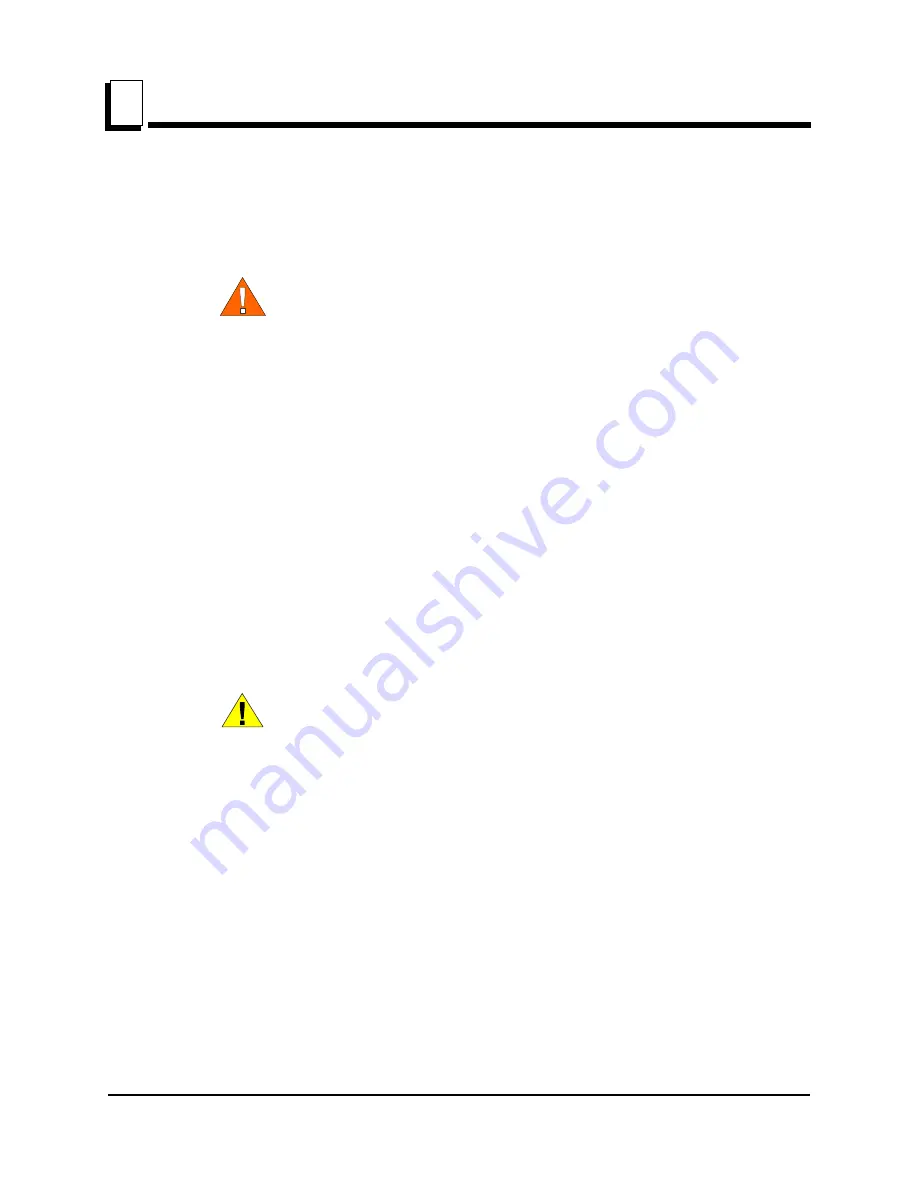
Grinding Wheel Installation
3-10
WM doc 1/20/21
3
3.4
Grinding Wheel Installation
For sharpening Wood-Mizer blades, select a 5" (12.5 cm) diameter, 1/4" (6.5 mm) wide
grinding wheel with a 1/2" (12.5 mm) bore.
WARNING!
check the grinding wheel for cracks or chips before using
it. NEVER use a cracked or chipped wheel. Doing so may result in
severe personal injury and/or machine damage.
Install a new grinding wheel:
NOTE:
The wrench built into the gauge can be used to hold the motor
arbor while installing/removing the grinding wheel
1.
Ensure that power is not connected to the sharpener and that all of the switches are in the
“off” position to avoid starting the motors when power is applied.
2.
While supporting the motor:
a.
Remove the wing nut that attaches the top rod end to the motor mount.
b.
Slide the turnbuckle assembly off the head.
c.
Rotate the sharpener head back so that it rests in the most upright position.
CAUTION!
When disconnecting or reattaching the sharpener head, be
sure to keep it supported. Do not allow the sharpener to fall. It may
damage the grinding wheel or the blade, and may cause personal
injury.
3.
Remove the wing nuts on the top and side of the cover.
4.
Remove the cover.
5.
Remove the jam nut and washer from the motor shaft.
6.
Slide a grinding wheel onto the shaft.
7.
Replace the washer.
8.
Replace the jam nut with the machined, or grooved, side toward the grinding wheel.
9.
Replace the cover.