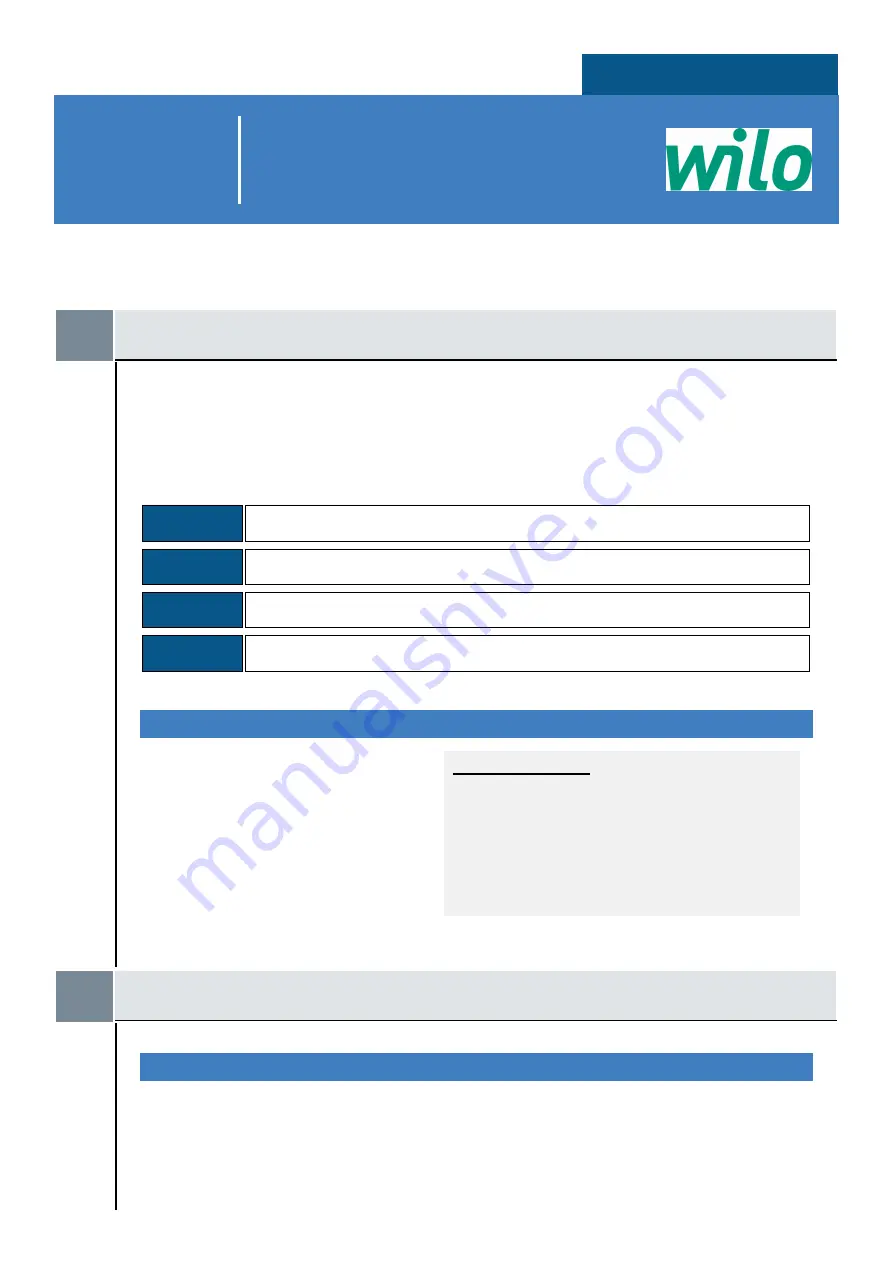
Rexa CUT GE, Rexa PRO
iBVD
Dokument Id
5560124769-00003
Version
2
Skapad
2019-02-14
Status
2019-02-14
Uppgiftslämnaren reserverar sig för eventuella fel i produktinformationen eller felaktigt registrerade uppgifter och förbehåller sig
rätten att korrigera och/eller komplettera produktinformation utan föregående avisering
1
GRUNDDATA
Varubeskrivning
Submersible Sewage Pump
Övriga upplysningar
Klassificeringar
ETIM
›
BK04
›
BSAB
›
UNSPSC
›
Leverantörsuppgifter
Företagsnamn
WILO Nordic AB
Organisationsnummer
5560124769
Adress
Isbjörnsvägen 6
Hemsida
www.wilo.se
Miljökontaktperson
Namn
Wilo kundsupport
Telefon
0470-72 76 00
E-post
[email protected]
2
HÅLLBARHETSARBETE
Företagets certifiering
ISO 9000
■
ISO 14000
■
Sida 1