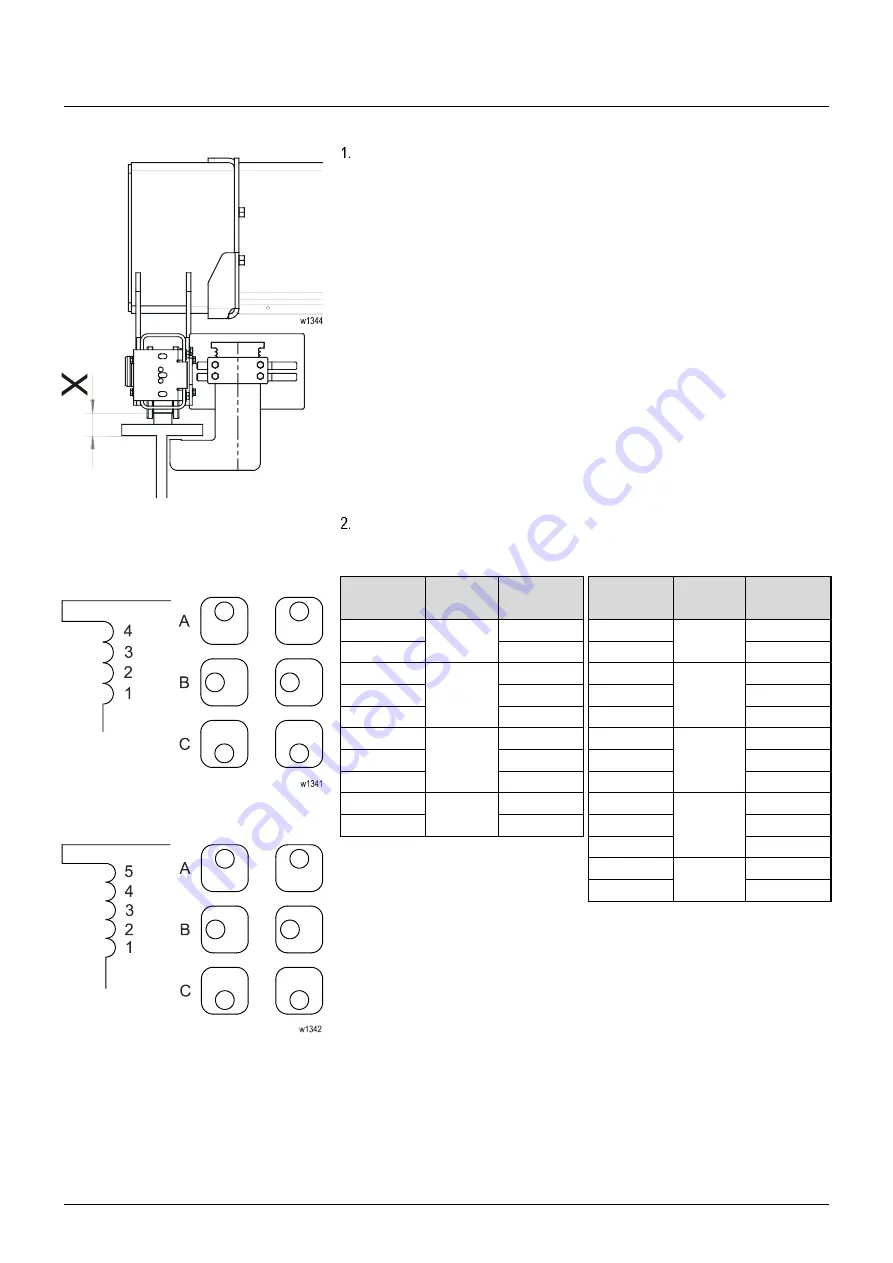
4
Installation
38
07.2020
ba
-o
.2
.6
.0
-us
-3
.2
-ys
|
A1
18
67
50
1 Re
v A
E
Vertical adjustment
Fig. 28
Measure dimension X, see Fig.
Select positions of hook and eccentric from the table.
Trolley type OE-S04
Trolley type OE-S04
Trolley type OE-S05
Hook position
Eccentric position
X
Hook
position
Eccentric
[in]
1.65...1.77
1
B
1.79...1.89
C
1.91...2.05
2
A
2.07...2.17
B
2.19...2.28
C
2.3...2.44
3
A
2.46...2.56
B
2.58...2.68
C
2.7...2.83
4
A
2.85...2.95
B
X
Hook
position
Eccentric
[in]
1.57...1.69
1
B
1.71...1.81
C
1.83...1.95
2
A
1.97...2.09
B
2.11...2.2
C
2.22...2.34
3
A
2.36...2.48
B
2.5...2.6
C
2.62...2.74
4
A
2.76...2.87
B
2.89...2.99
C
3.01...3.13
5
A
3.15...3.27
B
Fig. 29
Trolley type OE-S05
Hook position
Eccentric position
Fig. 30