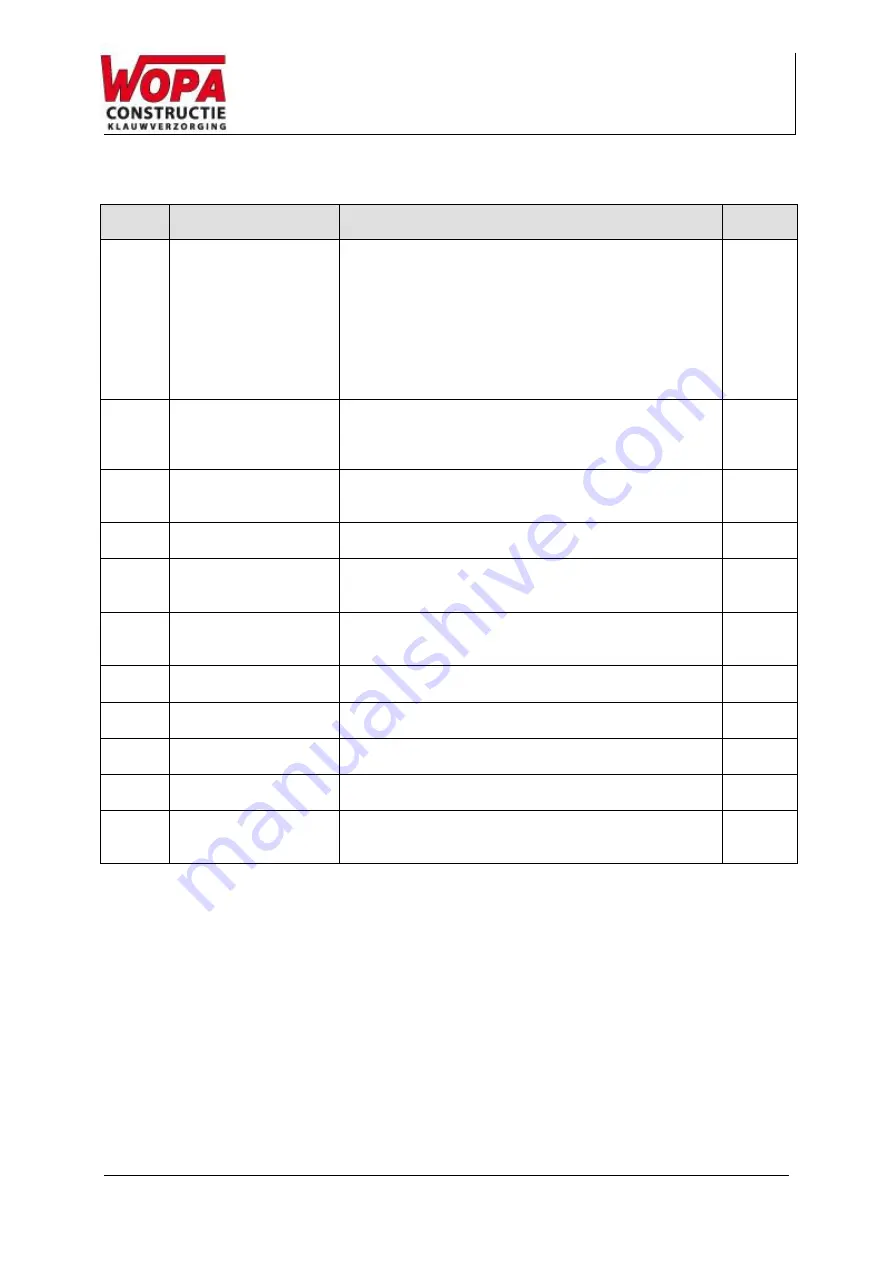
User manual
Hoof trimmingcrush:SA0051/SA0051B
Version: 21-02-17
Page 12 of 33
Main components SA0051/SA0051B:
Figure 1
Component
Description
See
Section
1
Front gate
The front gate can be set to 3 positions with the
hydraulic controls:
Entirely open: the cow can exit the crush at the
front.
Partially open: the cow can move its head
through the front gate but not its shoulders.
Stationary position.
Closed: the front gate is closed behind the
animal's head.
-
2
Front leg support
The cow’s front leg can be secured to the front
leg support by means of a hydraulic winch so
the leg can be treated.
5.4
3
Electrical connection
cable
The crush must be connected to the electricity
network for power supply for operation and the
hydraulic power unit.
4
Folding gate
The standard version includes a folding gate for
guiding the cattle.
5
Hydraulic rear gate
Once the cow is moved into the crush, the rear
gate is placed lightly against the back of the
animal.
Hind leg (hydraulic)
After the belt is attached round the hind leg, the
leg can be lifted with the hydraulic winch so the
hoof can be treated.
6
Transport set (light bar)
(SA0051)
A light bar with a license plate is attached to the
crush for transport on public roads.
Belly strap (hydraulic)
Once the cow is moved into the crush, the belly
strap is lifted hydraulically behind the front legs.
7
Transport set (axle)
(SA0051)
An axle with mudguards is attached to the
crush for transport on public roads.
8
Props
The 4 props adjust the crush to the desired
height. A lift is also possible as an option.
9
Transport set (draw bar
arm)
(SA0051)
A draw bar arm is attached to the crush for
transport on public roads