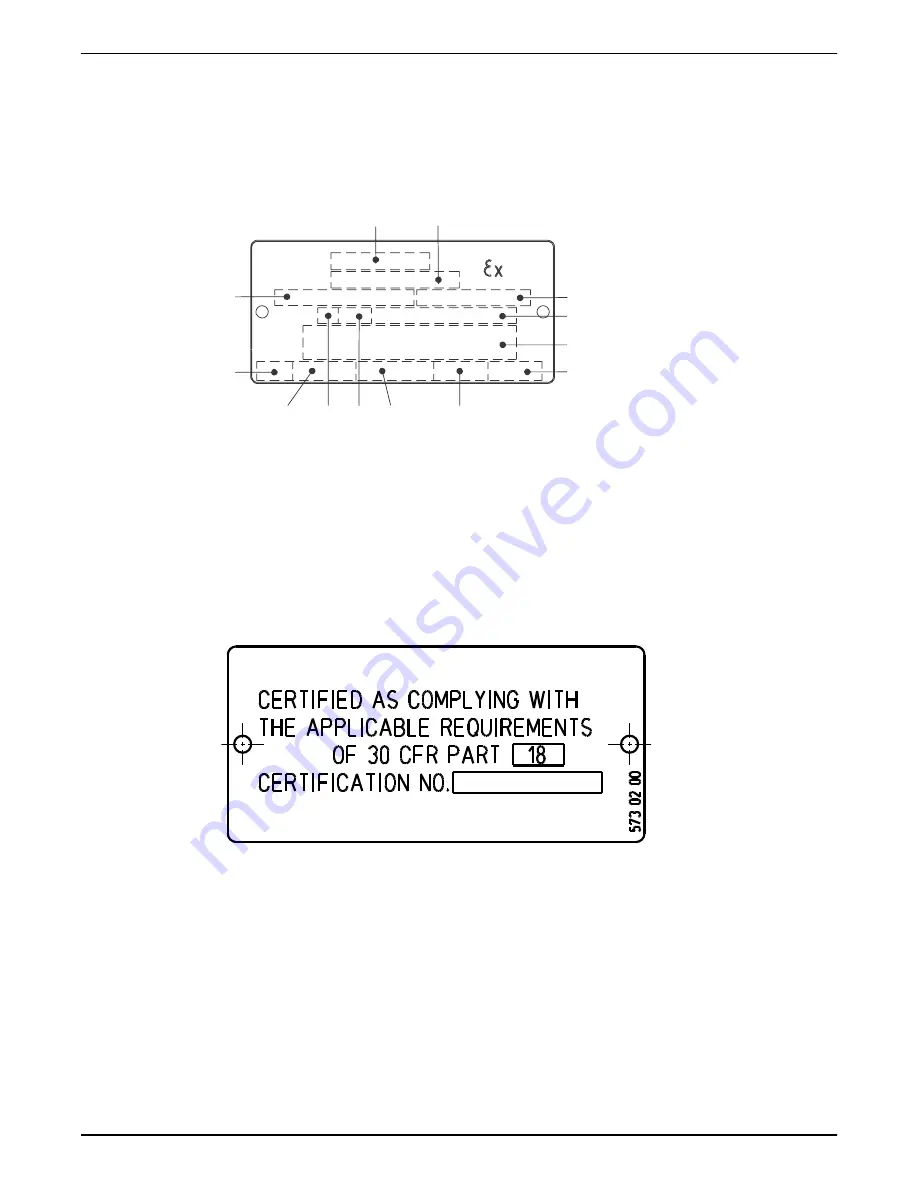
8.
Duty factor
9.
Input power
10. Rated speed
11. Controller
12. Additional information
13. Maximum ambient temperature
14. Serial number
15. ATEX marking
Figure 2: EN
WS001279B
2
1
8
7
6
3
4
5
9
10
11
12
13
1.
Approval
2.
Approval aut approval number
3.
Approved for drive unit
4.
Stall time
5.
Starting current/Rated current
6.
Duty class
7.
Duty factor
8.
Input power
9.
Rated speed
10. Controller
11. Additional information
12. Max. ambient temperature
13. Serial number
Figure 3: IEC
The MSHA approval plate
WS006211A
3.6 Product denomination
Reading instruction
In this section, code characters are illustrated accordingly:
X = letter
Y = digit
The different types of codes are marked up with a, b and c. Code parameters are marked
up with numbers.
3 Product Description
Flygt 2190, 2201 Installation, Operation, and Maintenance Manual
13