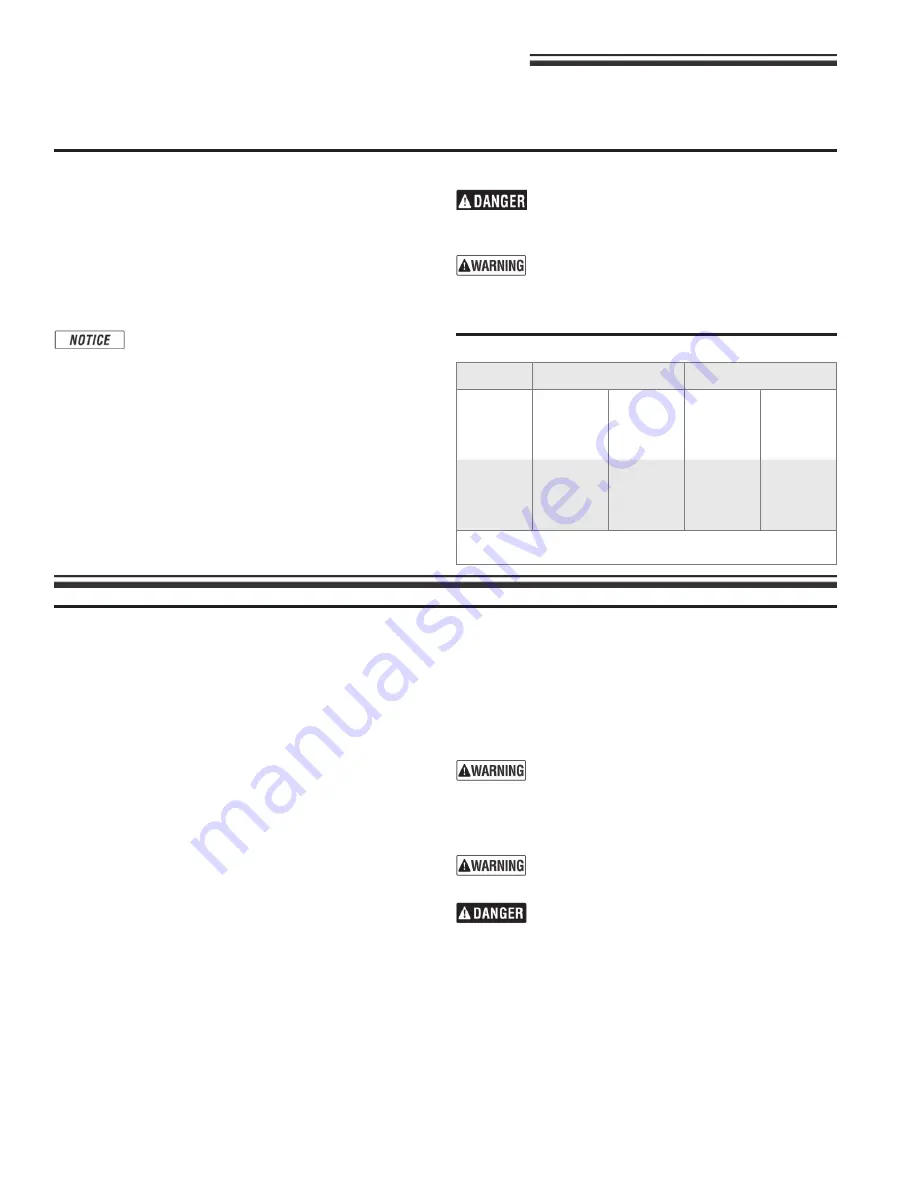
GWS-090E
Gas-Fired Water Boiler –
Boiler Manual
8
Part Number 550-110-737/1108
Perform hydrostatic pressure test
Pressure test boiler before attaching water or gas piping or elec-
trical supply (except as noted below).
Prepare boiler for test
1. Remove the shipping nipple (from GWS-090E supply tapping)
and remove the boiler relief valve. Temporarily plug the relief
valve tapping with a ¾” NPT pipe plug.
2. Remove 1¼” nipple, reducing tee and drain valve from ac-
cessory bag. Install in boiler return connection as shown on
in Figure 18, item 3, page 36. Install circulator on either the
return or supply.
3. Remove 1¼” nipple, 1¼” tee, bushing and pressure/tempera-
ture gauge from accessory bag. Pipe to boiler supply connec-
tion as shown in Figure 18, item 2, page 36. (Use pipe dope
sparingly.)
4. Connect a hose to boiler drain valve, the other end connected
to a fresh water supply. Make sure hose can also be used to
drain boiler after test.
5. Connect a nipple and shutoff valve to system supply connec-
tion on the 1¼” tee. This valve will be used to bleed air during
the fill. (Valve and nipple are not included with boiler.)
6. Connect a nipple and shutoff valve to system return connec-
tion (at circulator flange if circulator installed on return). This
valve will be used to bleed air during the fill. (Valve and nipple
are not included with boiler.)
Fill and pressure test
1. Open the shutoff valves you installed on supply and return
connections.
Pressure test
2. Slowly open boiler drain valve and fresh water supply to fill
boiler with water.
3. When water flows from shutoff valves, close boiler drain
valve.
4. Close shutoff valves.
5. Slowly reopen boiler drain valve until test pressure of not more
than 45 psi is reached on the pressure/temperature gauge.
6. Test at no more than 45 psi for no more than 10 minutes.
Do not leave boiler unattended. A cold water fill could
expand and cause excessive pressure, resulting in
severe personal injury, death or substantial property
damage.
7. Make sure constant gauge pressure has been maintained
throughout test. Check for leaks. Repair if found.
Leaks must be repaired at once. Failure to do so
can damage boiler, resulting in substantial property
damage.
Do not use petroleum-based cleaning or sealing
compounds in boiler system. Severe damage to
boiler will occur, resulting in substantial property
damage.
Drain and remove fittings
1. Disconnect fill water hose from water source.
2. Drain boiler at drain valve or out hose, whichever provides
best access to drain. Remove hose after draining if used to
drain boiler.
3. Remove nipples and valves unless they will remain for use in
the system piping.
4. Remove plug from relief valve tapping. See Section 3, page 9,
to replace relief valve.
2 Prepare boiler
Table 4
Manifold orifice sizing
Location
Natural gas
Propane gas
U. S.
Sea level –
2,000 ft
over
2,000 ft
Sea level –
2,000 ft
over
2,000 ft
2.55 mm
(Note 1)
1.60 mm
(Note 1)
Canada
Sea level –
2,000 ft
2,000 –
4,500
Sea level –
2,000 ft
2,000 –
4,500
2.55 mm
# 41
1.60 mm
1.45 mm
Note 1: For U. S. elevations above 2,000 feet, contact your local supplier for
details.
Place boiler/crate near position
1. Leave boiler in crate and on pallet until installation site is
ready.
2. Move entire crate and pallet next to selected location.
3. Remove crate. Leave boiler on pallet.
4. Remove boiler from pallet as follows:
a. Tilt left side of boiler up and place a board under left legs.
b. Tilt boiler the other way and place a board under right legs.
c. Slide boiler backwards off pallet and into position.
Do not drop boiler or bump jacket on floor or pallet.
Damage to boiler can result.
5. Check level.
a. Shim legs, if necessary.
b. Do not alter legs.
Inspect orifices and burners; connect air adapt-
er
1. Remove front jacket door. Remove air adapter fitting from air
inlet hose (see Figure 17, page 35, items 9 and 10) and screw
into opening on jacket top. Reconnect air hose to bottom of
air adapter fitting. Remove inlet air box top panel. (See Figure
16, item 13, page 34).
2. Check for correctly-sized manifold orifices. See Table 4 for siz-
ing. (The orifice size is stamped on the orifice spud barrel.)
Placement and setup
Correctly-sized manifold orifices must be used.
Failure to do so will result in severe personal injury,
death or substantial property damage.
3. Reinstall inlet air box top panel and jacket door.
Do not operate boiler without inlet air box top panel
secured in place. Failure to comply could result in
severe personal injury, death or substantial property
damage.