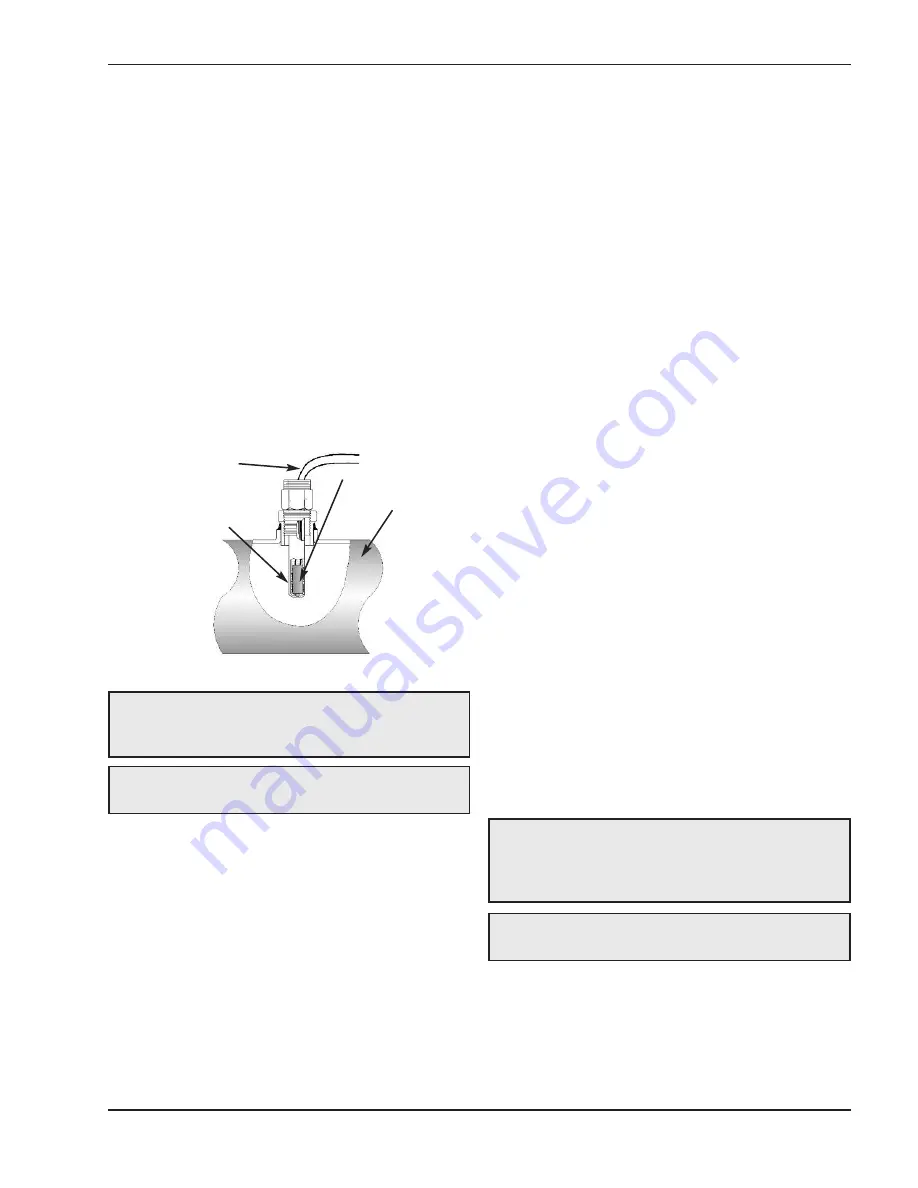
23
Heating Sensor Installation
1. Only use the System sensor provided with the
unit.
2. The sensor wires can be extended up to 500 ft
using a shielded 2-conductor cable.
3. Do not run sensor wires in conduit with line voltage
wiring.
4. Install a 3/8” ID 1/2 NPT immersion well.
5. If installing the system sensor on the supply, insert
the sensor in a well with heat paste no more than
5 ft past the boiler loop outlet on the common sup-
ply header, but before any major takeoffs. The
sensor must be located where it sees the output of
all the boiler stages. If a boiler is piped so that the
sensor does not see its output. the VERSA IC
®
will
not sequence the boilers correctly.
Wiring the Outdoor Sensor
1. There is no connection required if an outdoor sen-
sor is not used in this installation.
2. If using an Outdoor Sensor, connect the sensor
wires to the terminals marked OUTDOOR SEN-
SOR (see wiring diagram). Caution should be
used to ensure neither of these terminals
becomes connected to ground.
3. Use a minimum 18 AWG wire for runs of up to 150
feet.
4. Mount the outdoor sensor on an exterior surface of
the building, preferably on the north side in an
area that will not be affected by direct sunlight and
that will be exposed to varying weather conditions.
Wiring the Indirect Sensor
1. There is no indirect sensor connection required if
an indirect water heater is not used in the installa-
tion.
2. When the Indirect DHW call for heat is active, the
PIM communicates this to the VERSA. The
VERSA calculates the optimal operation and
sends the firing rate and pump output requests to
the PIM so it can activate the Indirect DHW pump
and Boiler pump if needed. If an optional Indirect
DHW sensor is connected to J2-1 and J2-2 the
PIM will pass this signal to the VERSA. This allows
the VERSA to optimize the Indirect DHW demand
to maintain the Indirect DHW setpoint. The Indirect
DHW thermostat switch closure is not required
when using the Indirect DHW sensor. If a VERSA
is not present the PIM shall activate the Indirect
DHW pump whenever the Indirect DHW call is
active. The Boiler pump may also be activated
based on the Indirect DHW piping configuration
setting.
3. Connect the indirect tank sensor to the terminals
marked INDIRECT DHW SENSOR (see wiring
diagram). Caution should be used to ensure nei-
ther of these terminals becomes connected to
ground. When using an indirect DHW sensor to
control tank temperature, contact closure is
required across the indirect DHW override con-
nections. To ensure proper operation during “limp
along” mode set PIM operator dial to be equal to
DHW Target temperature condition from occurring.
See VERSA IC manual, catalog 5000.72.
Wiring the Optional 0–10 Volt
Building Control Signal
1. A signal from an energy management system may
NOTE:
Alternately, a thermostat contact closure can
be used in lieu of the sensor for indirect operation.
Connect the thermostat to the terminals marked IND
REMOTE THERMOSTAT.
NOTE:
If the System Sensor (S3) can not sense the
correct water temperature, the VERSA IC
®
will not
provide comfortable heat levels.
WARNING:
Use only the System and Outdoor Air
sensors included with the control.
CAUTION:
Sensor and control wiring must
NOT
be
run in conduit or chases with line voltage.
Fig. 19: System Sensor (S3)
Heating
System
Sensor
Immersion Well
3/8” ID 1/2 NPT
Common
Supply Pipe
Sensor
Probe