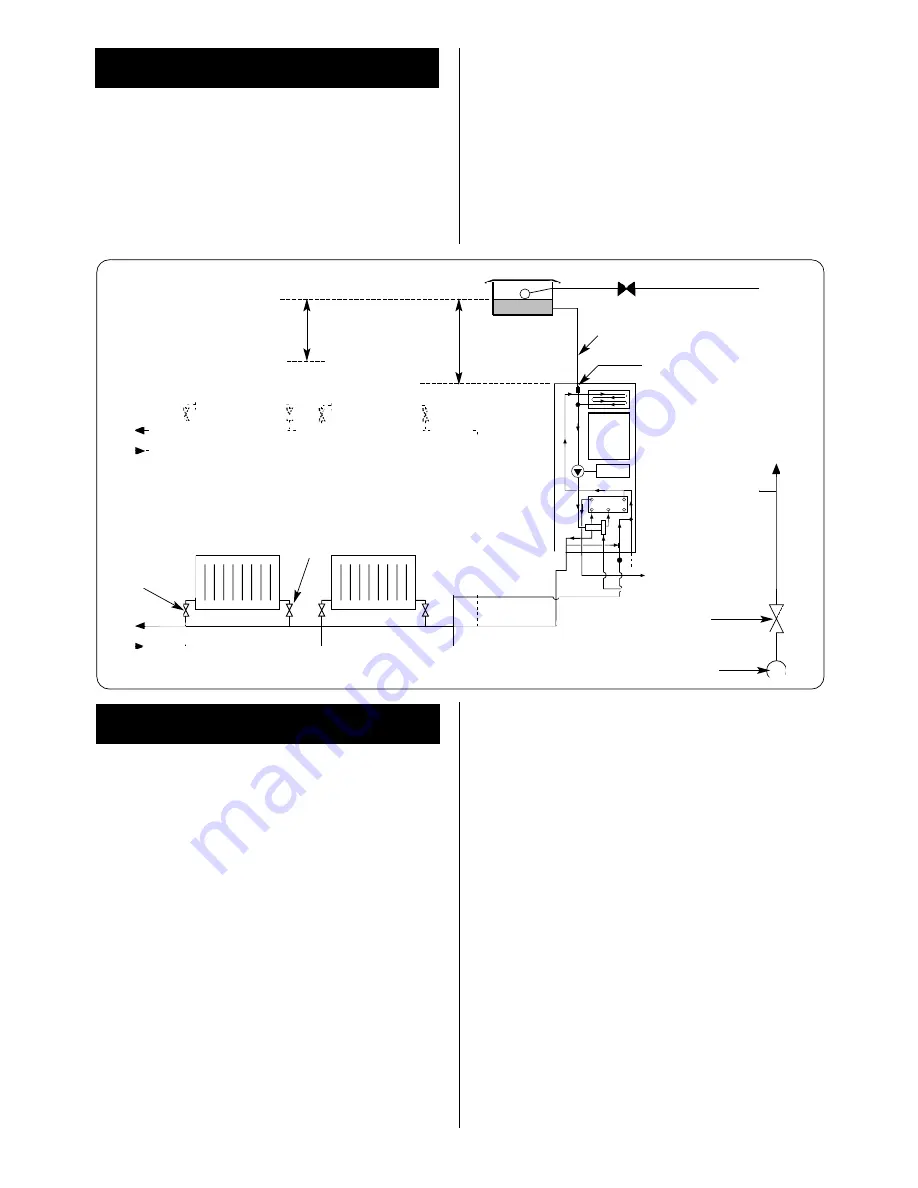
9.1
The size of the flow and return pipework is given in Section 3
– Table 4. The components required to connect the appliance to
an open vent system are available as an optional extra kit.
9.2
The feed and expansion cistern should be arranged so that
there is a minimum static head of 0.3 metres (12 inches) above
the top of the appliance or above the highest point in the heating
circuit, whichever is the higher. See Fig. 7
9.3
The feed and vent pipe should be 22mm diameter and rise
continuously from the appliance to the feed and expansion
cistern.
9.4
A pressure relief valve is not required on an open vented
system.
9.5
Air within the appliance will be expelled via the feed and
vent connection or dissipated into the rest of the system which
must be fitted with manual air vents at any high point.
9.6
The pump is set to maximum and must not be reset.
9.7
If it is required to use the appliance for domestic hot water
before the central heating circuit is connected, a 22mm copper
by-pass must be connected between the central heating flow
and return. Refer to Section 12 and Fig. 7.
N.B: 35CDi
II
IS NOT SUITABLE FOR OPEN VENT SYSTEMS.
9. Open V
ent Primary Systems
9
10.1
The following are general requirements and, if necessary,
reference should be made to the local Water Company before
fitting the appliance.
10.2 MAINS COLD WATER INLET
. Devices capable of preventing
the flow of expansion water must not be fitted unless separate
arrangements have been made. An expansion vessel connection
point is provided within the appliance. An Rc1/8” connection is
provided. A mini expansion vessel kit is available from Worcester
Heat Systems Ltd. A thread sealant compatible with potable
water must be used. Refer to Section 2.9.
10.3
The final 600mm of the mains cold water connection to the
appliance should be made in copper tube only.
10.4
The appliance is suitable for a mains pressure of up to 10
bar.
10.5
The appliance is fitted with a mains supply isolating valve.
10.6
The maximum domestic hot water flow rate is 9.0
litres/min (±15%) 24CDi or 10.0 litres/min (±15%) 28CDi or
12.0 litres/min (±10%) 35CDi
II.
10.7
In winter (when the mains inlet water temperature is
lower) a reduced flow rate at the taps may be required to achieve
the hot water delivery temperature available in warmer weather.
10.8
It is suggested that long pipe runs to the taps or shower
should be insulated to prevent the rapid cooling of domestic hot
water after a tap or shower has been turned off.
10.9
Hot and cold taps and mixing valves used with this
appliance must be suitable for operating at mains pressure and
temperatures of 65°C.
10.10
No anti-syphonage arrangements are necessary except
for some loose head showers. See Clause 12.
10.11
Thermostatically controlled or pressure equalising shower
valves will guard against the flow of water at too high a
temperature.
10.12
The head of a loose head shower must not fall closer than
25mm (1in) above the top edge of the bath to prevent its immersion
in bath water. Alternatively the shower must be fitted with an anti-
syphonage device at the point of the flexible hose connections.
10.13
The supply of hot and cold mains water direct to a bidet is
permitted, subject to local Water Company requirements,
provided that the bidet is of the over-rim flushing type. The
outlet(s) should be shrouded and unable to have any temporary
hand held spray attached. No anti-syphonage arrangements are
necessary.
10.14
As the maximum temperature of the Water to Water heat
exchanger is limited by the control circuit, there is normally no
need for water treatment to prevent scale accumulation. In
exceptional circumstances a device to prevent scale formation
can be fitted.
Installation of a scale inhibitor assembly should be in
accordance with the requirements of the local Water Company.
An isolating valve should be fitted to allow servicing. The water
hardness can be determined using a standard test paper or by
reference to the local Water Company.
10. Do
mestic Hot Water
Fig. 7. Open vent water system.
Lockshield
valve
Radiator
valve
S.H.
S.H.
Heating
return
Hot water out
Stop valve
Water main
British Standard
stop valve.
Fixed spindle type
Combined feed and
vent pipe (22mm),
must rise continuously
Static Head (S.H.): Minimum static head
0.3m (12ins) measured from the top
surface of the appliance or the highest
point in the heating system to the water
level in the feed and expansion tank.
Open vent pipe
(supplied as
optional extra)
Mains
cold
water
Heating
flow
NOTE: A drain cock should be installed at the lowest
point of the heating circuit and beneath the appliance.
Summary of Contents for 24CDi
Page 28: ...28 109 ...