to the start of any crane erection the building should be
measured to confirm span and clearances. These measurements
should be checked against the corresponding crane measurements
to insure correctness of “fit”. After assuring that the crane fits the
building, determine orientation of crane position with respect to
the runway. In addition, verify building and runway power supply to
ensure it matches the power requirements of the crane.
These types of cranes are usually lifted into position on the runway
in one piece. Total weight of this crane should be checked against
lifting equipment selected for erection of this crane.
Immediately after the crane is placed on the runway rails check the
wheel flange clearances to the rail. Clearance between the side
of rail head and inside flange of wheel should be between a total
of 3/4” and 1-1/8”, depending on the wheel and rail combination
and whether or not the truck is centered on the rail. Total wheel
float should not be less than the 3/4" as recommended by CMAA
Specifications #70 and #74.
Note: It is suggested that the trolley and hoist be installed on the
bridge crane at this time so that all wiring connections can be
completed.
TYPICAL CONNECTION OF BRIDGE TO
ELECTRICAL SERVICE
The crane inter-connection diagram is shown in Figure 10.
CAUTION
Verify that the crane is furnished for the same voltage,
frequency and phase as the runway power supply. Crane
voltage is shown on nameplate on bridge panel. Do
not operate crane until "Start Up and Pre-Operational
Inspection" are made.
WARNING
Before attempting any electrical connections the main
power switch feeding the runway conductors must be
LOCKED IN THE OPEN (OFF) POSITION.
NOTICE
A fused disconnect switch or circuit breaker must be
installed and electrically positioned between building
power supply and crane runway conductor system.
This disconnect must be lockable in the open position,
in-sight and in-reach for the crane operator, and clearly
labeled. A second lockable disconnect is required on the
bridge crane, electrically positioned between the runway
conductor system and bridge controls. Refer to Article 610
of NFPA No. 70 National Electric Code, OSHA Regulation
1910.179, ANSI/ASME B30.2 and B30.17, local, state
and provincial standards and regulations for specific
requirements.
CAUTION
In accordance with Article 610 of NFPA No. 70 National
Electric Code a separate bonding conductor must be run
for ground. Grounding through the wheels to girders and
runway steel is not permitted.
RUNWAY CONDUCTORS
Motorized bridge cranes and bridge cranes equipped with a
motorized trolley or hoist require runway conductors. Install
conductors according to manufacturer’s instructions and in
accordance with National, State and Local codes.
RUNWAY COLLECTORS
Install, adjust and align collectors with runway conductors.
Connect collectors to appropriate crane wiring as shown in
Crane Inter-Connection Diagram Figure 10.
NOTICE
A minimum of two collector shoes for each conductor bar
is required when using variable frequency drives (inverters)
on bridge and/or hoist controls, per Section 5.14.7 of
CMAA Specifications #70 and #74. Yale•Shaw-Box
standard bridge controls utilize variable frequency drive.
CROSS CONDUCTORS & PUSHBUTTON FESTOON
In most cases, the cross conductors and pushbutton festoon, if
provided, will be installed on your crane as received; however, if
the conductors have been separately shipped, be certain that the
instructions covering installation of these conductors are carefully
followed. Connect all wiring on the crane (main collectors to bridge
GENERAL
CMK_12322 Yale Rotating Axle End Truck Parts 11532619-REV AD_mec.indd 3
10/16/18 2:07 PM