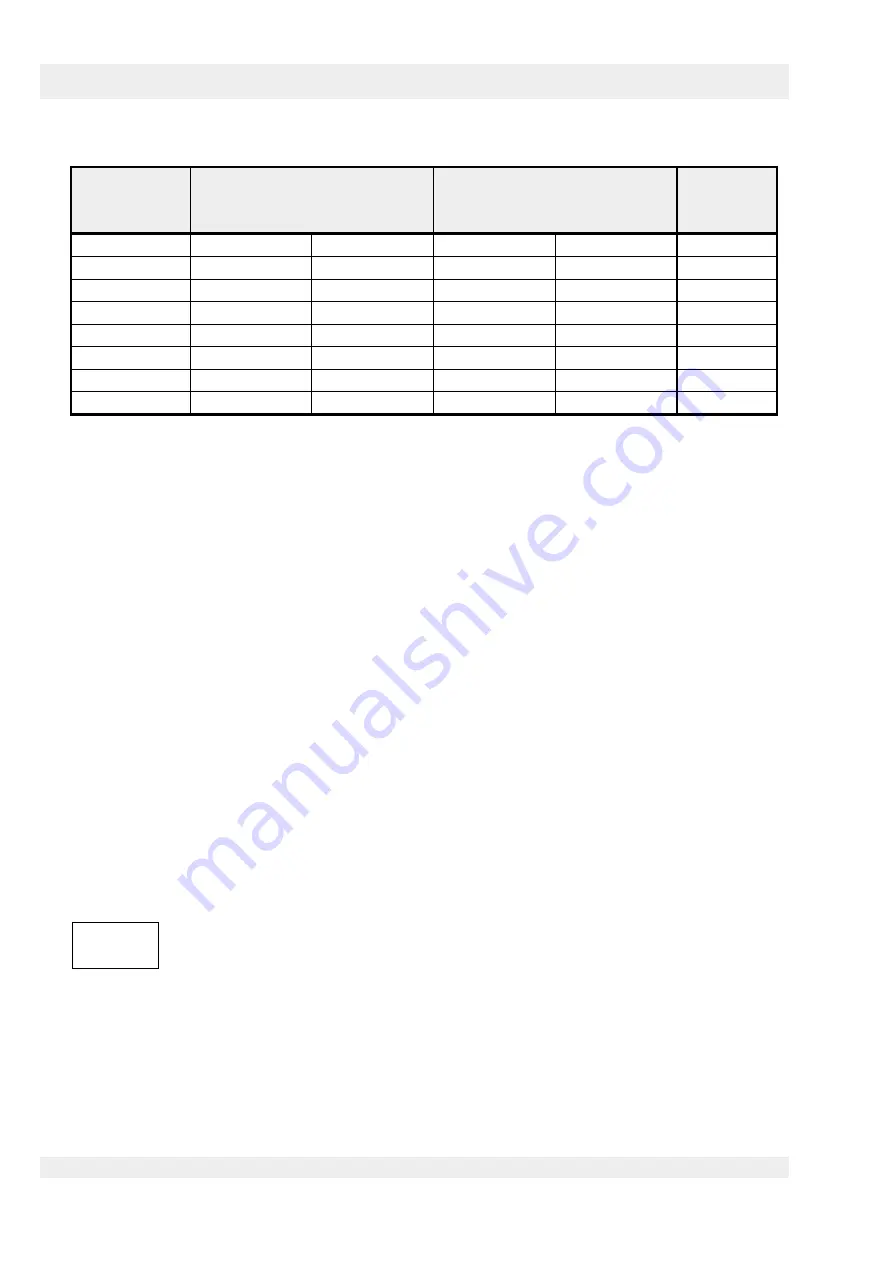
Operating instructions
Bearing sizes and oil quantities
Pump size
Grease lubrication
Bearing type
intake discharge
Oil lubrication
Bearing type
intake discharge
Qty.of oil
in litres
33 Pa
6305-2Z-C3
6305-2Z-C3
-
-
-
43 Pa *)
6306-2Z-C3
6306-2Z-C3
6306-C3
6306-C3
ca. 0.12
51 Pa *)
6307-2Z-C3
2x 7307 BG
6307-C3
2x 7307 BG
ca. 0.14
53 Pa *)
6307-2Z-C3
2x 7307 BG
6307-C3
2x 7307 BG
ca. 0.14
63 Pa *)
6307-2Z-C3
2x 7307 BG
6307-C3
2x 7307 BG
ca. 0.14
83 Pa *)
6308-2Z-C3
2x 7308 BG
6308-C3
2x 7308 BG
ca. 0.18
103 Pa *)
6308-2Z-C3
2x 7308 BG
6308-C3
2x 7308 BG
ca. 0.18
123 Pa
-
-
NU 310
2x 7310 BG
ca. 1.8
*) Standard design: grease lubrication
Special design: oil lubrication
The quantity of oil give applies for both bearing casings together.
Grease lubrication
Grease lubricants to be chosen from Table T 011-007 in Appendix.
The bearings are already filled with grease and are thus ready for use.
If the type of grease is changed, check that it is compatible with the left-over oil.
3. Transport, Handling, Storage
3.1 Transport, Handling
•
Check the pump/pump unit immediately upon delivery/receipt of despatch for damage or
missing parts.
•
The pump/pump unit must be transported carefully and by competent personnel. Avoid serious
impacts.
•
Keep the pump/pump unit in the same position in which it was supplied from the factory. Take
note of the instructions on the packaging.
•
The intake and discharge side of the pump must be closed with plugs during transport and
storage.
Dispose of all packing materials in accordance with local regulations.
•
Lifting devices (e.g. fork-lift truck, crane, crane device, pulleys, sling ropes, etc.) must be
sufficiently strong. The weight of the pump/pump unit is given in the Data Sheet.
•
The pump/pump unit may only be lifted by solid points such as the casing, flanges or frame. The
following illustration shows the correct method of carrying by crane.
Please
note
Pa 100/3-en
8