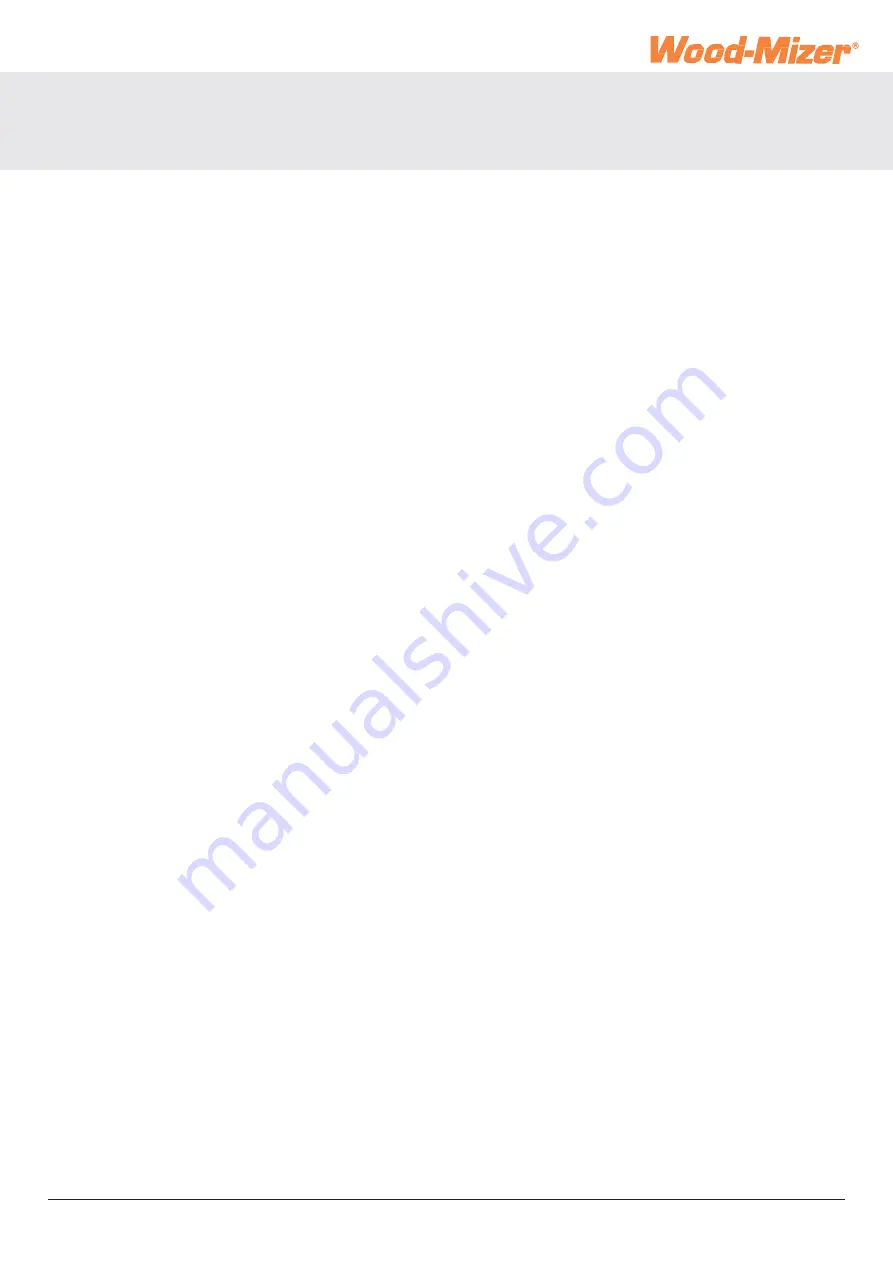
GENERAL SAFETY RULES FOR
WOODWORKING MACHINERY
3
20. Never leave the machine running unattended. Turn the power off. Do
not leave the machine until it comes to a complete stop.
21. Do not use the machine while under the effects of drugs, alcohol, or
any medication.
22. Always wear a face or dust mask if machinery operation produces a lot
of saw dust and or wood chips. Always operate the machine in a well-
ventilated area and provide for proper dust removal. Use a wood dust
collection system whenever possible.
23.
The HR250 Resaw is intended for sawing wood only. The machine must
not be used for other purposes such as cutting ice, metal or any other
materials.
24.
The blade is very sharp. Always wear safety gloves when handling the
blade.
25.
Never clean the blade or blade wheels with a brush or a scraper during
sawmill operation.
26.
Always wear ear protection when operating this machine.