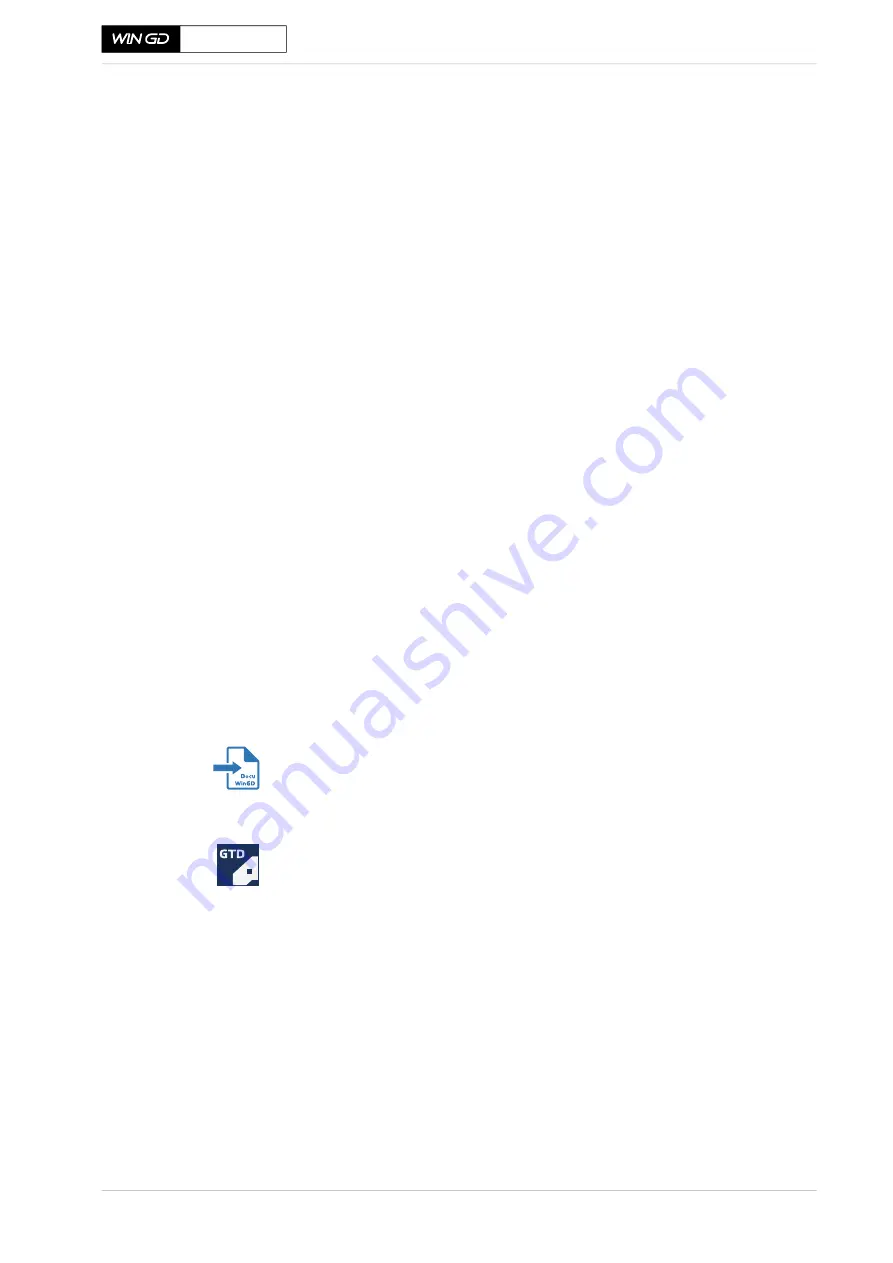
Marine Installation Manual
2022-03
4-103
4 Ancillary Systems
4.10 Exhaust gas system
X62DF-S2.0
Pressure and
control valves
The iCER exhaust gas system connects to both sides of the turbocharger and it
controls the exhaust gas recirculation flow rate with a series of valves. During
normal engine operation, the Back Pressure Valve (BPV) controls the amount of
exhaust gas that is recirculated to the engine. The Shut-Off Valve (SOV) is either
fully open or closed, depending on whether the iCER system is active or not. The
Flow Regulating Valve (FRV) can be used to support the control of the flow rate
in the iCER system, especially when operating in diesel Tier III mode.
Purge line
A purge line (inlet) valve is connected to the iCER exhaust gas system. During
the purging process, the flow direction is reversed and the position of the other
valves must be considered. The purging air is provided and controlled by the
X-DF2.0 engine.
Protection against
water droplets
The EGC has an integrated demister before its outlet. This demister removes
water droplets of a critical size carried by the exhaust gas.
After passing the EGC, the humid recirculating exhaust gas may condense on the
pipe wall and consequently, may be carrying water droplets (see section
4.3.7 The EGC circulation water system,
). For single turbocharger instal
-
lations, a water mist catcher is installed to ensure removal of these potential
water droplets. The drain arrangement is integrated into the engine. For installa
-
tions with two turbochargers, the exhaust gas return pipe must be routed below
the level of the turbochargers. This prevents water droplets in the exhaust gas
flow, or water condensate on the pipe wall, from being carried over to the turbo
-
chargers. Condensate water drains must be arranged at the lowest point of the
horizontal return manifold pipe. Different vessel trim conditions must be consid
-
ered.
As required for exhaust gas piping, the high-temperature pipes must be thermally
insulated upstream of the EGC. The pipes also require the same thermal insula
-
tion downstream of the EGC, as this will reduce condensation within the system.
For further information about system design and pressure requirements, see the
drawings relevant for the exhaust gas system (DG 9726) which are provided on
the WinGD webpage under the following link:
Exhaust gas pressure and temperature values are available from WinGD’s en
-
gine layout application
Pressure losses
The exhaust gas system design must consider many components. It is therefore
important that the shipyard coordinates with the engine builder and the ap
-
proved iCER supplier. For installations with one turbocharger, the additional
pressure drop of the water mist catcher (10 mbar) must be considered.
Pressure losses and thermal expansion must be considered across the entire iCER
system and will affect the design, selection and location of bellows within the
system.
Structural support
The piping of the exhaust gas system must be structurally supported to withstand
the mass and to minimise vibrations across the system. It is suggested that this is
achieved by supports which are connected to the ship hull or otherwise.