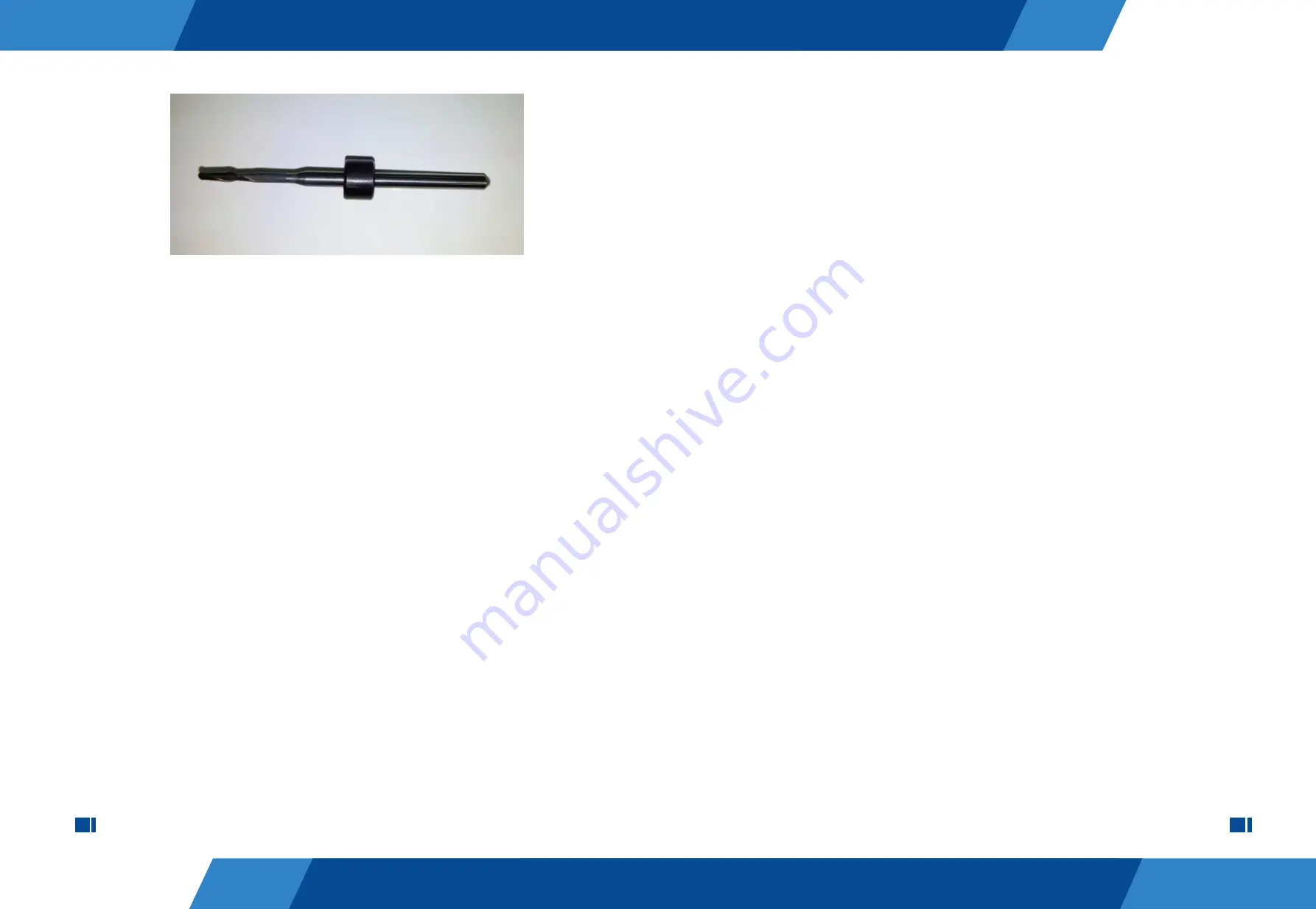
13
14
6. When the number of teeth engraved by the bur reaches 150 units, you need to strictly
monitor the bur edge and check if there is any breakage. If you have the 20X microscope,
you can check if there is any breakage to the bur coating and edge and the sharpness of
the bur. The quality of the machine needle must be ensured for the graving of high diffi-
culty.
7. Special notes for T3 bur
The T3 bur we offer is a very small bur (cutting diameter: 0.6mm), which is made of
materials of high hardness and low toughness.
You need to take care of the T3 bur and avoid applying force on it. Take care not to touch
the bur when cleaning up.
3-4 SPECIAL NOTES FOR LOADING MILLING MATERIAL
No matter what type of material is used, the following loading requirements must be
observed, in order to avoid any failure.
1. No residual dust is allowed on the clamp, which shall be cleaned each time when
loading the material.
2. Do not use the clamp with any defect, such as the bulging caused by bumping.
3. No residual dust is allowed on the edge of the material when it is installed. Be sure to
clean it, in order to avoid the breakage caused by uneven force during the installation.
4. When tightening the clamp, be sure to evenly tightening each screw. Do not fully
tighten a screw and then tighten other screws. It will cause uneven force to break the
material or cause internal stress which results in breakage during the processing.
3-5 Trouble shooting
System information will be displayed on the screen during milling process. In case of
any abnormality, the system will show error information on the screen. To ensure
safety, most operations are accepted by the system only in normal situation. When you
conduct the relevant operation in abnormal situation, the system will generate corre-
sponding prompts.
Therefore, when there is any exception prompt, you can click “reset” button to reset the
relevant exception. If the exception still exists after the reset operation, you need to
take the corresponding troubleshooting measures according to the exception message
and prompts, and then execute the reset or restart the software to remove the excep-
tion message.