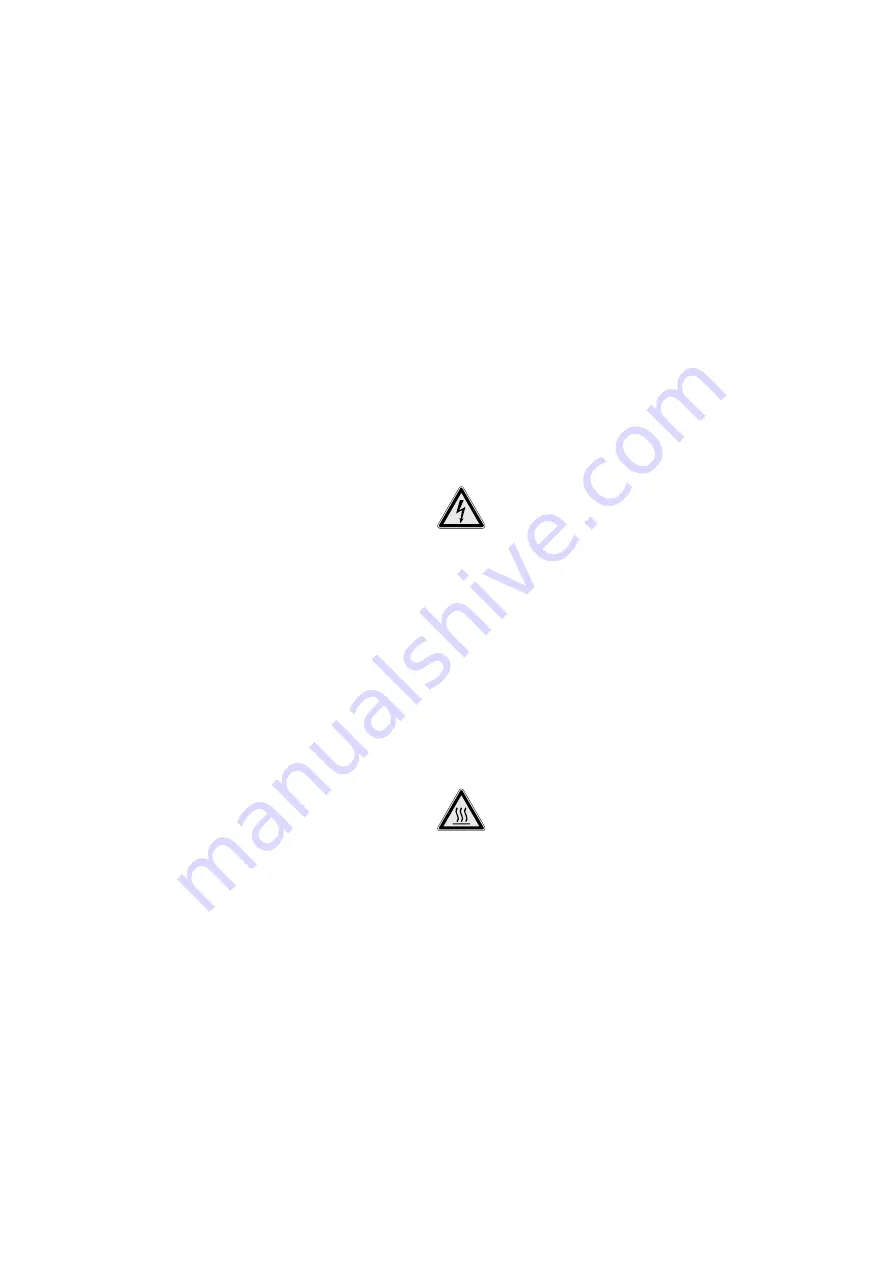
42
WILO SE 01/2014 Ed.05 DIN A4
English
COMMISSIONING
6.5.2. Initial commissioning
Before the lifting unit can be taken into operation,
it must be filled and a test run carried out. The
test run must include a complete pump cycle for
all the pumps. This allows the unit to be checked
for leaks.
In addition, the pumps' follow-up time has to be
set in order to guarantee optimum operation of
the unit.
BEWARE of malfunctions!
When the plug is inserted, the switchgear
starts in the last operating mode that was set.
Before inserting the plug, read the installation
and operating instructions for the switchgear
and ensure that you are familiar with the
switchgear's operation and displays.
Test run for proper function and leakage test
1. Switch on the lifting unit: insert the plug into the
socket.
2. Check the switchgear's current operating mode.
The switchgear should be in automatic mode.
3.
Open the check valves on the inlet and pressure
sides. The collection reservoir is filled slowly.
4.
The unit is now switched on and off using the
level control.
5. In a test run, every pump must run through a
complete pumping procedure.
6.
Close the gate valve in the inlet. In the normal
case, the lifting unit should now not switch on
again because no more fluid flows in.
If the lifting units switch on despite this, the
non-return valve is leaky. In this case, check the
position of the venting screw.
7. Check all pipe joints and the collection reservoir
do not leak.
If all the components are leak-tight and the
non-return valve closes correctly, the unit can be
used in automatic mode.
Open the gate valve in the inlet again so that
fluid can flow in.
Setting the follow-up time for the pumps
Set the pump run-time so that:
•
The largest possible quantity of sewage is
pumped in each pumping procedure.
•
The loads on the system and discharge pipeline
are as small as possible.
•
Operation is as silent as possible.
BEWARE of material damage!
Closing the non-return valve hard can result
in fluid hammers that damage or destroy the
unit and/or discharge pipeline. Avoid fluid
hammers by setting the pump run-time ap-
propriately or, if necessary, install an addi-
tional non-return valve with a counterweight.
The pump run-time should be determined as
follows:
• If a slurping noise can be heard before the pump
is switched off (pumping a water/air mixture) but
the non-return valve closes quietly or with only
a slight flap knock, the pump run-time should be
reduced so that the pump switches off shortly
before the slurping noise starts.
• If the non-return valve shuts with a loud knock
after the pump is switched off and the unit and
the pipe vibrate, the pump run-time must be
extended until the slurping operation starts.
•
The following information should be taken into
consideration when setting the pump run-time:
•
The slurping operation should not exceed 2 s.
•
The pump run-time should not exceed 12 s.
These values must not be exceeded because
otherwise the system will be operating outside
the permissible range.
The follow-up time for the pumps is set by ad
-
justing the potentiometer in the switchgear.
See the installation and operating instructions
for the fitted switchgear.
POTENTIALLY fatal danger due to electrical
voltage!
There is a risk of fatal electric shocks oc-
curring when performing work on the open
switchgear. The follow-up time must be set
by a qualified electrician.
6.5.3. Automatic mode
The lifting unit operates in automatic mode by
default and is switched on and off using the inte-
grated level control.
1. Switch on the lifting unit: insert the plug into the
socket.
2.
Check the switchgear's operating mode. The
switchgear should be in automatic mode.
3.
The unit now runs in automatic mode.
BEWARE of burns!
The motor housing can reach temperatures
well in excess of 40 °C during operation. There
is a risk of burns! Never touch the motor
housing during operation, and even when at a
standstill.
6.5.4. Manual operation
The lifting unit can also be switched on manu
-
ally for a short test run or to drain the collection
reservoir manually in an emergency.
1. Press the manual mode button on the switchgear.
2.
Release the button again to exit manual opera
-
tion. The unit runs in automatic mode again.
BEWARE of overload!
The lifting unit is only approved for intermit-
tent operation (S3). Permanent operation can
overload the motor and damage it. Manual
operation is not allowed to continue for more
than 12 seconds. After that, there must be
108 seconds without operation!
Summary of Contents for RexaLift FIT L Series
Page 4: ...Fig 7 Fig 6 Fig 5 10 20 mm 1 1 1 1 1 3 2 3 3 4 4 4 5 5 1 2 3 4 1 2 1 2...
Page 5: ...Fig 8 Fig 9 1 3 2 min 25 mm...
Page 6: ......
Page 26: ......
Page 27: ......