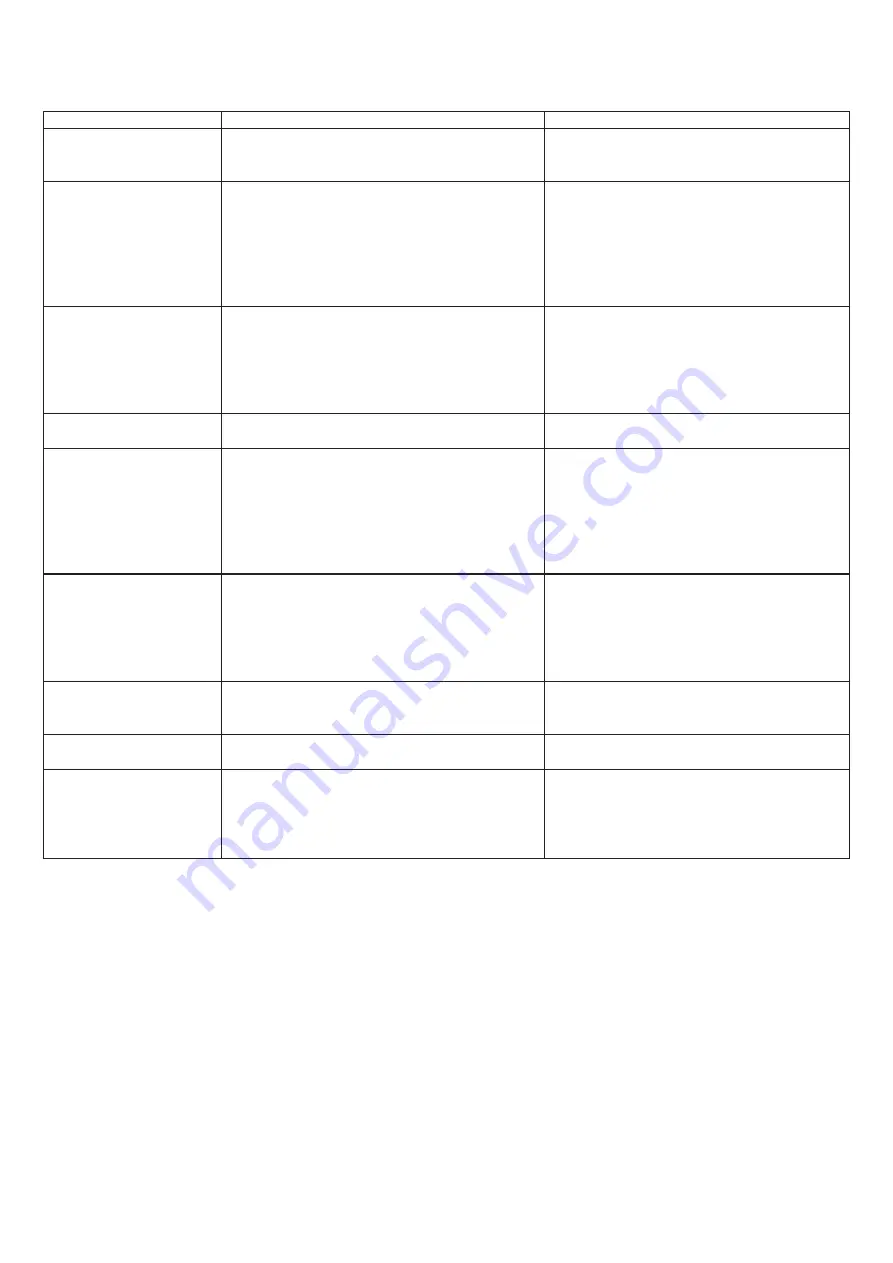
-14-
7. TROUBLESHOOTING
PROBLEM
PROBABLE CAUSE
REMEDY
Motor will not start
1.
Machine is not plugged in
2.
Low voltage
3.
Loose connection
1.
Plug in machine
2.
Check fuses
3.
Check plug and all connections
Motor fails to develop full
power.
1.
Power line is overloaded
2.
Undersize wires in supply system
3.
Drive belt tension is too high
4.
Low voltage
5.
Worn motor
1.
Correct the overload condition
2.
Increase supply wire size or elimi-
nate extension cord if one is used
3.
Adjust belt tension
4.
Have voltage checked by an elec-
trician and corrected, if necessary
5.
Replace the motor
Motor or Spindle Stalls or
will not start
1.
Excessive depth of cut
2.
Loose or broken belt
3.
Worn spindle bearings
4.
Improper cooling of motor
5.
Worn motor
1.
Reduce cutting depth
2.
Check tension or replace drive belt
3.
Replace bearings
4.
Clean motor to increase air flow, or
reduce motor running time
5.
Replace Motor
Motor overheats
1.
Motor is overloaded
2.
Air flow restricted on the motor
1.
Reduce load on the motor
2.
Clean motor to increase air flow
Excessive Vibration.
1.
Work piece is warped, out of round,
has major flaw, or was improperly prepared or
centered for turning
2.
Worn spindle bearings
3.
Worn belt
4.
Motor mount bolt or handles are loose
5.
Lathe is on an uneven surface
1.
Correct problem by planing, band
sawing, or discard the work piece
2.
Replace the bearings
3.
Replace the belt
4.
Tighten all bolts or handles
5.
Shim the lathe stand, or adjust the
feet on the stand for stability
Tailstock Moves when
applyin pressure
1.
Excessive pressure being applied by
the tailstock onto the work piece
2.
Tailstock is not secured in place
3.
Lathe bed and tailstock mating
surfaces are greasy or oily.
1.
Apply only sufficient force with the
tailstock to hold the work piece securely
between centers.
2.
Tighten tailstock locking lever
3.
Remove tailstock and clean bed
surfaces with a cleaner degreaser
Tailstock or Tool Rest
Base do not lock in place
Incorrect adjustment on locking lever
mechanism
Adjust the nut under the clamping plate
to increase (or decrease) the clamping
pressure of the lock levers
Machine bogs down
during cutting
1.
Excessive depth of cut is taken
2.
Turning tools are dull
1.
Decrease the depth of cut
2.
Sharpen the turning tools
Tools tend to grab or dig
in.
1.
Dull turning tools
2.
Tool rest is set too low
3.
Tool rest is set too far from the work
piece
4.
Improper turning tool is being used
1.
Sharpen the tools
2.
Reposition the tool rest height
3.
Set the tool rest closer to the work
piece
4.
Use the correct tool for operation