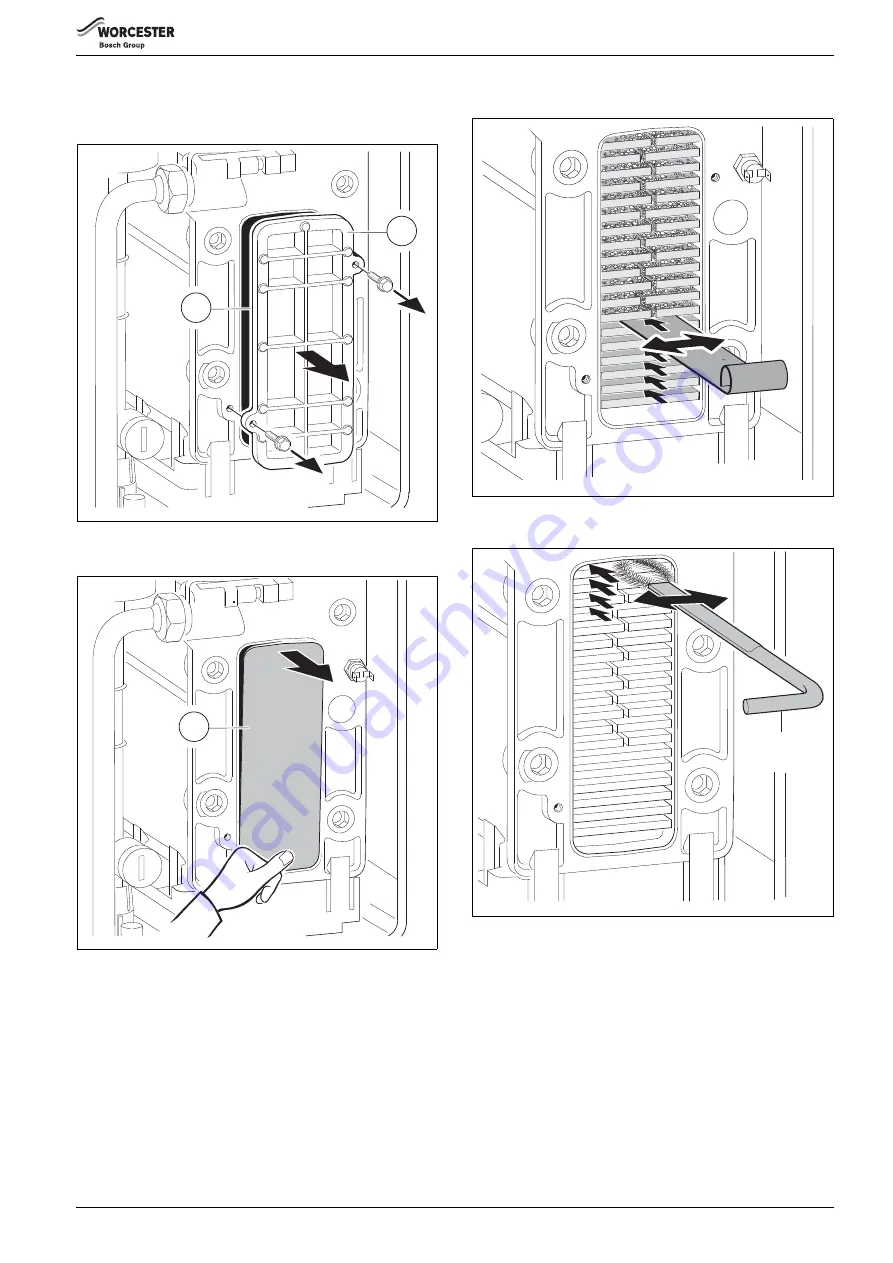
SERVICING AND SPARES
6720818077 (2016/04) -
Greenstar Highflow CDi
ErP
35
If the Heat Exchanger requires cleaning:
▶ Remove the condensate trap.
▶ Remove the cleaning access cover [1] and seal [2].
Fig. 51 Remove cover
▶ Press at the bottom to remove the metal plate [3], if fitted.
Fig. 52 Remove metal plate
▶ Using the cleaning blade, working from the bottom to the top, to
loosen any deposits in the heat exchanger.
Fig. 53
▶ Using the brush, clean the heat exchanger from top to bottom.
Fig. 54
▶ Use the handle of the brush to remove debris from the condensate
tray.
▶ Place a suitable container under the sump condensate outlet to
collect any water and debris.
6720818079-17.1Wo
1
2
6720818079-18.1Wo
3
6720818079-23.1Wo
6720818079-20.1Wo