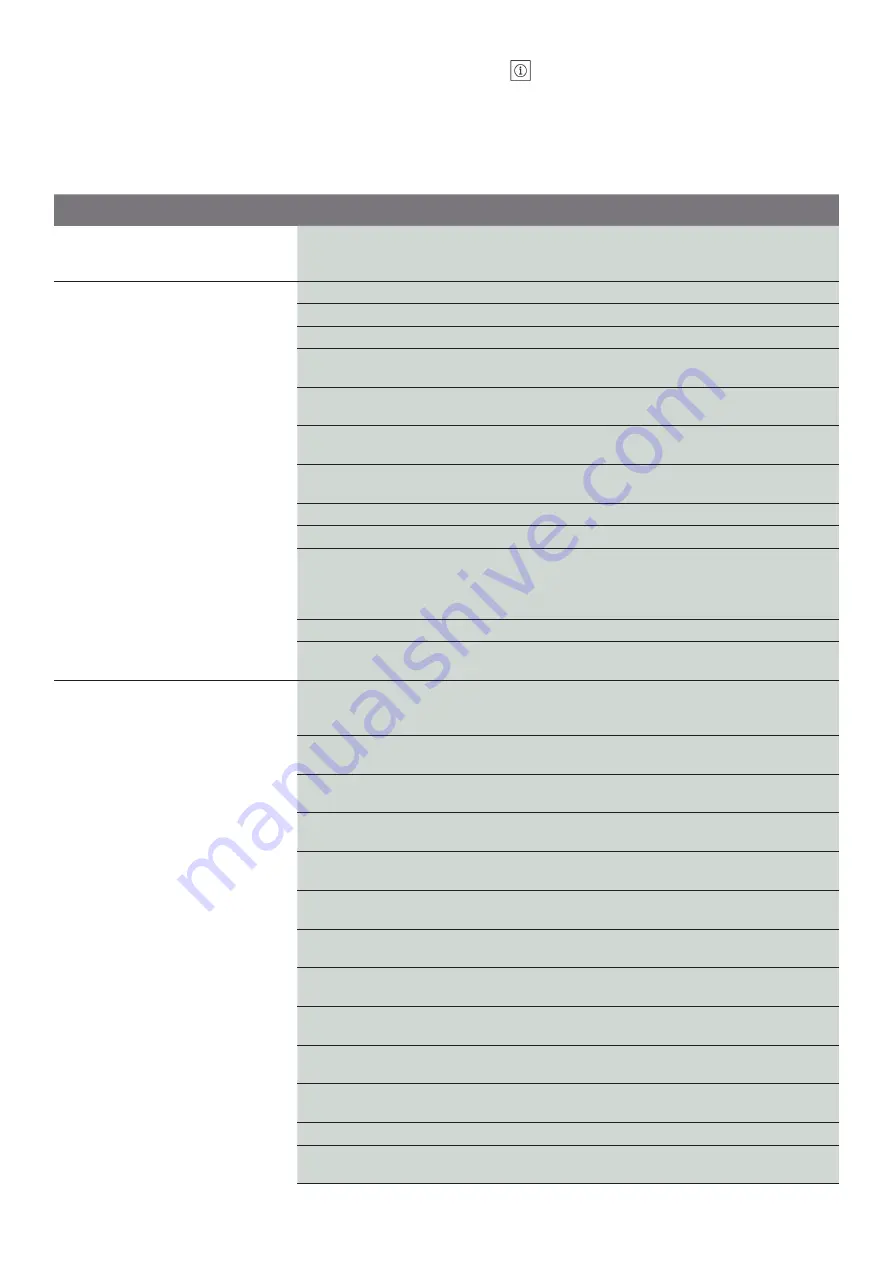
12
10 Faults, causes and remedies
Faults, particularly those affecting the pumps or
the control system, must be remedied by Wilo’s
customer service or a specialist company
NOTICE!
The general safety instructions must be observed
during any maintenance or repair work! The instal-
lation and operating instructions of the pumps and
the control device must be observed!
Fault
Cause
Remedy
Display on the control device incorrect
Make use of the information from the installa-
tion and operating instructions for
the control device
Pump(s) do(es) not start
No mains voltage
Check the fuses, cables and connections
Main switch “OFF”
Activate the main switch
Water level in break tank too low, i.e.
Check the break tank’s inlet valve / supply line
Low-water level reached
Check the inlet pressure and the level in the
break tank
Low water level indicated
Check and, if necessary, replace the low water
switch
Low water switch defective
Check installation and setting and correct as
required
Shut-off device closed at pressure sensor
Check and open the shut-off valve if neces-
sary
Start-up pressure set too high
Check the setting and correct it if necessary
Fuse defective
Check fuses and replace if necessary
Motor protection has triggered
Check the default values against the pump or
motor data, measure the current values and
correct the setting if necessary. Check the
motor for defects and replace if necessary
Contactor defective
Check it and replace it if necessary
Turn-to-turn fault in the motor
Check, if necessary replace motor or have it
repaired
Pump(s) do not switch off
Major fluctuations of the inlet pressure
Check the inlet pressure and take measures to
stabilise the inlet pressure if necessary (e.g.
pressure reducers)
Inlet pipe clogged or shut off
Check the inlet pipe and remove the clogging
or open the shut-off valve if necessary
Nominal diameter of the inlet pipe too
small
Check the inlet pipe and increase the cross
section of the inlet pipe if necessary
Inlet pipe installed incorrectly
Check the inlet pipe and change the pipe
routing if necessary
Air in the inlet
Check and shut off the piping and vent the
pumps if necessary
Impellers clogged
Check the pump and replace it or have it
repaired if necessary
Non-return valve leaking
Check and replace the seal or non-return
valve if necessary
Non-return valve clogged
Check and remove the clogging or replace the
non-return valve if necessary
Gate valve in the system closed or not
sufficiently open
Check and open the shut-off valve completely
if necessary
Flow rate too high
Check the pump data and default values and
correct if necessary
Shut-off device closed at pressure sensor
Check and open the shut-off valve if neces-
sary
Switch-off pressure set too high
Check the setting and correct it if necessary
Incorrect direction of rotation of the
motors
Check direction of rotation and correct by
changing over phases if necessary
Summary of Contents for ISAR MODH1 Series
Page 16: ...16 Fig 1 Fig 1b Fig 1c...
Page 21: ...21 NOTES...