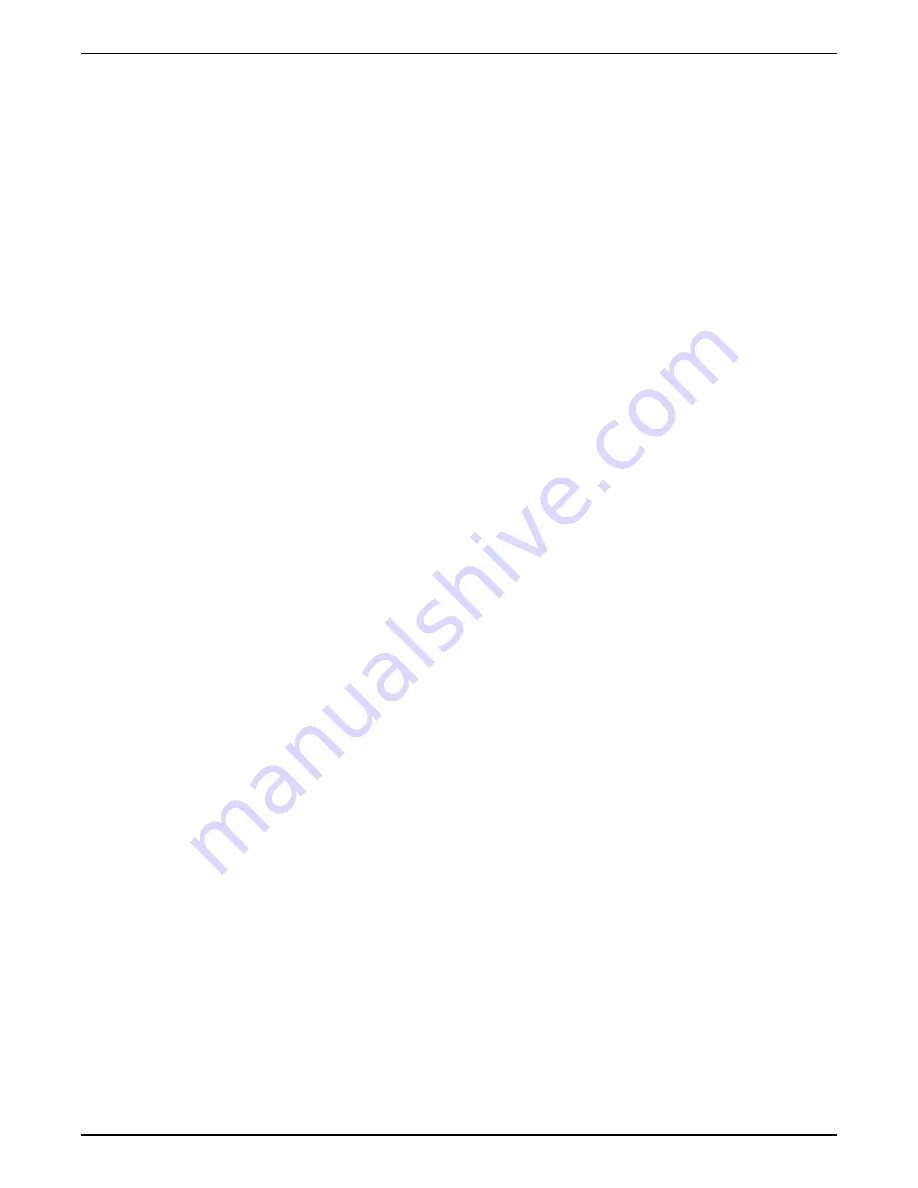
NOTE: Some settings made in the Start-Up Genie are not stored as a drive parameter.
These settings will not be copied to or from the LCP. These settings include Motor Type,
Operating Mode, Application Type, Number Feedback Sources and Number of Setpoints.
Be sure to enter the Start-Up Genie and configure these settings before using the Copy
Setup from LCP function.
The LCP can be used to store or save a parameter configuration. It is recommended to
copy all parameters to the LCP after commissioning the controller or prior to making
adjustments during troubleshooting. Select [Yes] from the menu in the Genie then and
press [OK] to begin copying parameters to the LCP. Parameter 0-50 LCP Copy can also be
used to copy all parameters from all setups to the LCP.
6.5.7 Automatic motor adaptation
Automatic motor adaptation (AMA) is a test procedure that measures the electrical
characteristics of the motor to optimize compatibility between the frequency converter
and the motor.
• The frequency converter builds a mathematical model of the motor for regulating
output motor current. The procedure also tests the input phase balance of electrical
power. It compares the motor characteristics with the data entered in parameters 1-20
to 1-25.
• The motor shaft does not turn and no harm is done to the motor while running the
AMA.
• Some motors may be unable to run the complete version of the test. In that case,
select
[2] Enable reduced AMA
.
• If an output filter is connected to the motor, select
Enable reduced AMA
.
• If warnings or alarms occur, see Warnings and alarms section for details.
• Run this procedure on a cold motor for best result.
NOTE: The AMA algorithm does not work when using PM motors.
To run AMA:
1. Press [Main Menu] to access parameters.
2. Scroll to parameter group 1–** Load and Motor
3. Press [OK].
4. Scroll to parameter group 1–2* Motor Data.
5. Press [OK].
6. Scroll to 1–29 Automatic Motor Adaptation (AMA).
7. Press [OK].
8. Select [1] Enable complete AMA.
9. Press [OK].
10.Follow on-screen instructions.
11.The test will run automatically and indicate when it is complete.
Date and time setting
The date and time can be set on the controller to help diagnostics and fault logging. To
set the clock, enter the parameter list by pressing [Main Menu]. Use the up and down
arrows to highlight 0-** Operation/Display menu and press [OK] to enter the menu. Next,
use the up and down arrows to highlight
0-7* Clock Settings
and press [OK] to select. Use
the up and down arrows to select parameter
0-70 Date and Time
. Press [OK] to enabling
editing of the Date and Time parameter. First set the time. Use the up and down arrows to
set the minutes. Then use the left arrow key to scroll left to the hours. Use the up and
down arrows to set the hour of the day. To change to PM, press the up arrow key until the
desired hours and the letter P (found between the minutes and day of the week) are
shown on the display. Next, scroll to the left to set the date. The day of the week on the
right side will update according to the date selected. Press [OK] to save the changes.
NOTE: If the power to the unit is lost, the date and time will reset to factory defaults.
Battery backup for real time clock is available on the Analog I/O Option Card (Input/
Output Option "A" or Repair part number 9K653).
6 Operation
Aquavar
®
Intelligent Pump Controller - 150 HP to 600 HP INSTRUCTION MANUAL
123
Summary of Contents for Aquavar
Page 1: ...INSTRUCTION MANUAL IM273 Rev C Aquavar Intelligent Pump Controller 150 HP to 600 HP...
Page 2: ......
Page 171: ......