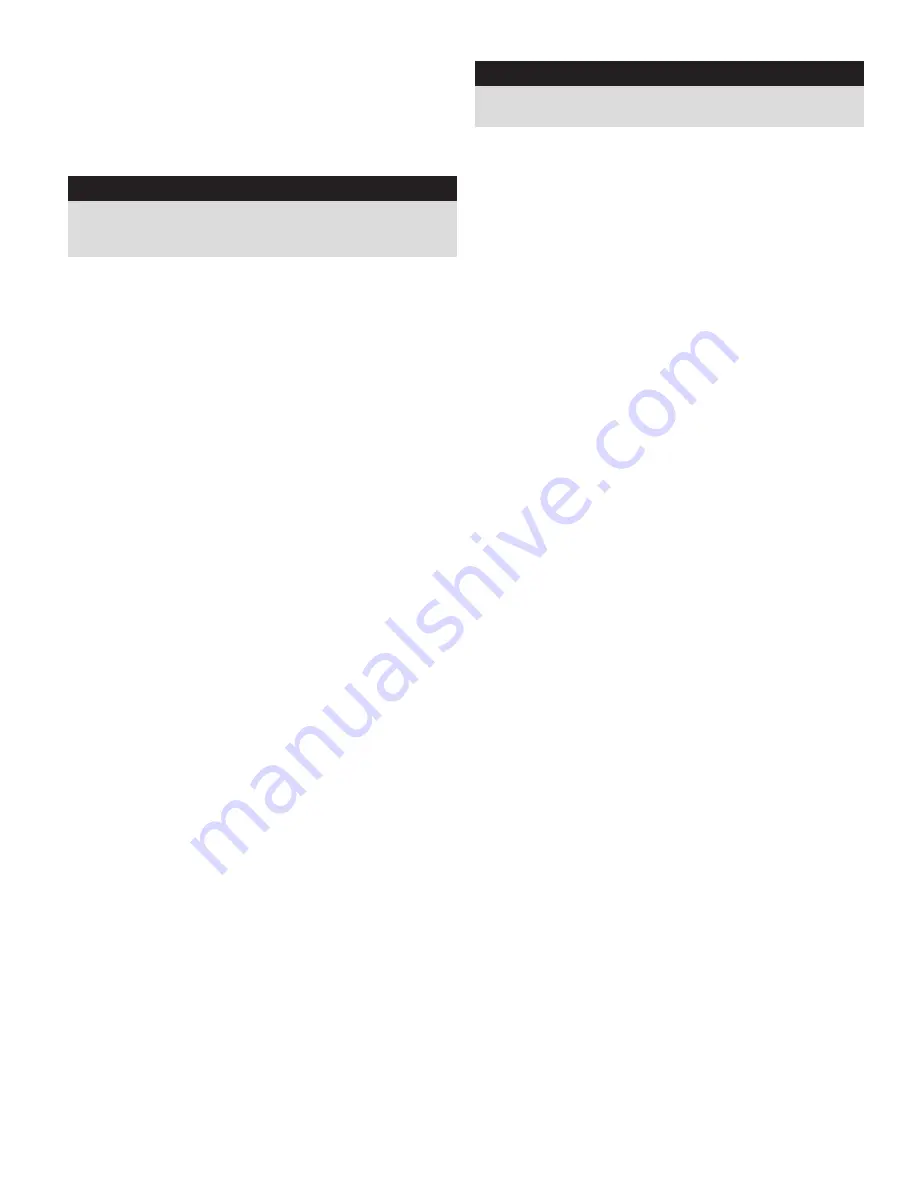
9
OPM-146/D
To connect the fuel line to the generator set you will
connect your incoming fuel line to the .75 inch NPT fitting
located on the left side of the engine-generator set. This
fitting is shipped with a plastic plug installed to insure
the fuel system stays clean. For all vapor fuel systems the
delivery pressure of the fuel to the fuel solenoid on the unit
must be four to six ounces psi (per square inch) or 7 to 11
inches W.C. (water column). These fuel pressures are critical;
failure to provide the proper pressure can cause many
problems including failure to start, inability to produce full
power, or damage to the equipment.
These generators have been tested with both natural gas
and LP at the factory. Before starting the engine you must
verify it is configured for the proper fuel. See additional
information in the NG/LP conversion section.
The information in this manual is offered to assist you in
providing the proper fuel for your engine. However, this
information is only provided to inform you of the engine’s
requirements and assist in making you aware of the
decisions you must make. In no case should the instructions
or information provided be interpreted to conflict with any
local, state, or national codes. If in doubt, always consult
your local fire marshal or fuel supplier.
INSTALLING THE FUEL LINE
NOTICE: The engine generator sets are properly adjusted
before they leave the factory. The electronic control panel
will indicate if the LP mode is active
NATURAL GAS or LP VAPOR PIPE SIZE
Size of pipe normally required for generators operating on
natural gas or LP vapor. Unit location will determine the
size of fuel line that is required to supply the engine with a
constant fuel pressure and volume.
LIQUID PROPANE VAPOR (LP)
Refer to the tables on the following pages for fuel line size
and recommended tank size. For distances of 25 feet or
over, a two regulator fuel system is recommended. This is
accomplished by installing a primary regulator at the tank
which will reduce the tank pressure down to 10 to 15 psi.
A low pressure regulator is installed to further reduce the
fuel pressure to the required six (6) oz. operating pressure.
This low pressure regulator must be at least 10 feet from
the engine generator set; any closer installation will require
a larger line be installed to provide a fuel reservoir. This is
also true for the single low pressure regulator, it should
also be a minimum of 10 feet from the unit. If this is not
done, the demand regulator on the unit and the pressure
regulator in the fuel line will interfere with each other.
When the two (2) regulator system is used on LP, a fuel line
size of 3/4 to 1 inch is generally adequate for distances up
to 300 feet from the primary to the low pressure regulator.
Consult your local fuel supplier for your exact requirements.
The appropriate line size from the following table is then
installed from the low pressure regulator to the generator
set.
WARNING: FIRE HAZARD
All fuel runs should be installed by a licensed fuel
supplier.
The WINCO installation manual OPM-112 contains
additional information on indoor, open skid installations
and is available electronically through our website or by
requesting a copy from the factory.
EXHAUST INSTALLATION
All exhaust must be piped out of the enclosure. When
selecting a location to exhaust fumes make sure that the
potential for contact with people is controlled. Exhaust can
enter buildings through windows, ventilation systems and
other openings if proper precautions are not followed.
The exhaust must be isolated from the vibration of the
engine. If the exhaust is connected in a rigid system it will
result in damage to the engine. The generator comes
equipped with an engine mounted flex pipe to aid your
installation. Ensure proper alignment with the generator.
The flex can be eliminated if it is pushed to one side to make
a connection.
The most direct path possible should be used to get to the
outside of the enclosure. Each bend restricts the pipe and
increases back pressure. It may be necessary to increase the
exhaust pipe diameter in some applications.
The exhaust pipe is very hot. When passing through the
structure it is critical that a thimble or other appropriate
technique is used to dissipate the heat and prevent the
structure from catching on fire.
It is preferable to exhaust out the side of the enclosures.
Slope the pipe slightly downward away from the engine
to cause any water in the exhaust to run away from the
engine. Do not exhaust near intake. Once outside the
enclosure a rain cap or other technique must be used to
keep water out of the exhaust. In mobile applications make
sure the rain flap faces to the rear of the vehicle so that it is
not blown open during transportation.
The generator ships with a critical grade muffler that should
be installed to decrease noise. It can be mounted either
internally or externally to the enclosure. The muffler cannot
increase back pressure to more than 0.725 psi.
FUEL INSTALLATION
The fuel supply should be as close as possible to the
engine. This will reduce the installation cost of fuel runs.
The information in this manual is offered to assist you in
providing the proper fuel for your engine. However, this
information is only provided to inform you of the engine’s
requirements and assist in making you aware of the
decisions you must make. In no case should the instructions
and information provided be interpreted to conflict with
any local, state or national codes. If in doubt, always consult
your local fire marshal, gas supplier or building inspector.
WARNING: PERSONAL INJURY
Improper exhaust installation will allow dangerous
gases to seep into enclosed spaces causing a hazard to
your health and/or death.
Summary of Contents for PSS21F4/1
Page 26: ...26 OPM 146 D Power Distribution POWER DISTRIBUTION ENGINE CONTROLS...
Page 27: ...27 OPM 146 D STARTING SYSTEM...
Page 28: ...28 OPM 146 D MSG 425 Engine Controls Ignition System IGNITION SYSTEM...
Page 29: ...29 OPM 146 D MSG 425 Engine Controls Charging System CHARGING SYSTEM...
Page 30: ...30 OPM 146 D Engine Controls Sensors 1 of 2 SENSORS...
Page 31: ...31 OPM 146 D SENSORS Engine Controls Sensors 2 of 2...
Page 32: ...32 OPM 146 D Engine Controls Actuator Data Link Connector DLC ACTUATOR DATA LINK CONNECTOR...
Page 33: ...33 OPM 146 D MSG 425 Engine Controls 08 23 Engine Controls Dry Fuel DEPR DRY FUEL DEPR...