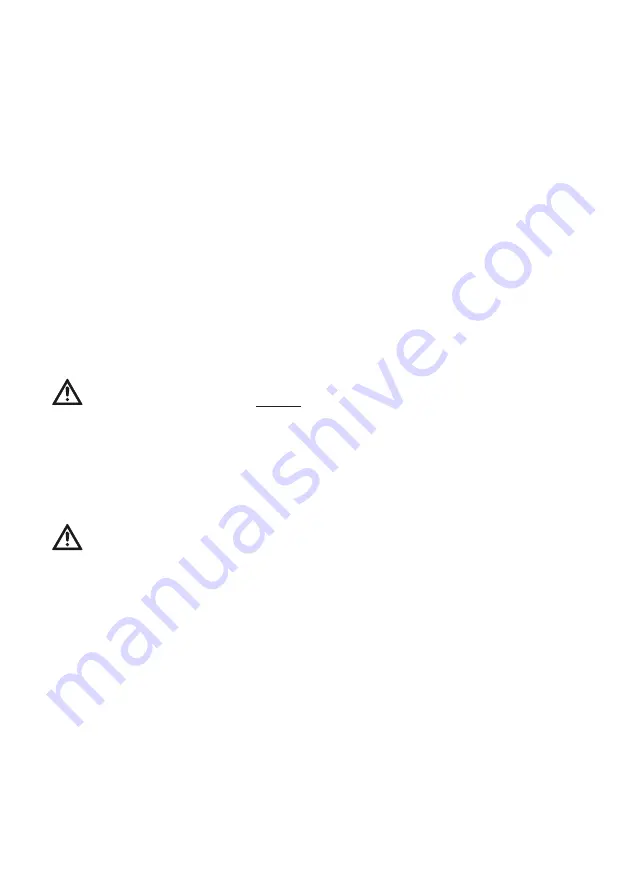
English
44
WILO SE 05/2011
7.2.3 Frequency converter operation
Three-phase motors of the series TOP-S/-SD/-D/-Z/-I can be connected to a
frequency converter. When operating with frequency converters, output filters
should be used to reduce noise and to avoid damage due to voltage spikes.
For noise reduction, it is recommended that sine filters (LC filters) are used
rather than du/dt filters (RC filters).
The following limit values should be complied with:
• Rate of voltage rise du/dt <500 V/s
• Voltage spikes û < 650 V
The following limit values at the connection terminals of the pump must not be
exceeded:
• U
min
= 150 V
• f
min
= 30 Hz,
At low output frequencies from the frequency converter, the direction of rota-
tion indicator light at the pump may go out.
8 Commissioning
WARNING! Risk of injury and material damage!
Commissioning the pump without the sealing screw including the gasket in
not permissible, since escaping fluid can cause damage!
8.1
Filling and bleeding
Prime and aerate the system as required. Aeration of the pump rotor cavity is
carried out automatically after a short operating period. Dry running for short
periods will not harm the pump.
WARNING! Risk of injury and material damage!
It is not permissible to remove the motor head for purposes of bleeding the
system!
• Touching the pump can cause burns!
Depending on the pump or system operating conditions (fluid temperature),
the entire pump can become very hot.
• There is a risk of scalding!
Escaping fluid can lead to injuries to persons and damage to the product.
When the vent screw is opened, hot fluid may escape at high pressure in
liquid of vapour form.
Pumps with vent screws (visible on the motor head; Fig. 1, item 1) can be bled
as follows if required:
• Switch off the pump
• Close the check valve on the pressure side.
• Protect electrical parts from any escaping water.
• Cautiously open the vent screw (Fig. 1, item 1) using a suitable tool.