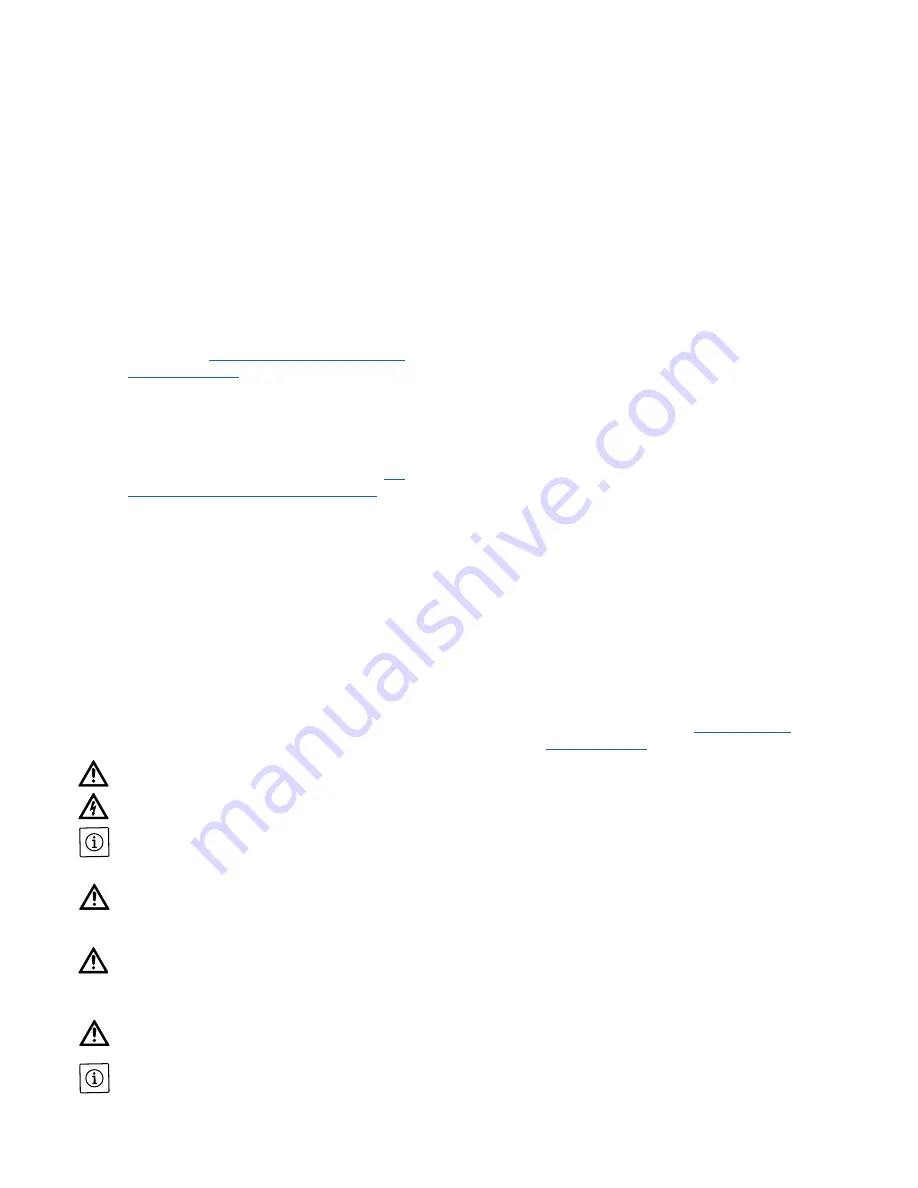
14
1. General
1.1 About this document
These installation and operating instructions are
an integral part of the product. They must be kept
readily available at the place where the product is
installed. Strict adherence to these instructions
is a precondition for the proper use and correct
operation of the product.
These installation and operating instructions
correspond to the relevant version of the product
and the underlying safety standards valid at
the time of going to print.
SPECIAL NOTE: ALL
REFERENCES TO FIGURES WILL BE ON PAGES
2-13.
1.2 Modeling information
Please refer to
, for the reference concerning
the model description.
1.3 Model nameplate information
Every MVI pump shall be shipped with a specific
nameplate for the model ordered that includes all
the information of the pump. Please refer to
1b (page 2) -Model nameplate information
2. Safety
These instructions contain important information
which must be followed when installing and
operating the pump. It is therefore imperative that
they be read by both the installer and the operator
before the pump is installed or operated.
Both the general safety instructions in this
section and the more specific safety points in the
following sections should be observed.
2.1 Instruction symbols used in this operating
manual
Symbols
General danger symbol
Hazards from electrical causes
NOTE: ...
Signals words:
DANGER! Imminently hazardous situation.
Will result in death or serious injury if not
avoided.
WARNING! Risk of serious injury. ‘Warning’
implies that failure to comply with the safety
instructions can potentially result in severe
personal injury.
CAUTION! Risk of damage to the pump if
improperly installed.
NOTE: Useful information on the handling of the
product. It alerts the user to possible problems.
2.2
Personnel qualification
The personnel installing the pump must have the
appropriate qualification for this work
.
2.3 Possible risks incurred by failure to comply with
the safety instructions
Failure to comply with the safety instructions
could result in personal injury or damage to the
pump or installation. Failure to comply with the
safety instructions could also invalidate any claim
for damages.
In particular, failure to comply with these safety
instructions could give rise, for example, to the
following risks:
• Failure of important pump or installation
functions,
• Failure of specified maintenance and repair
methods,
• Personal injury due to electrical, mechanical and
environmental causes,
• Damage to property.
2.4 Safety precautions for the operator
The relevant accident precaution regulations must
be observed. Dangers caused by electrical energy
must be excluded. Local or general regulations
[e.g. NEC,NEMA, etc.] and directives from local
codes.
2.5 Safety precautions for inspection and
installation
The operator must ensure that all inspection and
installation work is carried out by authorized and
qualified specialists who have carefully studied
these instructions.
Work on the pump/unit must be carried out only
with the pump disconnected (locked out) from
the electrical supply and at complete standstill.
For proper mounting options concering the pump
installation please refer to
2.6 Unauthorized alterations and manufacture of
spare parts
Alterations to the pump or installation may only
be made in agreement with the manufacturer.
The use of original spare parts and accessories
authorized by the manufacturer will ensure safety.
The use of any other parts may invalidate claims
revoking the liability of the manufacturer.
2.7 Improper use
The proper operation of the pump or installation
can only be guaranteed if it is used in accordance
with the operating instructions. All values must
neither exceed, nor fall below, the limit values
given in the catalogue or data sheet.
3. Transport and interim storage
When receiving the material, check that there has
been no damage during the transport. If shipping
damage has occurred, take all necessary steps
Scot Pump 02/2022