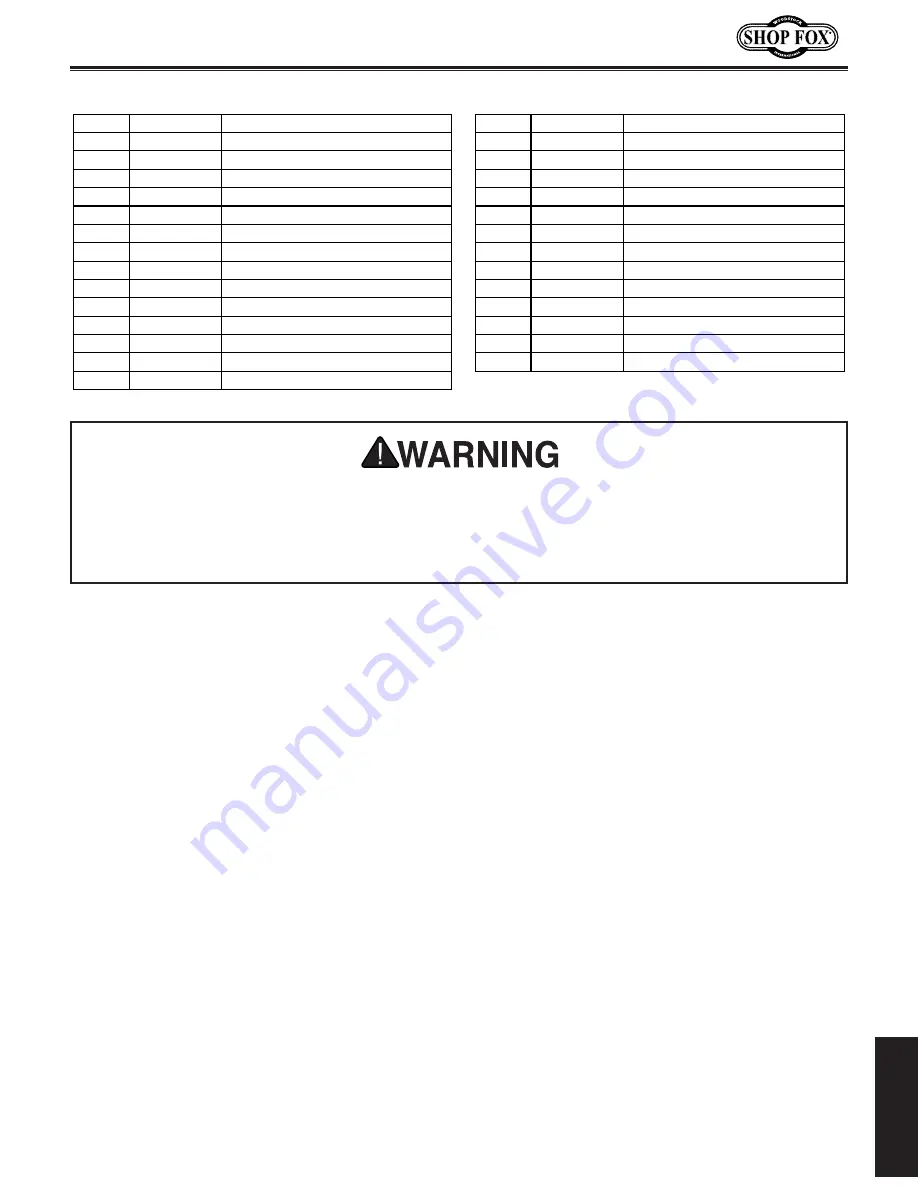
-55-
W1677/W1711 10" Table Saw
PA
RT
S
REF
PART
�
#
DESCRIPTION
REF
PART
�
#
DESCRIPTION
57
XPB15
HEX
�
BOLT
�
5/16-18
�
X
�
3/8
201
X1677201
MITER
�
GAUGE
�
BODY
57-1
XPW07
FLAT
�
WASHER
�
5/16
201-1
X1677201-1
RIVET
�
2
�
X
�
4
60
XPB07
HEX
�
BOLT
�
5/16-18
�
X
�
3/4
201-2
X1677201-2
MITER
�
GAUGE
�
SCALE
61
XPW07
FLAT
�
WASHER
�
5/16
202
X1677202
MITER
�
GAUGE
�
HANDLE
62
X1677062
BRACKET
203
X1677203
STAR
�
KNOB
�
5/16-18
�
X
�
1-1/4
72
X1677072
SHAFT
204
XPW07
FLAT
�
WASHER
�
5/16
73
X1677073
UPR
�
BLADE
�
GUARD
�
BRACKET
205
X1677205
POINTER
74
X1677074
LWR
�
BLADE
�
GUARD
�
BRACKET
206
XPFH04
FLAT
�
HD
�
SCR
�
1/4-20
�
X
�
5/8
140
XPB11
HEX
�
BOLT
�
5/16-18
�
X
�
1-1/2
207
X1677207
MITER
�
SLIDE
�
BAR
141
XPW07
FLAT
�
WASHER
�
5/16
208
X1677208
SPECIAL
�
SCREW
142
XPLW01
LOCK
�
WASHER
�
5/16
209
X1677209
SPECIAL
�
WASHER
143
XPN02
HEX
�
NUT
�
5/16-18
210
XPSS31
SET
�
SCREW
�
10-24
�
X
�
5/8
144
XPB03
HEX
�
BOLT
�
5/16-18
�
X
�
1
300
X1677300
BLADE
�
GUARD
�
ASSEMBLY
145
XPSS02
SET
�
SCREW
�
5/16-18
�
X
�
3/8
301
X1677301
BLADE
�
GUARD
�
LABEL
200
X1677200
COMPLETE
�
MITER
�
GAUGE
Safety labels warn about machine hazards and how to prevent machine damage or injury. The
owner of this machine MUST maintain the original location and readability of all labels on this
machine. If any label is removed or becomes unreadable, REPLACE that label before allowing the
machine to enter service again. Contact Woodstock International, Inc. at
(
360
)
734-3482 or www.
shopfoxtools.com to order new labels.
Summary of Contents for SHOP FOX W1677
Page 2: ......
Page 48: ...46 W1677 W1711 10 Table Saw SERVICE W1677 Wiring Diagram...
Page 49: ...47 W1677 W1711 10 Table Saw SERVICE W1711 Wiring Diagram...
Page 52: ...50 W1677 W1711 10 Table Saw PARTS PARTS Table Body Breakdown...
Page 54: ...52 W1677 W1711 10 Table Saw PARTS Motor Trunnion Breakdown...
Page 56: ...54 W1677 W1711 10 Table Saw PARTS Guard Miter Gauge Breakdown...
Page 59: ......
Page 60: ......
Page 63: ......
Page 64: ......