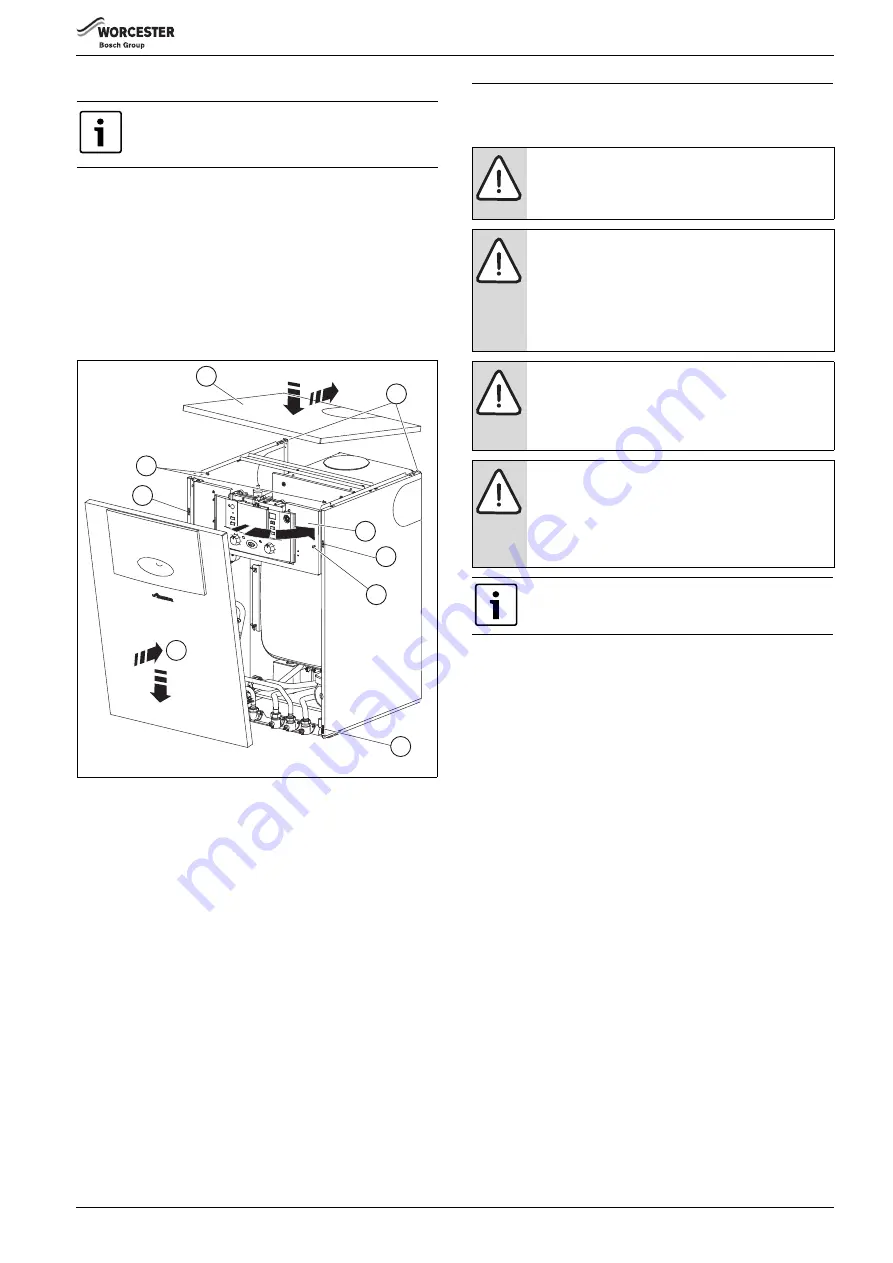
SERVICING AND SPARES
6720818077 (2016/04) -
Greenstar Highflow CDi
ErP
31
5.7
Finishing commissioning
1. Engage top panel [2] onto rear retainers [3] and lower front of panel
into position.
▶ Secure the top panel with the two screws [4].
2. Swing the control panel assembly [5] into the boiler.
▶ Secure with the screw [6].
3. Locate the bottom corners of the front panel [1] into retaining lugs
[7].
▶ Push the top of front panel [1] in to engage with the two ball catches
[8].
Fig. 42 Finishing commissioning
HANDOVER:
▶ Complete the Benchmark log book at the rear of the manual.
▶ Set up the controls and show the user how to operate all the controls
shown in the User Guide.
▶ Instruct the user how to repressurise the system.
▶ If the appliance is unused and exposed to freezing conditions, advise
the user of the precautions necessary to prevent damage to the
boiler, system and building.
In the event of the appliance being inoperative, isolate the boiler and
drain the system and boiler.
6
SERVICING AND SPARES
6.1
Inspection and service
• To ensure the continued efficient operation of the appliance it must
be checked at regular intervals.
• The frequency of servicing will depend upon the particular
installation conditions and usage however, an annual service is
recommended.
• The extent of the service required by the appliance is determined by
the operating condition of the appliance when tested by fully
qualified engineers.
Inspection
1. Check that the terminal and the terminal guard, if fitted, are clear
from any obstructions and undamaged.
2. If the appliance is in a compartment or cupboard check that the
specified service space around the appliance is clear.
3. Check all the joints and connections in the system and remake any
that show signs of leakage. Refill and re-pressurise if applicable as
described in Commissioning.
4. Operate the appliance and take note of any irregularities. Call up the
last fault stored by the Bosch Heatronic control, Service Function
‘6A’.
Refer to Fault Finding on page 43 for rectification procedures.
Max pressure
▶ When the heating system water is at maximum temperature, 2.5 bar
must not be exceeded. If this pressure is exceeded then an additional
expansion vessel must be fitted into the system return as close as
possible to the appliance.
▶ If the system does not retain the pressure, the pressure relief valve
(PRV) and the heating system should be checked for leaks.
At the time of commissioning, complete all relevant
sections of the Benchmark Checklist located on the
inside back pages of this document.
6720818077-23.1W
o
2
1
8
8
3
5
4
6
7
CAUTION:
ISOLATE THE GAS SUPPLY
▶ Ensure that the gas supply is safely Isolated and
secured to prevent inadvertent re-connection.
Follow all relevant safety precautions
CAUTION:
ISOLATE THE 230V ELECTRICITY SUPPLY
▶ Ensure that the electricity supply is safely Isolated
and secured to prevent inadvertent re-connection.
Information on safe isolation can be found in the
Health and Safety Executive guidance HSG85.
Using test equipment approved to GS38 confirm that
the electricity supply is disconnected
NOTICE:
COMPONENTS.
▶ After replacement of any components always check
for gas tightness where relevant and carry out
functional checks as described in Commissioning.
Damaged O-rings or gaskets must be replaced.
NOTICE:
SERVICE WORK
▶ SERVICE WORK MUST
NOT
BE ATTEMPTED IF A CO/
CO
2
ANALYSER IS
NOT
AVAILABLE.
▶ Service work must be carried out by a competent
registered gas engineer, such as British Gas or Gas
Safe registered engineer!
After servicing, complete the relevant Service Interval
Record section of the Benchmark Checklist located on
the inside back pages of this document.