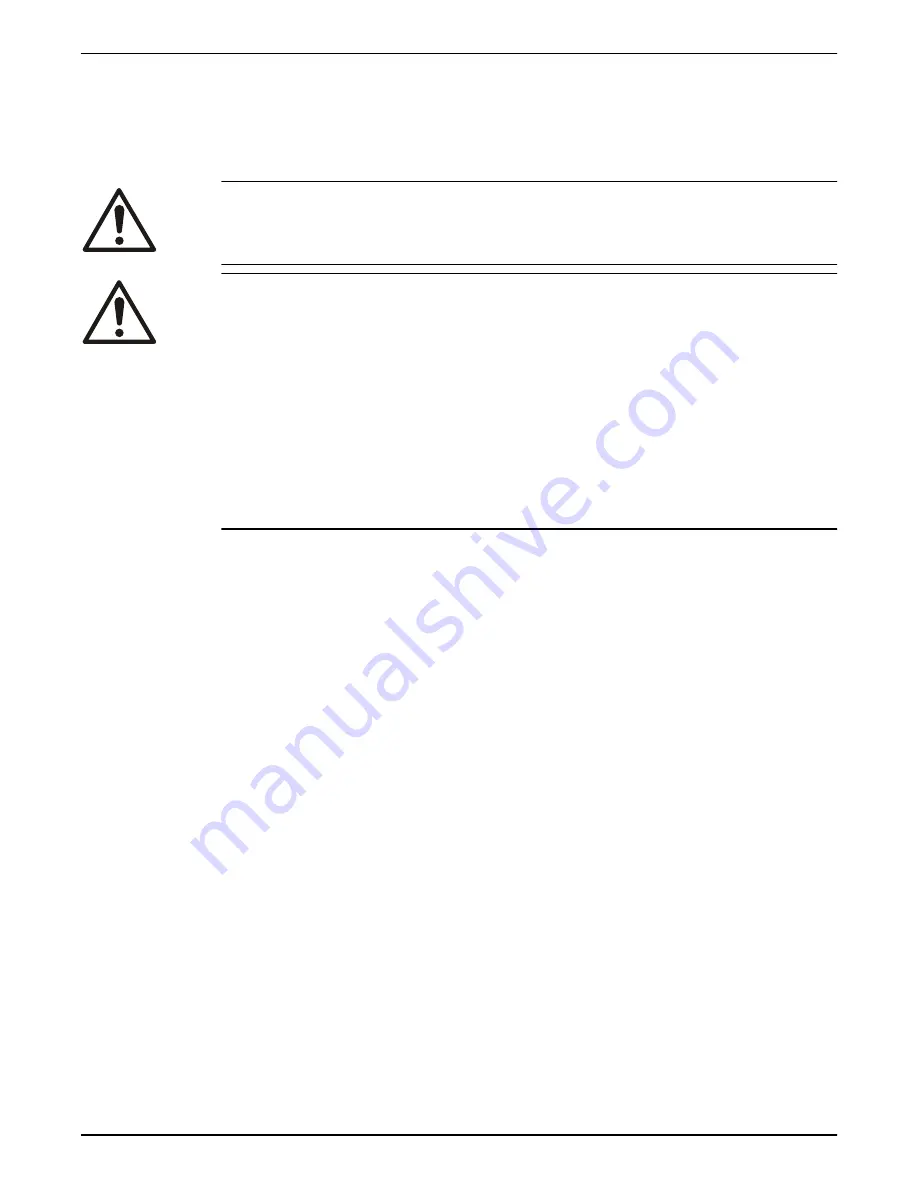
6 Maintenance
6.1 Precautions
DANGER:
Electrical hazard sufficient to kill. Always disconnect and lock out the power before you
service the unit.
WARNING:
• This manual clearly identifies accepted methods for disassembling units. These
methods must be adhered to. Trapped liquid can rapidly expand and result in a violent
explosion and injury. Never apply heat to impellers, propellers, or their retaining
devices to aid in their removal.
• Make sure that each pump and the package are isolated from the system and that
pressure is relieved before you disassemble the pump, remove plugs, open vent or
drain valves, or disconnect the package piping.
• Always disconnect and lock out power to the package and the driver before you
perform any installation or maintenance tasks. Failure to disconnect and lock out driver
power will result in serious physical injury.
• Crush hazard. The unit and the components can be heavy. Use proper lifting methods
and wear steel-toed shoes at all times.
6.2 Monthly maintenance
Motor lubrication checks
• For grease-filled bearings, make sure that grease is not all over the inside of the motor
and in the bottom of the motor. This could be a sign of overfilling. Refer to the
lubrication instructions from the motor manufacturer.
Close-coupled pumps
• For a horizontal pump, verify that the mechanical seal is not leaking between the pump
and the motor.
Sound and visual checks of the whole station
• Listen for any odd sounds that rub or grind, electrical arcing, and check for anything
that is binding or unusual. These conditions can indicate a serious problem.
Note that there is going to be some harmonic vibration with the pumps and motor.
Listen for excessive vibration or noise as this requires immediate service. Do not
operate the pump if there is excessive vibration.
• Confirm that the building cooling and ventilation systems are operating and clear of all
obstructions. The maximum operating range for equipment is 104°F (40°C).
• Verify that water, grease, oil, and hardware are not leaking or loose on the pump
station.
Station skid
• Visually inspect for leaks in the station piping, valves, and other components.
• Visually inspect the piping and skid for any stress cracks in the welds.
• Visually inspect the station for loose or damaged paint or areas of rust.
6 Maintenance
AquaBoost Advanced Pumping Packages INSTRUCTION MANUAL
23
Summary of Contents for Goulds AquaBoost Advanced
Page 1: ...INSTRUCTION MANUAL 10 001 326 AquaBoost Advanced Pumping Packages...
Page 2: ......
Page 34: ......
Page 35: ......