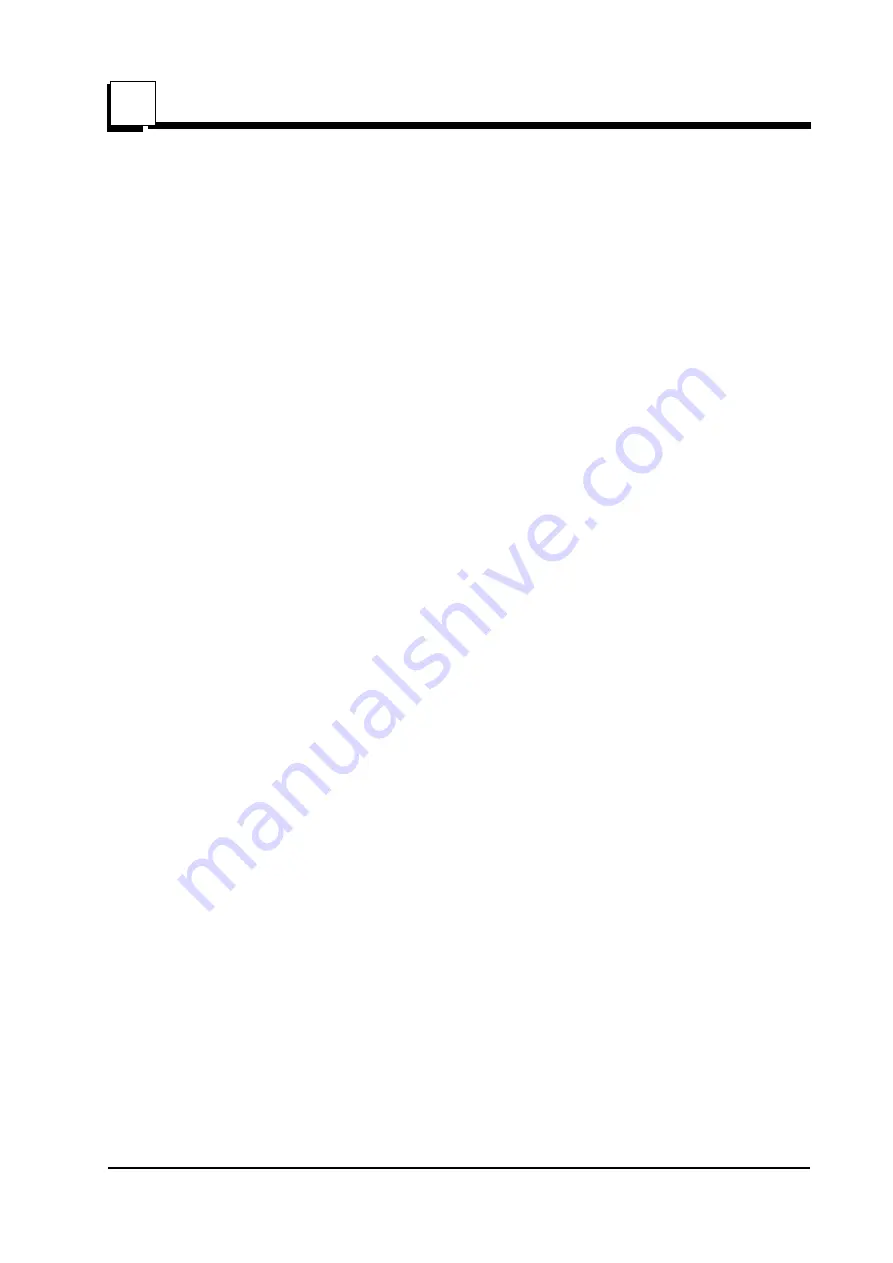
Service and repairs
11
11-1
15doc030910
Service and repairs
SECTION 11 SERVICE AND REPAIRS
1) All repairs within the warranty time period can only be performed by the authorized service
team of
Wood-Mizer Ind.
– violation of this rule may invalide the warranty.
Wood-Mizer Ind.
Customer Service
tel. +48 63 2626026