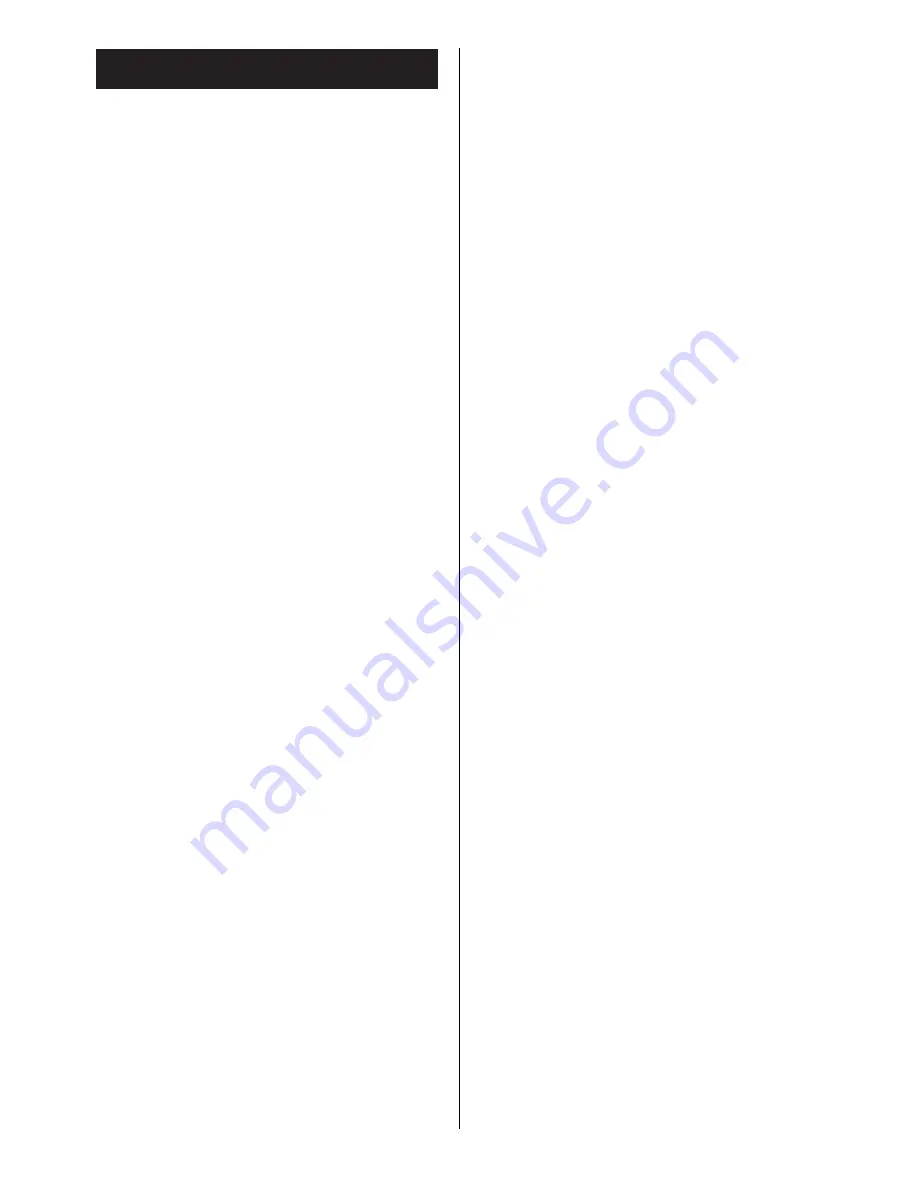
The appliance is supplied suitable for fitting to a sealed system. If
it is to be fitted to an open vent system refer to paragraph 11.3
and Section 8.
11.1 FLUE OPTIONS:
Refer to Section 5b and Fig. 5..
IMPORTANT:
Two standard flue kits are available for the
appliance:
1) Standard Horizontal Rear Flue Kit.
The maximum flue length when measured from the
REAR
of the
appliance casing is 500 mm. See Fig. 5 Frame 1.
2) Standard Horizontal Side Flue Kit.
The maximum flue length when measured from the
SIDE
of the
appliance casing is 950 mm. See Fig. 5 Frame 2.
EXTENSION FLUE KITS.
Extension flue kits and 90° flue bends are available to increase
the length and redirect the flue as follows:
(a) From the standard flue length up to 3000 mm straight flue.
(b) From the standard flue length to up 2300 mm when a
second 90° flue bend is required.
(c) From the standard flue length up to 1000 mm when a
second and third 90° flue bend is required.
Refer to Section 3, Table 2 and Section 5b, Flue Options, to
determine whether an extension flue kit or kits and an extra 90°
flue bend or bends are required.
IMPORTANT:
Extension flue kits,extra 90° flue bends, flue
adaptor, flue spacer and air duct supports are all optional extras.
All the extras required for the installation must be available
before continuing. Refer to Section 5b.
VERTICAL BALANCED FLUE OPTION.
A vertical balanced flue option is available. Instructions
describing the fitting of the vertical balanced flue system are
sent with the vertical flue terminal assembly.
The flue must be installed as specified in BS 5440 Part 1.
11.2 GENERAL FITTING.
The following description covers one method of installation.
Extra space may be required for installation if connections are
made in a different way.
Compression fittings may be used on all water connections to
allow for the fitting of the appliance and servicing.
Pipework must be routed so as not to obstruct access to the
circulating pump, diverting valve, gas valve, water to water heat
exchanger or heat bank.
Removable sections are provided in the cabinet top panel to
facilitate vertical pipe connections and the flue system,if
required.
Alternatively, removable sections are provided in the side panels
to accommodate the side flue system.
Check the appliance carton contains :
Installer’s Instruction Pack.
User’s Information Pack.
Hardware Pack with flue restrictor rings.
Appliance.
Carefully remove the appliance from the cardboard package and
plinth.
Check the position chosen for the appliance is in accordance with
the instructions given in Sections 4 and 5a. Also refer to Fig. 2.
Do not place the appliance in its final position at this stage.
For all flue options from the dimensions given in Fig. 13 carefully
mark out:
(i) the wall with the centre-lines for the Rear Flue centre point
position.
(ii) the floor with the base outline of the appliance.
Before continuing with the installation it will be necessary to
decide which flue option is suitable. Refer to Section 5b and
Fig. 5.
Having decided upon the most suitable flue option for the
installation, the position of the hole for the flue must now be
marked on the wall/walls.
FLUE OPTION 1.
See Fig. 5.
The location of the centre point position for the Rear Flue is
obtained from the flue centre-lines previously marked.
This is the Rear Flue centre point position. See Fig. 13.
FLUE OPTION 2.
See Fig. 5.
Draw a horizontal line from the Rear Flue centre point position in
the appropriate direction along the wall. Check that it remains
horizontal. Measure 94 mm from the junction of the walls and
make a short vertical line. Extend the horizontal line to intersect
the vertical line and mark the position.
This is the Side Flue centre point position. See Fig. 13.
FLUE OPTION 3.
See Fig. 5.
The location of the centre point position for the Rear Flue is
obtained from the flue centre-lines previously marked.
If the flue duct extends through other walls ensure it remains
horizontal.
Measure the rear flue centre point position from the floor and
transfer this dimension to the appropriate wall where the flue
will terminate. Mark the wall to suit the installation.
This is the Rear Flue Extension centre point position. See Fig. 13.
FLUE OPTION 4.
See Fig. 5.
Draw a horizontal line from the Rear Flue centre point position,
previously marked, in the appropriate direction along the
wall/walls. Ensure it remains horizontal.
If the flue system extends through other walls or the appliance is
not installed close to a wall, ensure it remains horizontal.
Measure the rear flue centre point position from the floor and
transfer this dimension to the appropriate wall where the flue
will terminate.
Measure 94 mm from the junction of the walls if the appliance is
installed against a wall and make a short vertical line.
If the appliance is
NOT
installed against a wall, measure the
distance from the junction of the walls, make a short vertical line
to suit the installation. Extend the horizontal line to intersect the
vertical line and mark the position.
This is the Side Flue Extension centre point position. See Fig. 13.
FLUE OPTION 5.
See Fig. 5.
Draw a horizontal line from the Rear Flue centre point position,
previously marked, in the appropriate direction along the
wall/walls. Check that it remains horizontal.
If the flue system extends through other walls or the appliance is
not installed close to a wall, ensure it remains horizontal.
Measure the rear flue centre point position from the floor and
transfer this dimension to the appropriate wall as necessary.
Mark the wall where the flue will terminate to suit the
installation.
This is the Side Flue Extension centre point position. See Fig. 13.
FLUE OPTION 6.
See Fig. 5.
Draw a vertical line upwards from the Rear Flue centre point
position previously marked. Extend the line, approximately 250
mm, above the position required for the centre-line of the
horizontal flue duct. See Fig. 13.
Mark the position on the vertical line to coincide with the centre-
line position of the horizontal duct.
This is the Rear Flue Upwards Extension centre point
position. See Fig. 13.
FLUE OPTION 7.
See Fig. 5.
Follow the procedure as described in Flue Option 5 ensure the
flue system remains horizontal.
11. Installing The Appliance
16