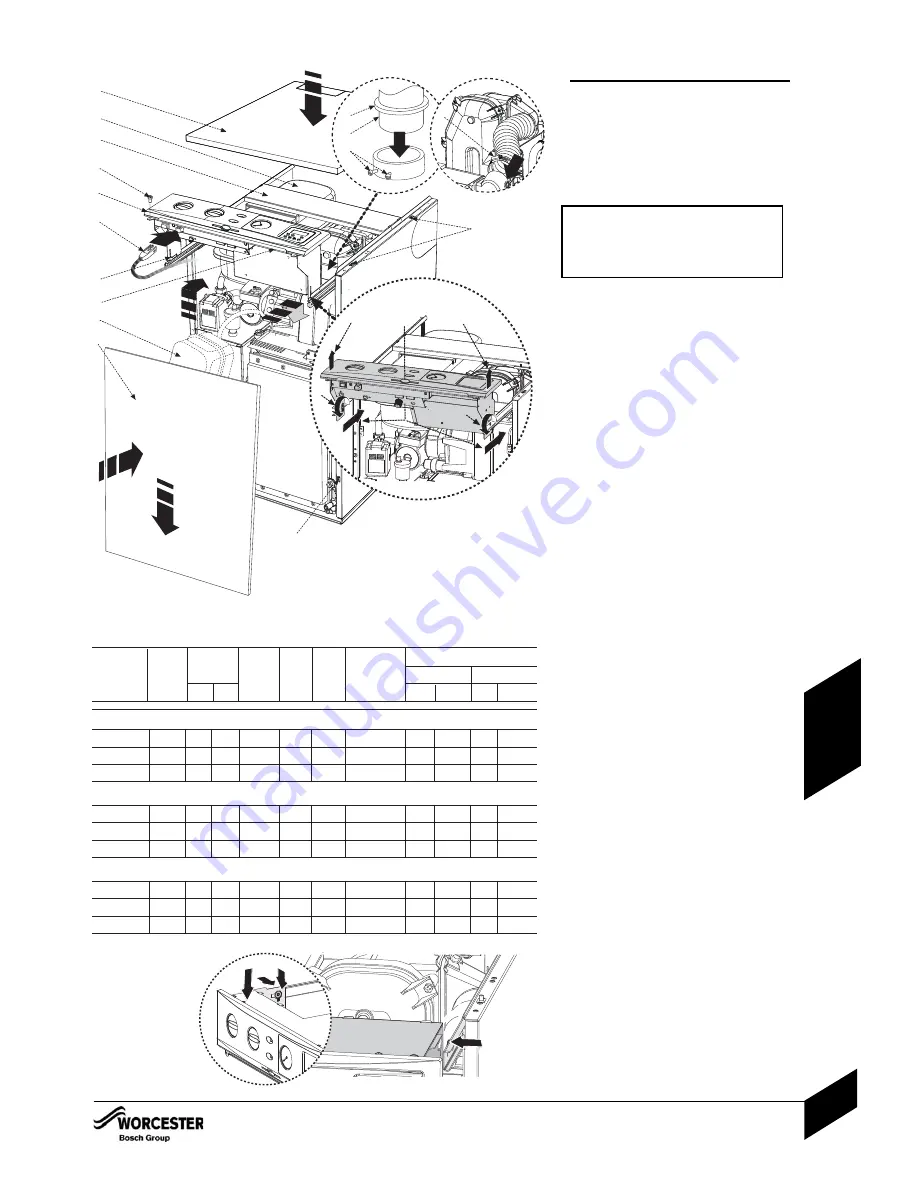
INSPECTION AND SERVICE
INSPECTION AND SERVICE
INSTALLATION & SERVICING INSTRUCTIONS FOR WORCESTER GREENSTAR HEATSLAVE 12/18-18/25-25/32
6 720 802 432 issue A 04/2012
45
SER
V
IC
IN
G
&
SP
A
RES
Re-commission the burner:
1
4
Align burner combustion head (A) into the
boiler housing tube with gasket (B)
correctly fitted.
4
Push firmly down to compress the gasket (B).
4
Tighten burner retainers (C) sufficiently to
ensure a good seal.
IMPORTANT:
Ensure the gasket is a good seal between
the burner combustion head and the boiler
housing to prevent flue gases escaping
from the combustion chamber into the room.
4
Refit flexible air duct and secure with clip (D).
2
4
Refit the expansion vessel (E) onto the
support bracket (F) and taking care not to
kink the flexible hose or snag the thermostat
capillaries.
3
4
Plug burner lead (G) into control box (H).
4
Connect an oil pressure gauge to the oil pump,
run the burner and check the oil pressure is
correct for the required boiler output. Check
that the smoke reading is between 0 and 1, if the
smoke reading is above 1 check the air setting.
If the air setting is correct check that the burner
has been reassembled correctly. Allow the
boiler to warm up then check the combustion
settings are correct as indicated in the table
below, adjust the CO
2
if necessary using the air
shutter. When the combustion is correct turn off
the boiler, remove the pressure gauge and refit
the blanking plug and plastic cover.
Refit control box:
4
4
Lift the control box upwards ( J ).
4
Rotate the box towards you (K).
4
Slide back into position (L).
4
Secure in place with screws (M).
Refit panels:
5
4
Locate top edge of panel (N) onto the top
supporting ledge (O) on the boiler.
4
Locate the ball stud connections (P) at the
base of the front panel (N) and push towards
the boiler to secure.
6
4
Locate the top panel (R) onto the ball stud
connections (S) and press down to secure.
After service handover:
4
Make a note of the date of any water treatment.
4
Set the controls back to the users requirements.
4
Complete the service interval record at the
back of this manual and a CD11 or an
equivalent form.
4
If the appliance is unused and exposed to
freezing conditions; shut off all the mains
supplies, isolate the boiler and drain the
system and boiler, including the secondary
heat exchanger.
4
Replacing control box:
NOTE:
Refitting for only after complete
removal of control box.
1
4
Locate right hand side onto pivot point’
2
4
lower left hand side.
3
4
Slightly push in left hand side and align
with pivot point.
4
4
Locate left hand side onto pivot point.
4
Push box & slider fully in and secure with
screws.
S
R
E
1
5
M
6
P
4
F
N
E
O
3
H
G
2
1
C
A
B
R
%CO
2
NOMINAL BOILER RATING AT NORMAL OPERATING TEMPERATURE
USING 28sec KEROSENE:
NOZZLE
OIL
PUMP
PRESSURE
(p.s.i.)
FUEL
FLOW RATE
Kg/h
l/h
APPROX
FLUE
GAS
TEMP.
( °C )
AIR
DAMPER
DISC
APPROX.
AIR
SETTING
APPLIANCE
INPUT
OUTPUT
kW
Btu/hr
kW
Btu/hr
12/18 - Riello RDB 1 Burner
:
0.35 80
°
SR
0.45 60
°
ES
0.50 60
°
ES
105
120
125
1. 0 4
1.29
1.55
1.32
1.63
1.96
64
67
72
12 .0
12.0
12.5
4.5
3.0
4.5
42300
52900
6 3500
12
15
18
40900
51200
61400
12.4
15.5
18.6
18/25 - Riello RDB 2.2 Burner
:
0.50 60
°
ES
0.65 60
°
ES
0.75 60
°
ES
125
120
115
1.56
1.86
2.17
1.98
2.36
2.75
75
78
84
11.5
12.0
12.5
2.0
3.0
4.5
63300
75100
8 9700
18
21.5
25
61400
73400
85300
18.6
22.2
25.8
25/32 - Riello RDB 2.2 Burner
:
0.75 60
°
ES
0.75 60
°
ES
0.85 60
°
ES
105
140
150
2.15
2.45
2.75
2.72
3.10
3.48
78
80
83
11.5
12.0
12.5
3.0
4.0
5.0
87040
99200
111400
25
28.5
32
85300
97200
109200
25.5
29.1
32.7
15-18kW
15-18kW
12kW
18-25kW
18-25kW
18-25kW
N/A
N/A
N/A
D
N
L
K
J
J
K
3
4
2
1