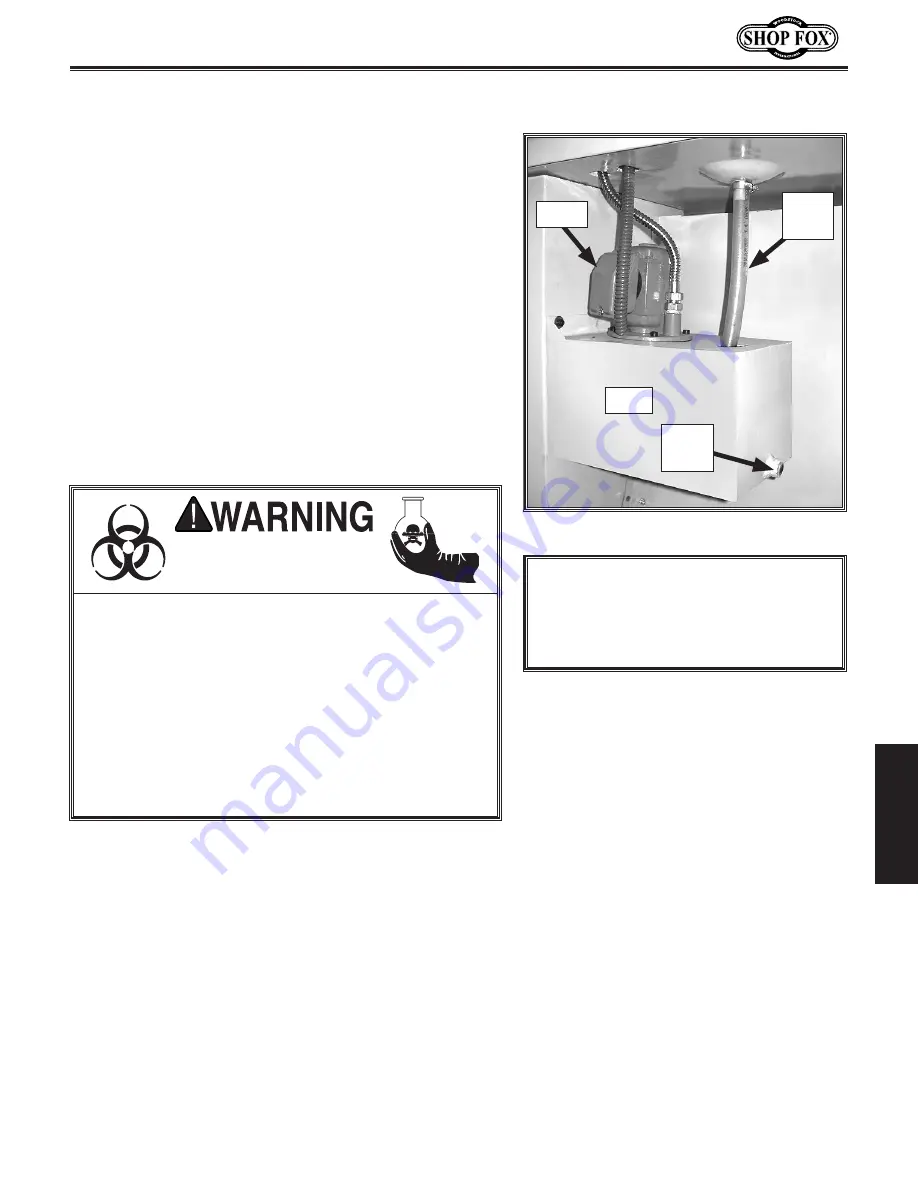
-41-
Model M1112 (For Machines Mfd. Since 12/20)
M
A
INTE
N
A
N
CE
Coolant System
To maintain the coolant system, do these steps:
1.
DISCONNECT THE LATHE FROM POWER!
2.
Remove the drain plug from the tank, drain the
coolant out, and discard properly as hazardous
waste.
3.
Pull the clear plastic drain tube from the tank and
let it hang free (
Figure
59).
4.
Using a magnet, remove metal chips from the tank.
5.
Using a rag, remove remaining material from the
tank.
6.
Refill the tank with new coolant, and insert the clear
plastic drain tube back into the tank.
Failure to follow lubrication guidelines
will lead to rapid deterioration of
lathe components.
NOTICE
Figure
59
.
Coolant pump and reservoir.
BIOLOGICAL and POISON
HAZARD!
The reservoir on this machine is designed to store
coolant. During storage coolant can grow dangerous
microbes or collect toxic heavy metals, making the
coolant a biological and poison hazard.
To prevent infections and poisoning, use the correct
personal protection equipment when handling cool-
ant and change it often.
To properly dispose of toxic coolant, follow federal,
state, and fluid manufacturer procedures.
Drain
Tube
Drain
Plug
Pump
Tank