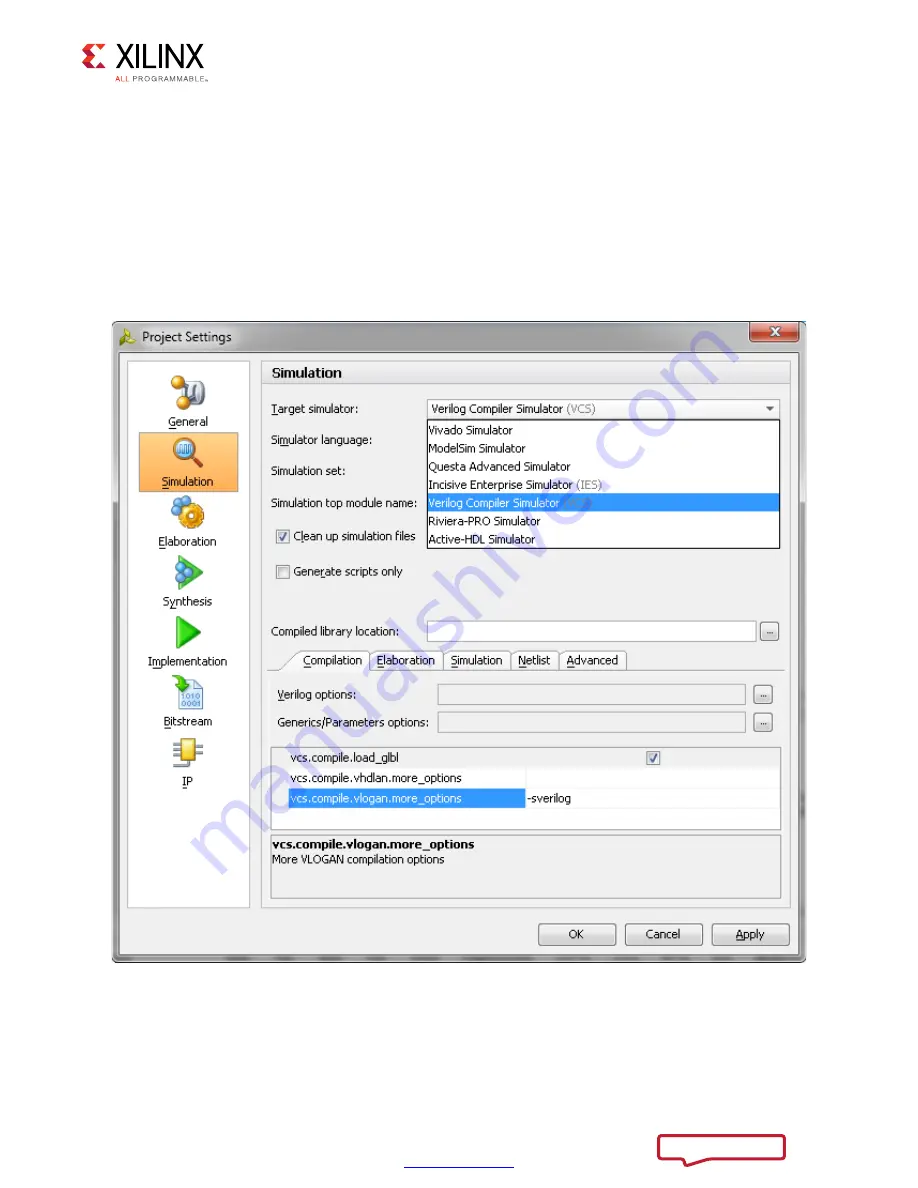
Zynq-7000 AP SoC and 7 Series FPGAs MIS v4.1
86
UG586 November 30, 2016
Chapter 1:
DDR3 and DDR2 SDRAM Memory Interface Solution
a. Browse to the
Compiled libraries location
and set the path on
Compiles libraries
location
option.
b. Under the
Compilation
tab, set the
vcs.compile.vlogan.more_options
to
-sverilog
.
c. Under the
Simulation
tab, set the
vcs.simulate.runtime
to 1 ms (there are
simulation RTL directives which stop the simulation after a certain period of time
which is less than 1 ms) as shown in
3. Apply the settings and select
OK
.
4. In the
Flow Navigator
window, select
Run Simulation
and select
Run Behavioral
Simulation
as shown in
X-Ref Target - Figure 1-49
Figure 1-49:
Simulation with VCS