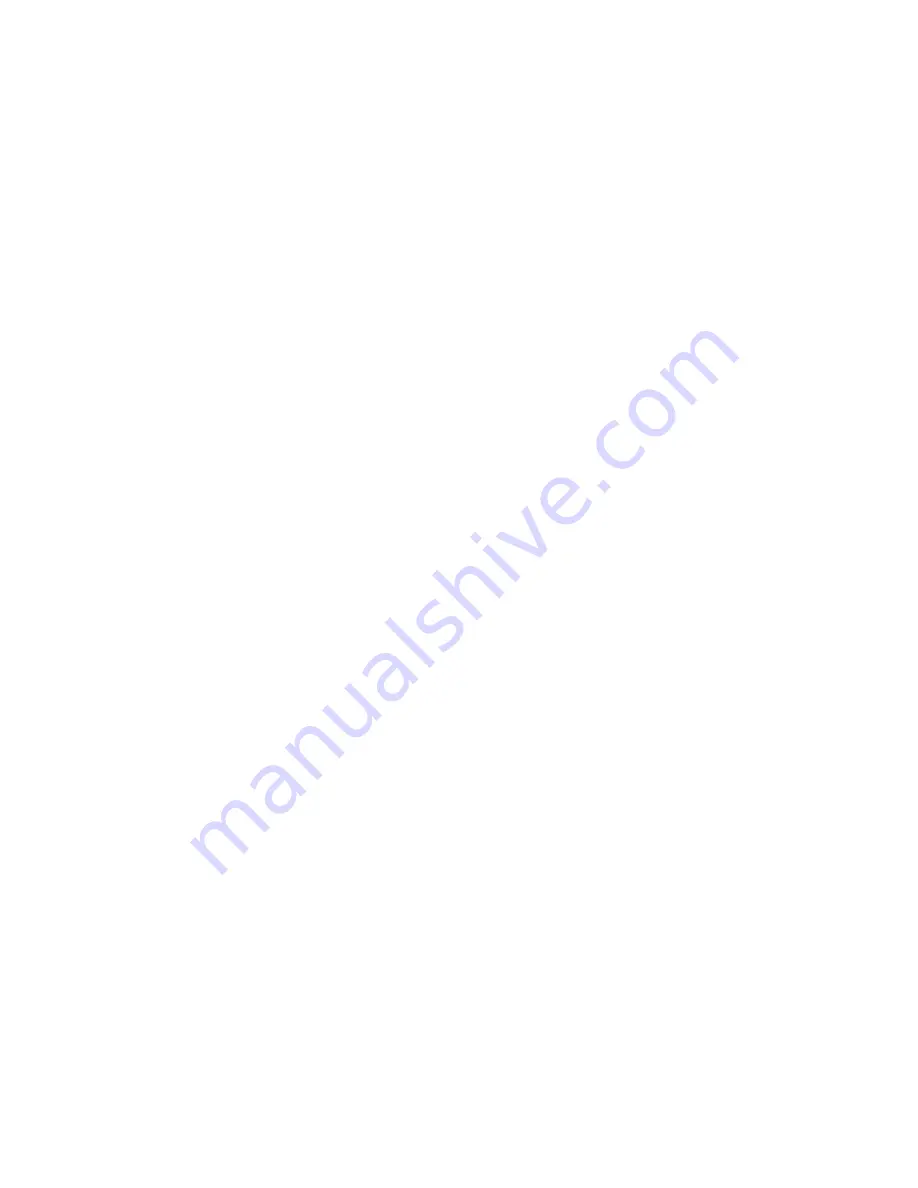
Rev 11.3/1-17
37
MRTALPR4-DC: #35057
Stock No.
Description
Qty.
15920
Vacuum Gauge - 1/8 NPT - CBM Type - w/Panel Mount Bracket
2
15792AM
Rotation or Tilt Release Lever Knob
2
15632
Pad Filter Screen - Small (for VPFS10T pads)
4
15630
Pad Filter Screen - Large (for VPFS625 pads)
4
15310AM
Pad Fitting - Push-In Swivel Elbow - 1/4 Male-NPT to 3/8" OD Hose Size (for VPFS625 pads)
4
13530
Cotterless Hitch Pin - 1/2" x 3 1/2" [13 mm x 89 mm]
6
11726AM
Clamp Collar - 2.157-18 Thread - 1-Piece
1
10906PM
Shoulder Bolt - Socket Head - 3/8" x 1" x 5/16-18 Thread (for mounting VPFS625 pads)
16
10900
Shoulder Bolt - Socket Head - 5/16" x 1/2" x 1/4-20 Thread (for mounting VPFS10T pads)
24
SERVICE ONLY WITH IDENTICAL REPLACEMENT PARTS,
AVAILABLE AT WPG.COM OR THROUGH AN AUTHORIZED WPG DEALER