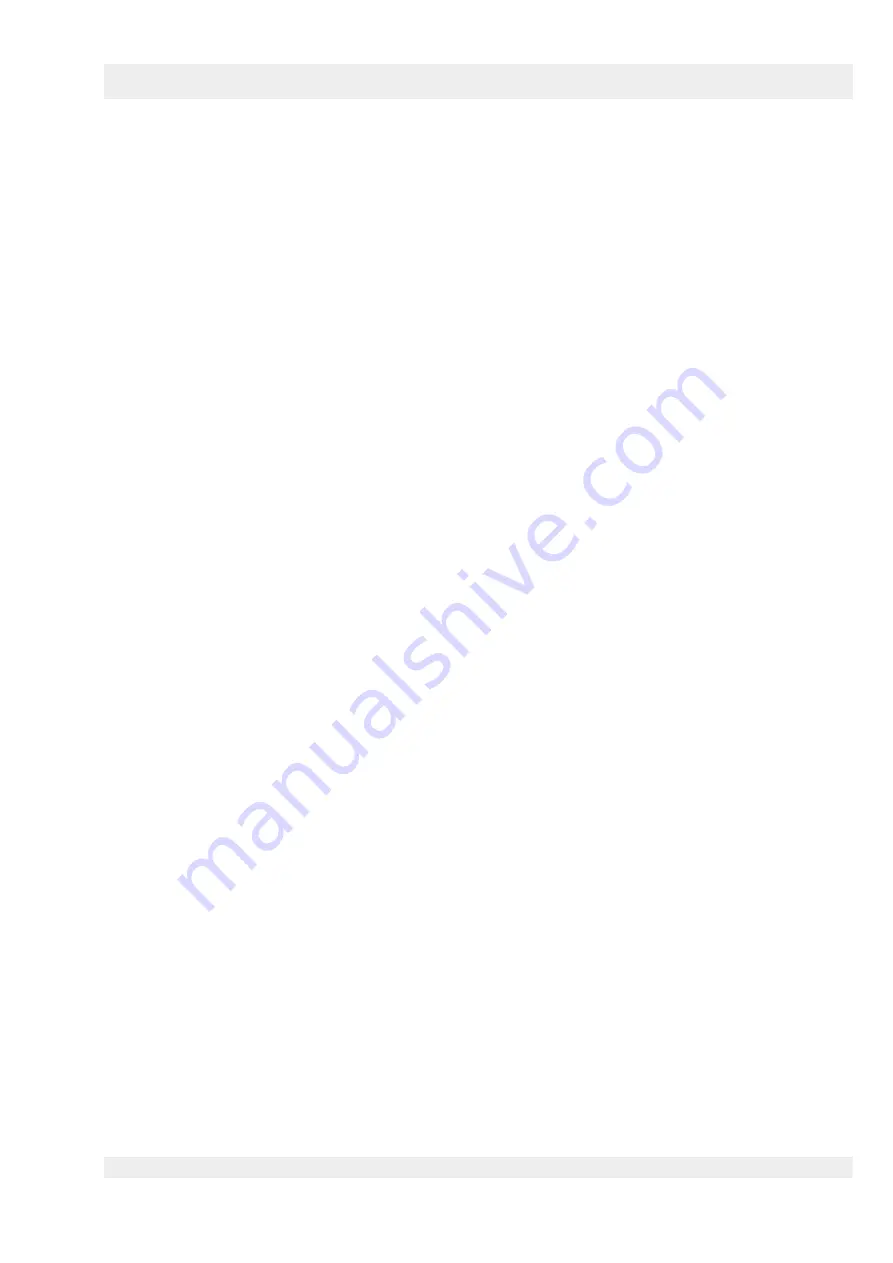
Operating instructions
Safety instructions for the operator
•
Depending on the operating conditions, wear and tear, corrosion or age will limit the working
life of the pump/pump unit, and its specified characteristics. The operator must ensure that
regular inspection and maintenance are carried out so that all parts are replaced in good time
which would otherwise endanger the safe operation of the system. If abnormal operation or any
damage are observed, the pump must cease operation immediately.
•
If the breakdown or failure of any system or unit could lead to people being hurt or property
being damaged, such system or unit must be provided with alarm devices and/or spare modules,
and they should be tested regularly to ensure that they function properly.
•
If there is any risk of injury from hot or cold machine parts, these parts must be protected against
contact by the user, or suitable warning signs must be affixed.
•
Contact protection on moving parts (e.g. coupling guards) must not be removed from systems
that are in operation.
•
If dangerous media (e.g. explosive, toxic, hot) leak out (e.g. from shaft seals), these must be
directed away so that there is no danger to people or the environment. The provisions of the law
must be observed.
•
Measures should be taken to exclude any danger from electricity (e.g. by complying with the
local regulations on electrical equipment). If work is carried out on live electrical components,
they should be unplugged from the mains or the main switch turned off and fuse unscrewed. A
motor protection switch is to be provided.
•
Basically, all work on the pump or pump unit should only be carried out when the pump is
stationary and not under pressure. All parts must be allowed to return to ambient temperature.
Make sure that no-one can start the motor during such work. It is essential that the procedure for
stopping the system described in the Operating Instructions is observed. Pumps or pump systems
that carry media that are dangerous to health must be decontaminated before being taken apart.
Safety Data Sheets for the various liquids handled. Immediately the work has been completed,
all safety and protective devices must be replaced or restarted.
•
Under EC Machinery Directives, every machine must be fitted with one or more emergency
command devices by which situations which represent an immediate danger or which could later
be dangerous can be avoided. This does not include machines in which the emergency switches
cannot reduce the danger, either because they do not reduce the time required to stop the
machine or because the do not allow the measures required by the danger to be taken. This
emergency switch must:
have controls that are clearly marked, easy to see and within easy reach;
stop the dangerous movement as quickly as possible without causing any additional danger;
trigger any specified safety movements or allow these to be started up.
If the emergency command device is no longer operated after an emergency „off“ switch has
been triggered, this must be maintained by blocking the emergency command device until it is
released again. It should not be possible to block the device without this triggering an emergency
„off“ switch. It should only be possible to release the device through an appropriate action; this
release should not start the machine up again - it should only make it possible to start it up again.
•
If the power supply is interrupted or restored after being interrupted or if it is changed in any
other way, this should not cause any danger (e.g. pressure surges).
Pa 100/3-en
5