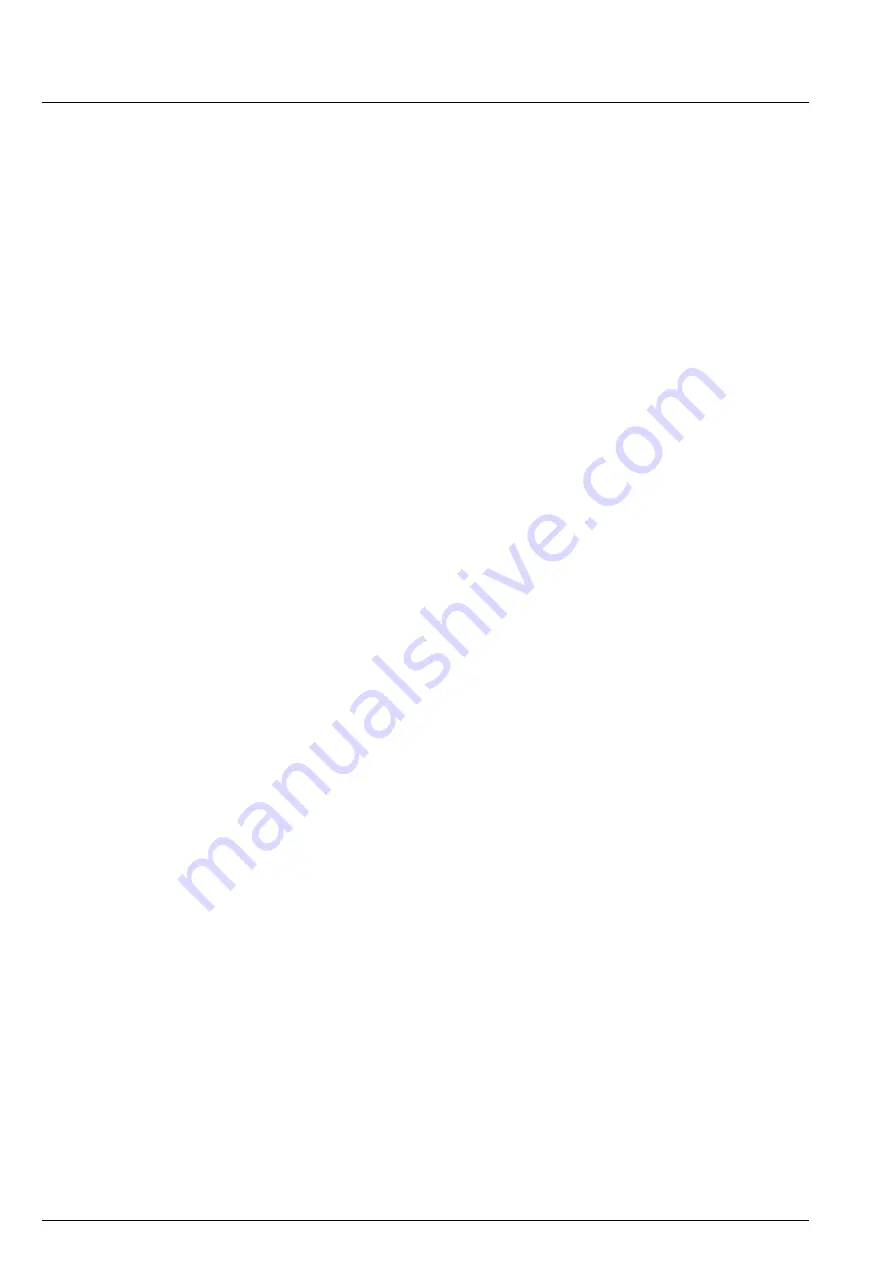
Product description
3-2
WILO EMU 3.0
Motor
The shaft and screw connections are made of stainless steel. The three-phase asynchronous motor
consists of a stator in the “H” insulation class as well as the motor shaft with rotor package. The
power supply cable is designed for the maximum mechanical load and is sealed against water pres-
sure from the pumped liquid. The motor cable lead connections are sealed from the pumped liquid
as well. The bearings used are permanently lubricated maintenance-free antifriction bearings.
The motor is surrounded by a
cooling jacket. This is filled
with a mixture of water and
glycol (P35). This means the
necessary cooling of the mo-
tor is achieved during sub-
merged and emerged
operation.
Pump
The pump housing is manufactured from different materials and, depending on the model, is sup-
plied with different connections. This means that the machine can be connected with the respec-
tive pipeline system. Some pump housings are supplied with a cleaning hole lid. This allows
blockages to be eliminated. Depending on the pump unit used, it can be equipped with a stationary
wear ring. The stationary wear ring is found in the intake port or directly in the pump housing. The
stationary and mobile wear ring determine the gap between the impeller and the intake port. If this
gap is too big, the performance of the machine decreases, and/or it can lead to blockages. For this
reason, the rings can be changed. As a result, wear and expenses for spare parts are minimized.
For machines with a screw impeller, the gap between the impeller and the intake port is set with
spacers.
Sealing
The seal between the pump and the motor consists of two mechanical shaft seals in a stainless
steel block seal cartridge. The sliding and counter-rings of the mechanical shaft seals used are
made from silicon carbide.
Sealing housing
The sealing housing is located between the motor and pump housing and is made of gray cast iron.
The housing is equipped with a sealing and leak chamber. The sealing chamber is filled with medici-
nal white oil, this means a long-lasting lubrication of the sealing is guaranteed. The leak chamber is
normally empty and takes in the fluid which is transferred inwards by the seal.
Impellers
The impeller is fastened directly to the motor shaft and driven by it. The materials used are differ-
ent types of cast iron. If special protection against wear is required, suitable impellers can be made
of “Abrasit” hard-cast or coated with ceramic liquid. Different impellers can be used according to
application, e.g. channel, screw or vortex impeller. Closed impellers are generally equipped with a
mobile wear ring.
Safety and monitoring devices
The motor is equipped with temperature sensors. These are to protect the motor from overheating.
The leak chamber is fitted with a float switch. This switches the machine off when the water
reaches a high level in the leak chamber. In addition, the machine is equipped with an electrode for
motor chamber and terminal chamber monitoring and can additionally be equipped with a sealed
chamber electrode. Depending on the connection, a warning signal can be displayed and/or the
machine switched off if water enters the motor chamber, terminal chamber or the sealing housing.
Details of the safety and monitoring devices used and how to connect
these can be found in the “Electrical connection plan” data sheet.