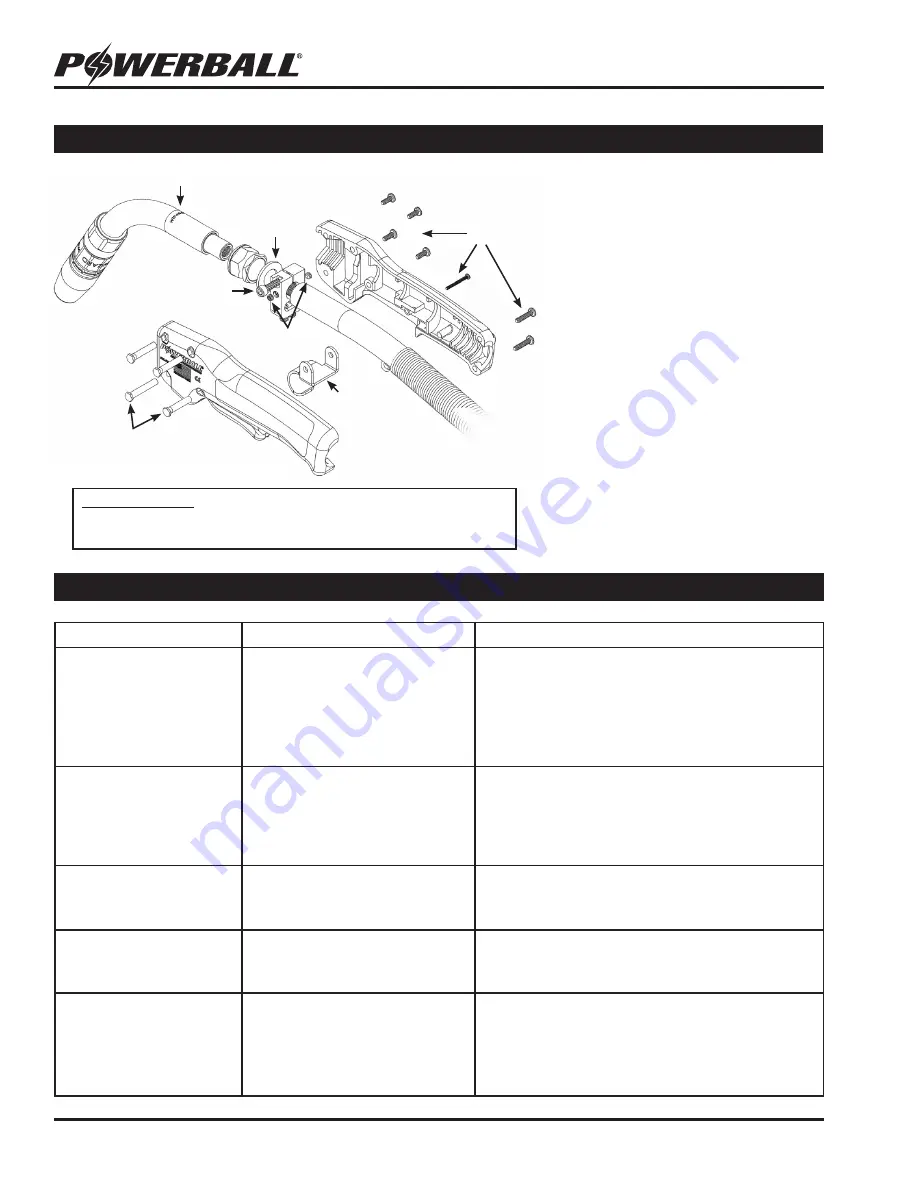
8
MIG WELDING GUN OPERATION MANUAL
7.0 TROUBLESHOOTING
6.2 GOOSENECK REPLACEMENT INSTRUCTIONS
1. Ensure power supply is OFF. Remove
the 7 handle screws from the right side
of the handle. Pull the hook attachment
pin to separate the two halves of the
handle.
2. Loosen the gooseneck clamp bolt and
the two set screws.
3. Remove gooseneck by turning
counterclockwise. Keep the insulating
washer at the base of the neck.
4. Slide the insulating washer onto the
base of the new gooseneck. Install neck
assembly by turning clockwise.
5. Secure the neck in place by tightening
the clamp bolt and two set screws.
6. Re-assemble handle with the 7 screws
and 4 attachment pins.
Handle Screws
(7)
Torch Hook
Attachment Pins
(4)
Gooseneck
Gooseneck
Clamp Bolt
Set Screws
Insulating
Washer
Problem
Potential Causes
Solutions
Wire will not feed or feeds
erratically
• Poor connection to wire feeder
• Feeder drive roll problem
• Bad microswitch in trigger
• Worn torch liner
• Burn back in contact tip
• Wrong size torch liner or tip
Inspect all cables connected to wire feeder and ensure
they are secure and in good condition. Check drive rolls
for proper size and tension. Inspect torch liner for wear
and build-up, replace as needed. Replace contact tip if a
burn back has occurred. If feeder is set up properly and
wire path is clear, the microswitch on the gun trigger may
need replacing.
Burn-back at contact tip
• Improper wire feed speed
• Improper voltage for application
• Poor wire feed
• Improper wire stick-out
• Bad ground
Check welding parameters and ensure feed speed and
voltage are set properly for your welding application.
Adjust wire stick-out if necessary. Inspect cables to
ensure proper grounding. Ensure wire delivery path does
not have excess friction.
Erratic arc
• Bad contact tip
• Poor wire feed
• Build-up in liner
Inspect contact tip for wear and replace as needed.
Check liner and wire delivery path for any build-up or
wear. Replace liner or conduit as needed.
Weld porosity
• Plugged or damaged diffuser
•
Poor gas flow
• Bad nozzle/insulator
Inspect diffuser for damage or debris, replace as needed.
Check gas supply and gas lines for proper gas flow. If
nozzle is badly worn, replace as needed.
Excess spatter
• Improper welding/gas parameters
• Tip not installed properly
• Bad nozzle/insulator
• Poor anti-spatter performance
Adjust welding parameters and gas mixture so it is
optimized for your welding application. Check tip for
proper installation and torque (see section 6.0). Replace
nozzle as needed. Try a different anti-spatter - Blue
Magic® Anti-Spatter from Wire Wizard® is recommended
for best performance.
TOOLS REQUIRED:
Phillips Screwdriver
5/32” Allen Wrench
Small Crescent Wrench
3/32” Allen Wrench