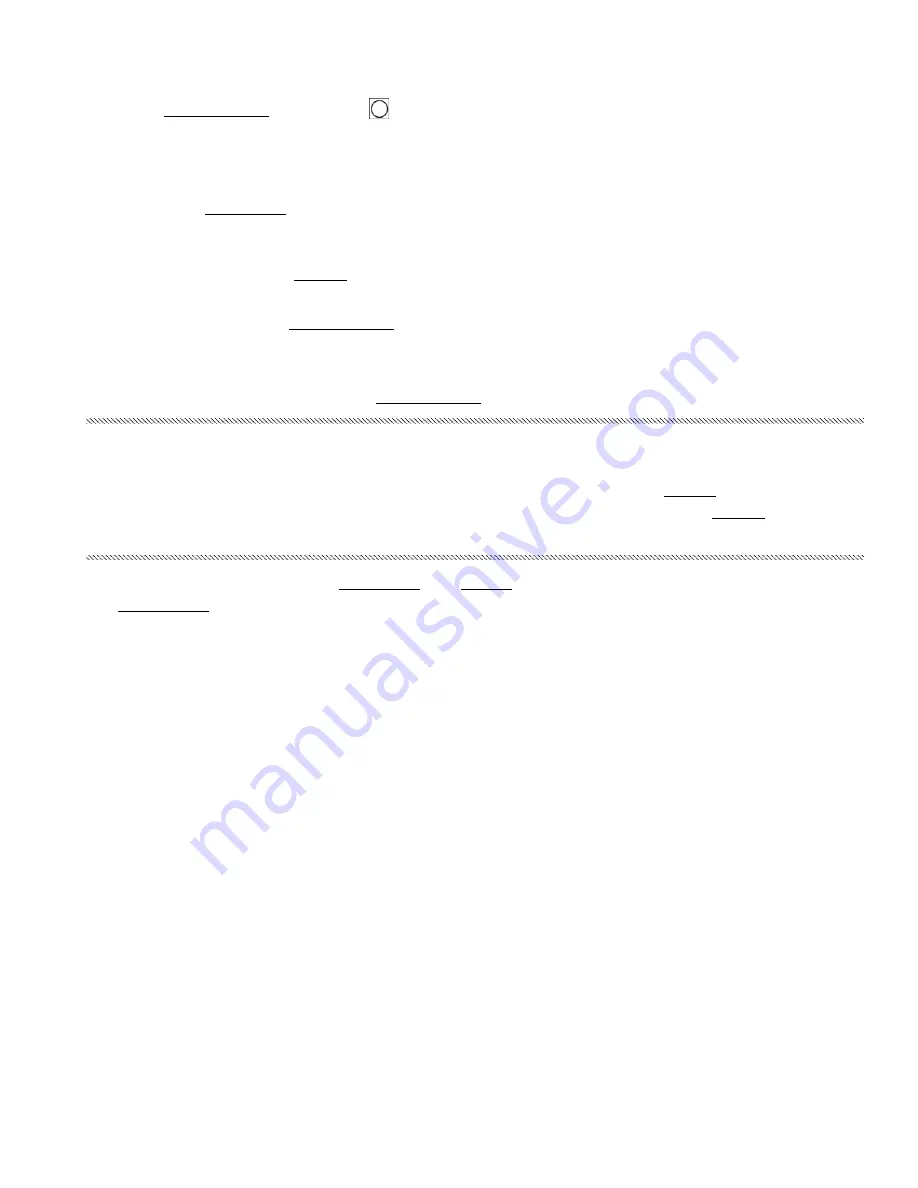
Rev 2.0/4-16
15
MRPT1211LAC: #35063
A
FTER
U
SING THE
L
IFTER
Place the power switch in the OFF ( ) position.
CAUTION: Do not set the lifter against any surfaces which could soil or damage the
vacuum pads.
Built-in parking feet can be used to support an unloaded lifter when not suspended from a crane:
Make sure the pad frame is oriented vertically with the parking feet at the bottom. Use the
hoisting equipment to gently lower the lifter until the parking feet support its entire weight.
Make sure the lifter leans securely against an appropriate support; then detach the hoisting
equipment hook from the lift bail.
If the lifter is transported to another location, use the original shipping container and secure the
lifter so as to protect the vacuum pads and all other components from damage while in transit.
Storing the Lifter
Use the covers supplied to keep the vacuum pads clean.
!!-CE-!! In accordance with CE Standard EN 13155, the lifter is designed to rest on relatively
horizontal surfaces without tipping over. To store the lifter in this way, set the lifter with the
pads facing downward on a clean, smooth, flat surface. Then lower the lift bar to a horizontal
orientation (see OPERATION: T
O
T
ILT THE
L
OAD
) and place a support under the lift bail. However,
see the Note immediately following.
Note: Storing the lifter with its pad frame and lift bar in the horizontal orientation could damage
the tilt actuator, if the lift bar is not supported. Avoid placing the lifter in this position; or if this is
unavoidable, place a support under the lift bar. Also be sure to provide manual assistance to the
tilt actuator when raising the lift bar to the vertical position (see ASSEMBLY).
Summary of Contents for MRPT1211LAC
Page 2: ......
Page 31: ...Rev 2 0 4 16 29 MRPT1211LAC 35063 ...
Page 32: ...Rev 2 0 4 16 30 MRPT1211LAC 35063 ...
Page 33: ...Rev 2 0 4 16 31 MRPT1211LAC 35063 ...
Page 34: ...Rev 2 0 4 16 32 MRPT1211LAC 35063 ...
Page 35: ...Rev 2 0 4 16 33 MRPT1211LAC 35063 ...
Page 36: ...Rev 2 0 4 16 34 MRPT1211LAC 35063 ...