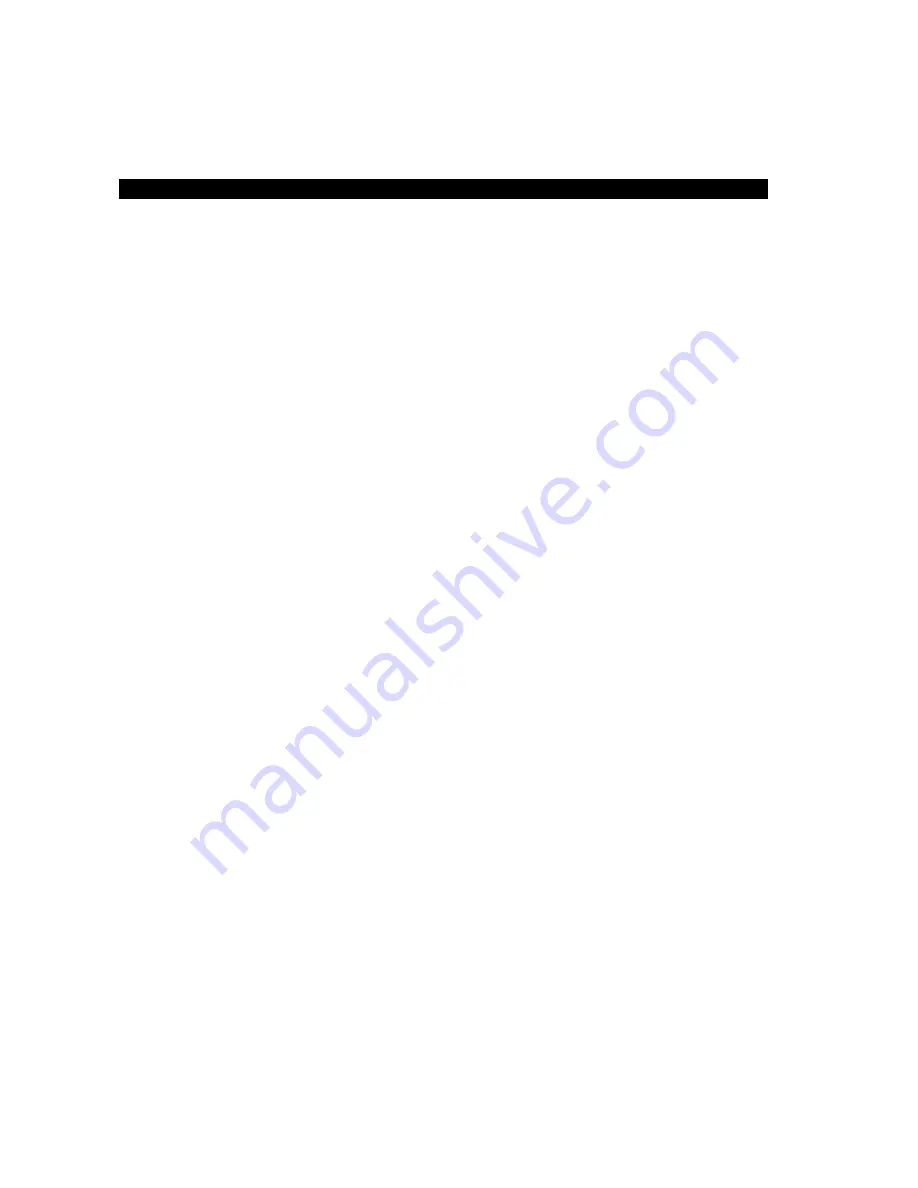
2. Installation
The rugged design of the SXT2011 allows it to be installed in most industrial
environments. Refer to the electrical and environmental specifications and tolerances
(pg. 1-4) for more detailed information.
System Power
It is a good practice to use isolation transformers on the incoming AC power line to the
system. An isolation transformer is especially desirable in cases in which heavy
equipment is likely to introduce noise onto the AC line. The isolation transformer can
also serve as a step-down transformer to reduce the incoming line voltage to a desired
level. The transformer should have a sufficient power rating (units of volt-amperes) to
supply the load adequately.
Proper grounding is essential to all safe electrical installations. Refer to the relevant
federal, state/provincial, and local electric codes, which provide data such as the size and
types of conductors, color codes and connections necessary for safe grounding of
electrical components. The code specifies that a grounding path must be permanent (no
solder), continuous, and able to safely conduct the ground-fault current in the system with
minimal impedance (minimum wire required is 18 AWG, 1 mm).
Observe the following practices:
•
Separate the power and ground (P. E., or Protective Earth) cable from signal cables at
the point of entry to the enclosure. To minimize the ground wire length within the
enclosure, locate the ground reference point near the point of entry for the plant
power supply.
•
All electrical racks or chassis and machine elements should be Earth Grounded in
installations where high levels of electrical noise can be expected. The rack/chassis
should be grounded with a ground rod or attached to a nearby Earth structure such as
a steel support beam. Connect each different apparatus to a single Earth Ground point
in a "star" configuration with low impedance cable. Scrape away paint and other
nonconductive material from the area where a chassis makes contact with the
enclosure. In addition to the ground connection made through the mounting bolt or
stud, use a one-inch metal braid or size #8 AWG wire to connect between each
chassis and the enclosure at the mounting bolt or stud.
Excessive Heat
To keep the temperature in range, the cooling air at the base of the system must not
exceed the maximum temperature specification (see pg. 1-4). Allocate proper spacing
between internal components installed in the enclosure.
When the air temperature is higher than the specified maximum in the enclosure (see
pg. 1-4), use a fan or air conditioner to lower the temperature.
2-1
Environmental Considerations