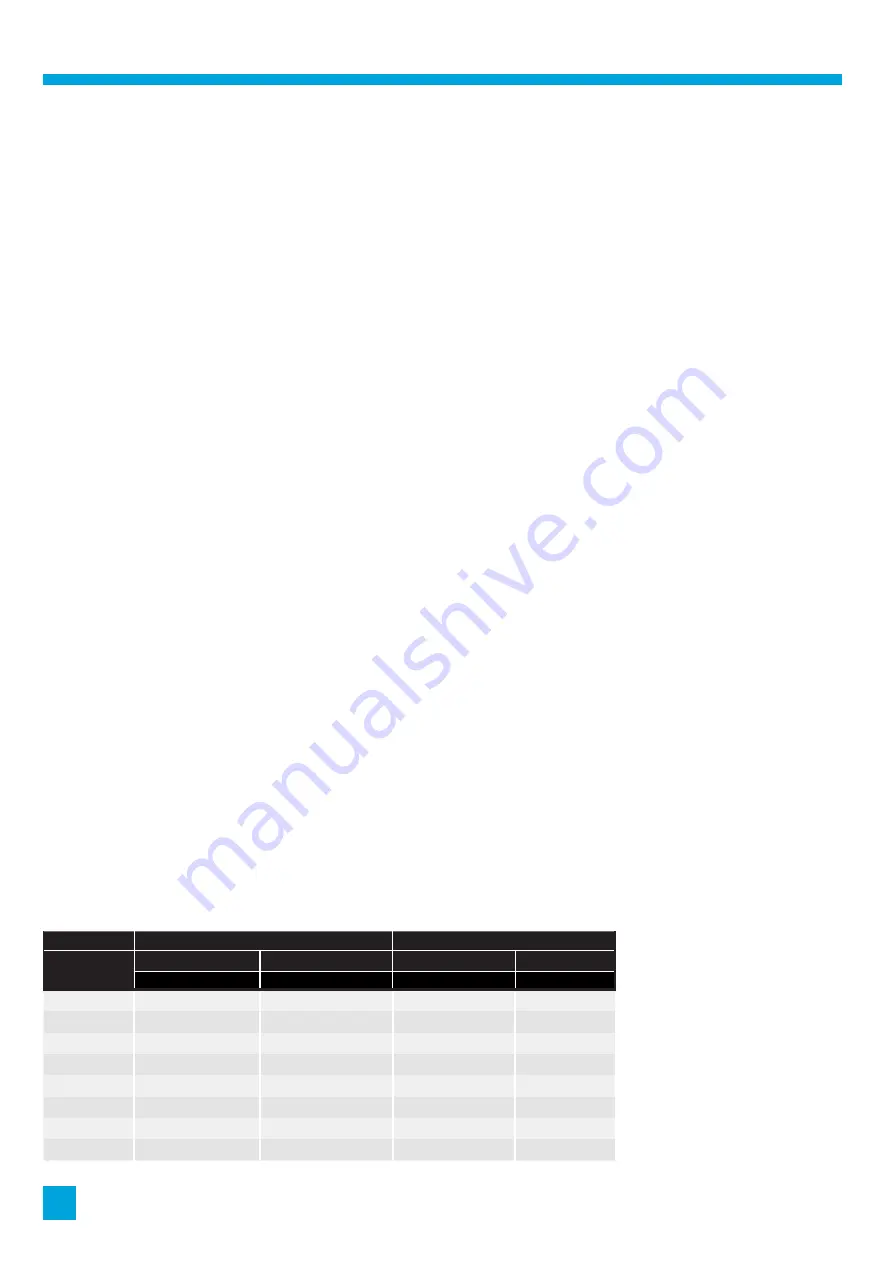
Cooling
24
20. Standards applied to the product range
Pressure equipment directive (PED) 2014/68/EU & Pressure Equipment
(Safety) Regulations 2016
• BS EN 14276-1:2006+A1:2011 - Pressure equipment for refrigerating systems and heat pumps. Vessels. General requirements
• Maximum System PED category assessment CAT I
Machinery directive 2006/42/EC & Supply of Machinery (Safety) Regulations 2008
• BS EN 378-2:2016 - Refrigerating systems and heat pumps. Safety and environmental requirements. Design, construction,
testing, marking and documentation
• BS EN ISO 12100:2010 – Safety of machinery. Basic Concepts. General principles for design. Risk assessment and risk reduction
Low voltage directive 2014/35/EU & Electrical Equipment (Safety) Regulations 2016
• BS EN 60335-1:2012+A13:2017 Household and similar electrical appliances – Safety-Part 1: General Requirements
• BS EN 60335-2-24:2010+A2:2019 Household and similar electrical appliances-Safety-Part 2-24: Requirements for refrigerating
appliances, ice cream appliances and ice makers
• EN 60529:1991- Degrees of protection provided by enclosures (IP Code)
EMC Directive 2014/30/EU & Electromagnetic Compatibility Regulations 2016
• EN 61000-6-1:2007 - Electromagnetic compatibility (EMC). Generic standards. Immunity for residential, commercial and light-
industrial environments
• EN61000-6-3:2007 A1:2011 - Electromagnetic compatibility (EMC). Generic standards. Emission standard for residential,
commercial and light-industrial environments (inclusive of EN 55014-2:2015 performance criteria in regard to Voltage dips and
interruptions, as applicable)
Other relevant directives / standards
• BS EN 378-1:2016 - Refrigerating systems and heat pumps. Safety and environmental requirements. Basic requirements,
definitions, classification and selection criteria
• RoHS Directive 2011/65/EU
• The Restriction of the Use of Certain Hazardous Substances in Electrical and Electronic Equipment Regulations 2012
• REACH Directive 1907/2006
• WEEE Directive 2012/65/EU
21. Noise levels
All noise levels are in free field conditions, Condensing unit is at 10m, and the Evaporators 3m
BMOP
CONDENSING UNIT
SOUND PRESSURE LEVELS
AIR VOLUMES
MODEL
AIR ON 20
O
C
AIR ON 32
O
C
AIR ON 20
O
C
AIR ON 32
O
C
dB(A) @10m
dB(A) @10m
m
3
/s
m
3
/s
BMOP-130-1
34.8
39.7
0.7
0.8
BMOP-150-1
34.8
39.7
0.6
0.8
BMOP-190-1
34.8
39.7
0.5
0.7
BMOP-210-1
35.3
39.9
0.5
0.7
BMOP-250 -1/3
35.3
39.9
0.5
0.7
BMOP-320 -1/3
36.9
42.4
1.3
1.6
BMOP-350-3
36.9
42.4
1.2
1.6
BMOP-360-3
36.9
42.4
1.1
1.5
Summary of Contents for Beermaster Plus BMIE-448-69
Page 1: ...wolseley co uk climate Beermaster Plus Cooling Range Installationand maintenanceinstructions...
Page 26: ...Cooling 26 23 Sales outlines BMOP130 BMOP250...
Page 27: ...27 Cooling BMOP 320 350 360...
Page 32: ...Cooling 32 BMOP 1PH BMO PLUS 1PH Schem Rev1...
Page 33: ...33 Cooling BMOP 3PH BMO PLUS 3PH Schem Rev1...
Page 34: ...Cooling 34 BMIEP All Units...
Page 36: ...wolseley co uk climate Kelvion BMI BMO Installation and maintenance Issue 1 0 2021...