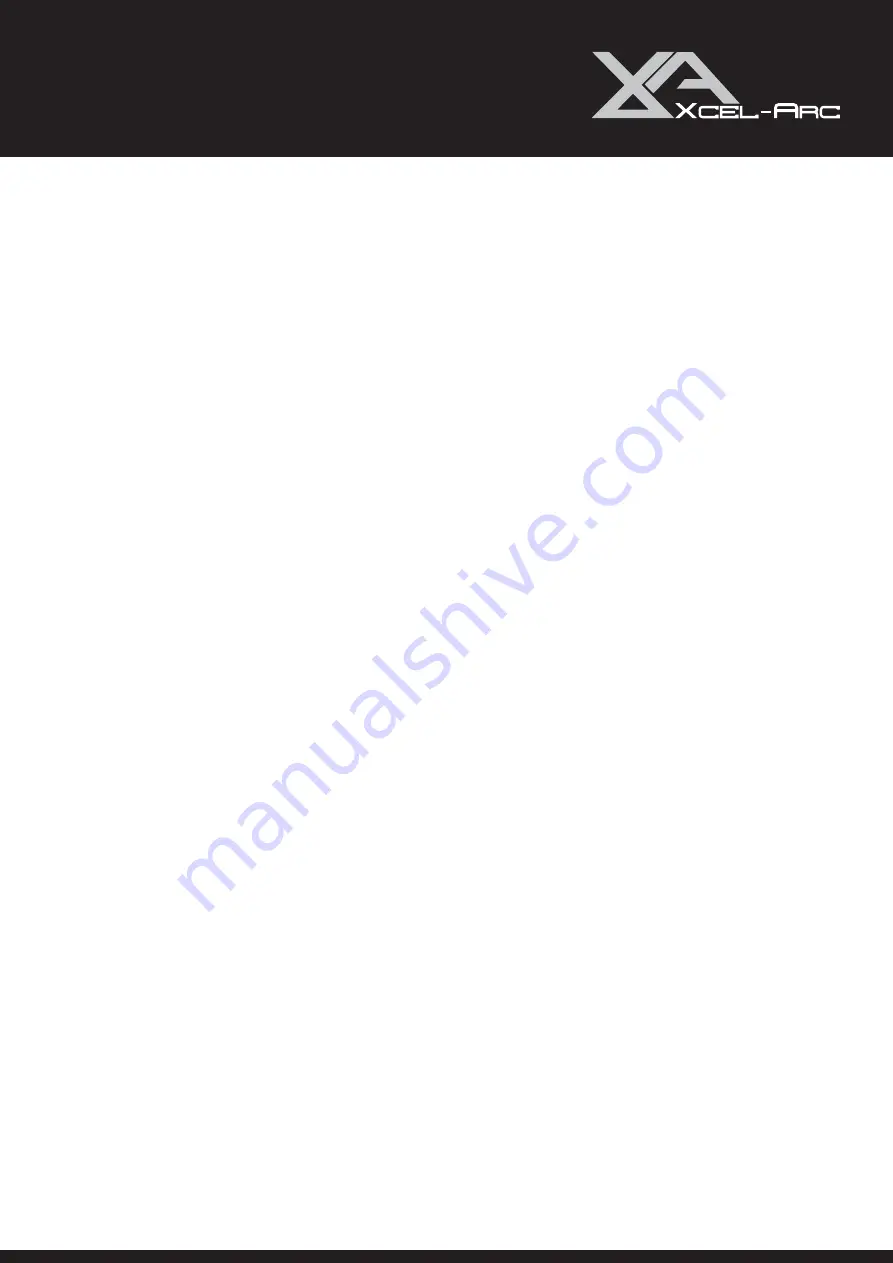
CAUTION
1. Working Environment.
i.
The environment in which this welding/cutting equipment is installed must be free of grinding dust, corrosive chemicals, flammable gas or
materials etc, and at no more than maximum of 80% humidity.
ii.
When using the machine outdoors protect the machine from direct sun light, rain water and snow etc; the temperature of working environment
should be maintained within -10°C to +40°C.
iii.
Keep this equipment 30cm distant from the wall.
iv.
Ensure the working environment is well ventilated.
2. Safety Tips.
i. Ventilation
This equipment is small-sized, compact in structure, and of excellent performance in amperage output. The fan is used to dissipate heat
generated by this equipment during the welding/cutting operation. Important: Maintain good ventilation of the louvres of this equipment. The
minimum distance between this equipment and any other objects in or near the working area should be 30 cm. Good ventilation is of critical
importance for the normal performance and service life of this equipment.
ii. Thermal Overload protection.
Should the machine be used to an excessive level, or in high temperature environment, poorly ventilated area or if the fan malfunctions the
Thermal Overload Switch will be activated and the machine will cease to operate. Under this circumstance, leave the machine switched on to
keep the built-in fan working to bring down the temperature inside the equipment. The machine will be ready for use again when the internal
temperature reaches safe level.
iii. Over-Voltage Supply
Regarding the power supply voltage range of the machine, please refer to “Main parameter” table. This equipment is of automatic voltage
compensation, which enables the maintaining of the voltage range within the given range. In case that the voltage of input power supply
amperage exceeds the stipulated value, it is possible to cause damage to the components of this equipment. Please ensure your primary
power supply is correct.
iv.
Do not come into contact with the output terminals while the machine is in operation. An electric shock may possibly occur.
MAINTENANCE
Exposure to extremely dusty, damp, or corrosive air is damaging to the welding/cutting machine. In order to prevent any possible failure or fault of this welding/
cutting equipment, clean the dust at regular intervals with clean and dry compressed air of required pressure.
Please note that:
lack of maintenance can result in the cancellation of the guarantee; the guarantee of this welding/cutting equipment will be void if the
machine has been modified, attempt to take apart the machine or open the factory-made sealing of the machine without the consent of an authorized
representative of the manufacturer.
TROUBLE SHOOTING
Caution:
Only qualified technicians are authorized to undertake the repair of this welding/cutting equipment. For your safety and to avoid Electrical
Shock, please observe all safety notes and precautions detailed in this manual.
INSTALLATION & OPERATION
Please install the machine strictly according to the steps. The protection class of this machine is IP21S, so avoid using it in rain.
CONNECTION OF INPUT CABLES
Primary input cable is supplied with this welding equipment. Connect the primary input cable with power supply of required input voltage. Refer to data
plate on machine for Input voltage, IMAX and IEFF.
EMC DECLARATION
IEC 60974-10:2007
Arc Welding equipment - Part 10: Electromagnetic compatibility (EMC) requirements (Classification of ISM Equipment - According to IEC 60974-
10:2007 and CISPR 11: 2033+A1:2004 Clause 4.1 and 4.2. The EUT Belongs to Apparatus Group2 Class A)
6
|
RAZORWELD™ ARC 630 - MMA/CAG/TIG Welder Manual
SAFETY