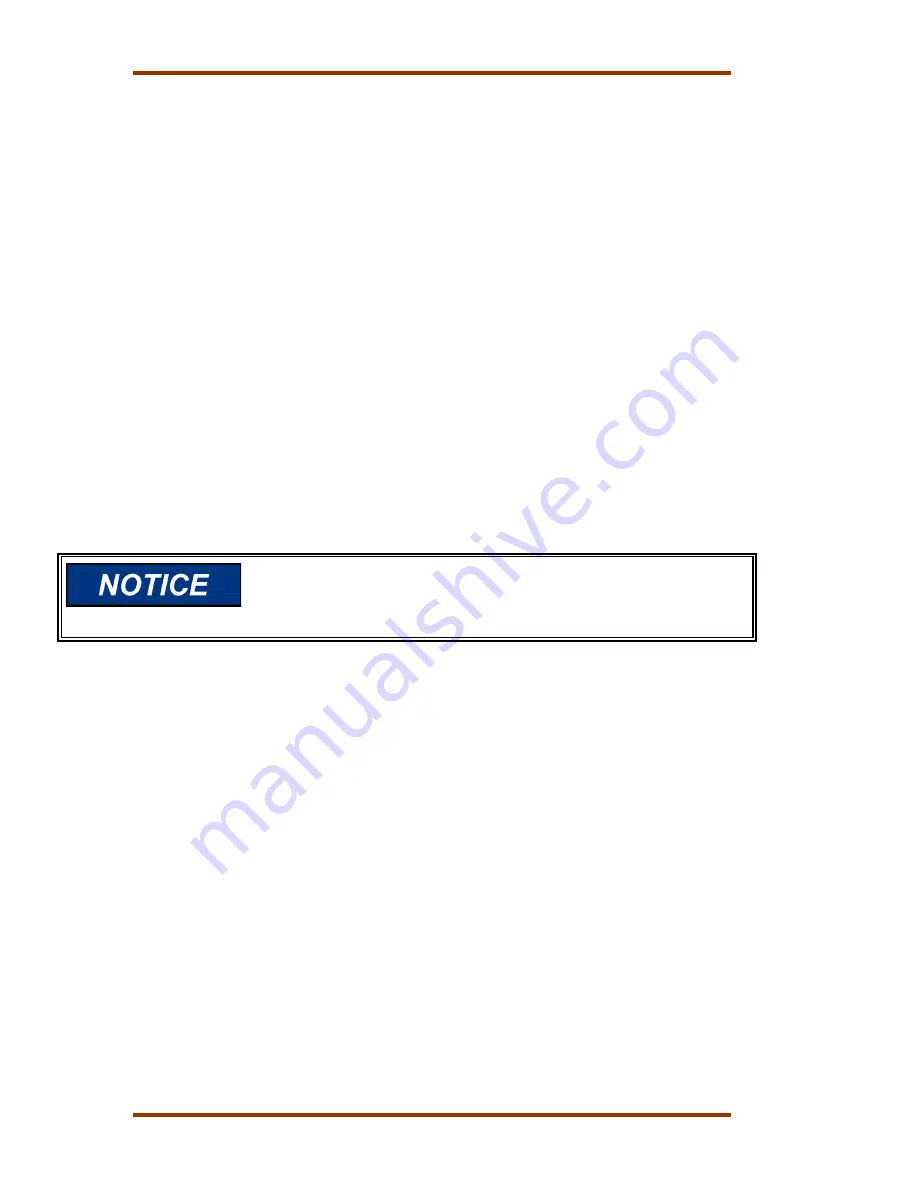
ProAct III/IV Actuator/Driver
Manual 04127
22
Woodward
Returning Equipment for Repair
If a control (or any part of an electronic control) is to be returned for repair,
please contact your Full-Service Distributor in advance to obtain Return
Authorization and shipping instructions.
When shipping the item(s), attach a tag with the following information:
•
return
number;
•
name and location where the control is installed;
•
name and phone number of contact person;
•
complete Woodward part number(s) and serial number(s);
•
description of the problem;
•
instructions describing the desired type of repair.
Packing a Control
Use the following materials when returning a complete control:
•
protective caps on any connectors;
•
antistatic protective bags on all electronic modules;
•
packing materials that will not damage the surface of the unit;
•
at least 100 mm (4 inches) of tightly packed, industry-approved packing
material;
•
a packing carton with double walls;
•
a strong tape around the outside of the carton for increased strength.
To prevent damage to electronic components caused by improper
handling, read and observe the precautions in Woodward manual
82715, Guide for Handling and Protection of Electronic Controls,
Printed Circuit Boards, and Modules.
Replacement Parts
When ordering replacement parts for controls, include the following information:
•
the part number(s) (XXXX-XXXX) that is on the enclosure nameplate;
•
the unit serial number, which is also on the nameplate.