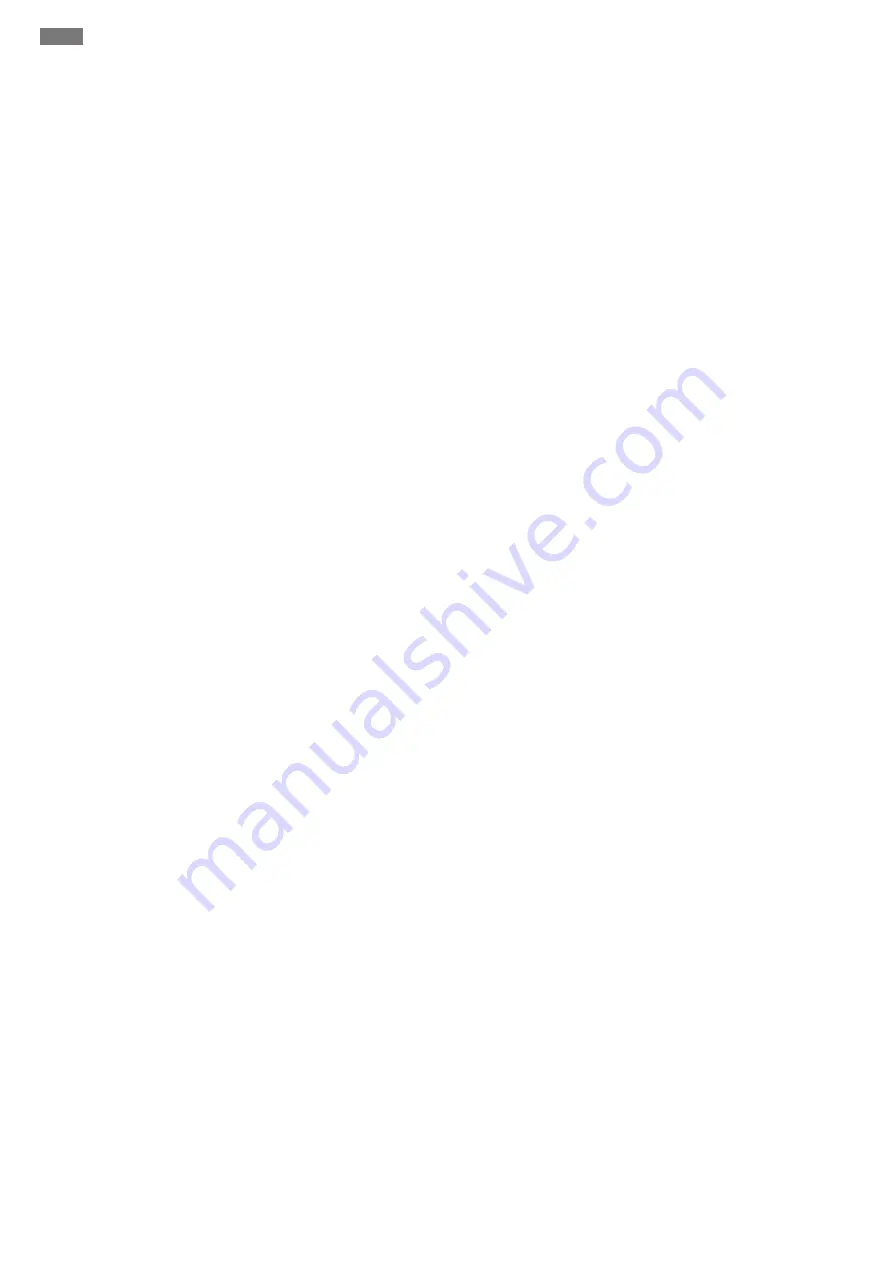
en
Spare parts
26
WILO SE 2019-02
3. Hydraulics jammed.
⇒ Clean the hydraulics.
4. Incorrect direction of rotation.
⇒ Have the connection corrected by a qualified elec-
trician.
5. Air cushion in the pipe system.
⇒ Vent the pipe system.
⇒ If air cushions occur frequently: Locate and prevent
the air intake, if required install ventilation systems
at specified locations.
6. Pump pumping against excessive pressure.
⇒ Open all gate valves on the pressure side com-
pletely.
⇒ Check the impeller shape, use other impeller shapes
if required. Contact customer service.
7. Signs of wear on the hydraulics.
⇒ Have the components (impeller, suction port, pump
housing) checked and replaced by customer ser-
vice.
8. Pipe system on the pressure side or pressure hose
clogged.
⇒ Remove clogging and replace the damaged com-
ponents if necessary.
9. Strongly gassing fluid.
⇒ Contact customer service.
10.There are only two phases at the connection.
⇒ Have the connection checked and corrected by a
qualified electrician.
11.Excessive decrease in the fill level during operation.
⇒ Check supply/capacity of the system.
⇒ Have the switching points of the level control
checked and adjusted if necessary.
Fault: The pump does not run smoothly and is noisy
1. Improper duty point.
⇒ Check the pump configuration and the duty point,
contact customer service.
2. Hydraulics jammed.
⇒ Clean the hydraulics.
3. Strongly gassing fluid.
⇒ Contact customer service.
4. There are only two phases at the connection.
⇒ Have the connection checked and corrected by a
qualified electrician.
5. Incorrect direction of rotation.
⇒ Have the connection corrected by a qualified elec-
trician.
6. Signs of wear on the hydraulics.
⇒ Have the components (impeller, suction port, pump
housing) checked and replaced by customer ser-
vice.
7. Motor bearings have worn.
⇒ Inform customer service; send the pump back to
the factory for overhauling.
8. Pump is installed under tension.
⇒ Check installation, install rubber compensators if
necessary.
Fault: Sealing chamber control reports fault or switches the
pump off
1. Condensation water build-up due to extended storage
or high temperature fluctuations.
⇒ Operate the pump for a short period (max. 5 min.)
without pencil electrode.
2. Increased leakage when running in new mechanical
seals.
⇒ Change the oil.
3. Pencil electrode cable is defective.
⇒ Replace the pencil electrode.
4. Mechanical seal is defective.
⇒ Inform customer service.
Further steps for troubleshooting
If the points listed here do not rectify the fault, contact customer
service. Customer service can assist in the following ways:
ƒ
Telephone or written support.
ƒ
On-site support.
ƒ
Inspection and repair at the factory.
Costs may be incurred if you request customer services! Please
contact customer services for more information.
11
Spare parts
Spare parts are ordered via customer service. To avoid return
queries and incorrect orders, the serial or article number must al-
ways be supplied.
Subject to change without prior notice!
12
Disposal
12.1
Oils and lubricants
Operating fluid must be collected in suitable tanks and disposed
of in accordance with the locally applicable guidelines. Wipe up
drips immediately!
12.2
Protective clothing
Used protective clothing must be disposed off in accordance with
the locally applicable guidelines.