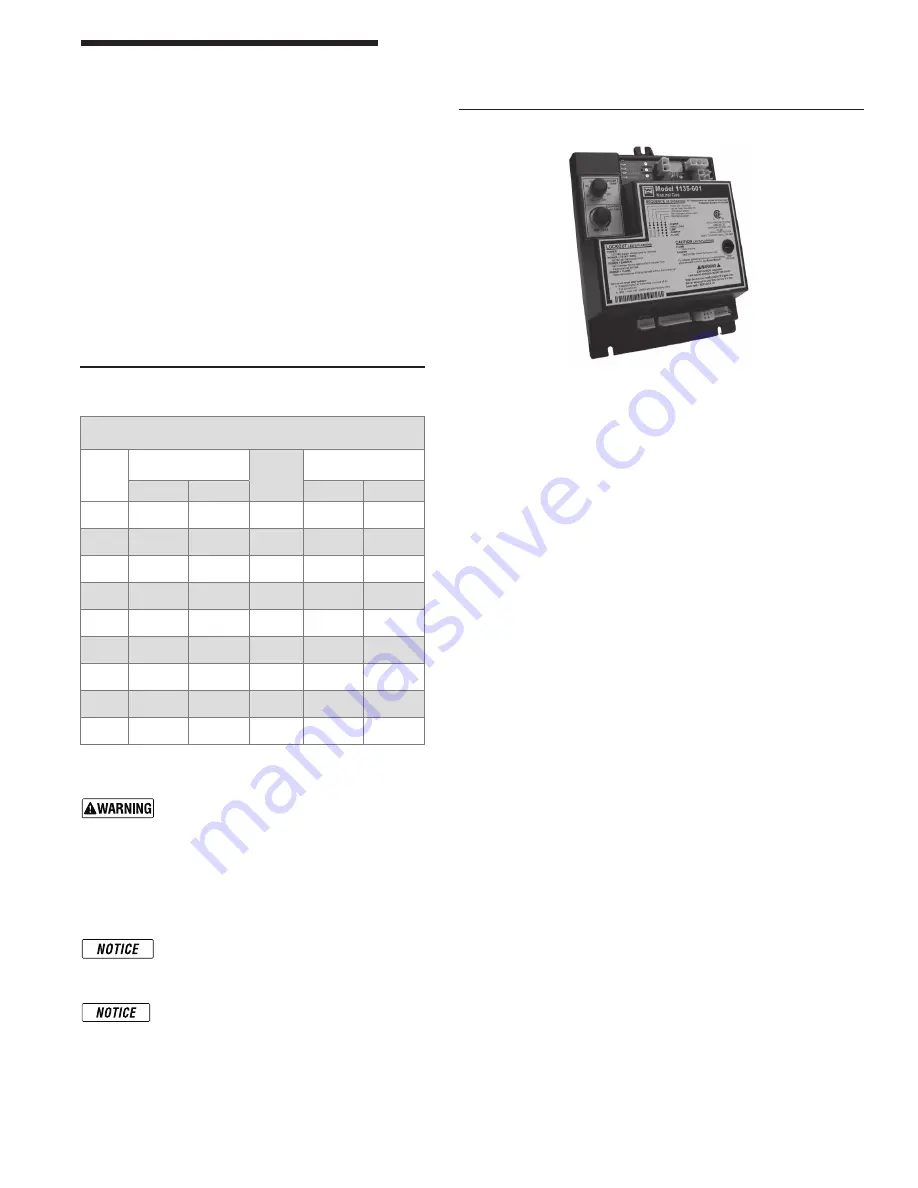
37
Part Number 550-142-320/0720
GWA
Series 3
Gas-Fired Water Boilers –
Boiler Manual
13 Troubleshooting – spark-ignited pilot boilers
Sensor resistance values
Temp
(°F)
Sensor ohms
Temp
(°F)
Sensor ohms
Min
Max
Min
Max
32
34265
37871
120
4517
4992
40
27834
30764
130
3698
4088
50
21630
23907
140
3043
3364
60
16944
18727
150
2517
2782
70
13372
14780
160
2091
2311
80
10629
11747
170
1744
1928
90
8504
9399
180
1461
1615
100
6847
7568
190
1229
1359
110
5545
6129
200
1038
1147
Temperature sensor
1. The boiler temperature sensor is a resistance-type
device.
2. See Figure 25 below shows the correct value for the
sensor at various temperatures.
3. Use the resistance values at 32°F, 60°F, 70°F and
212°F to measure the sensor resistance at known
temperatures (ice point, room temperature and sea
level boiling point). For ice point and boiling point,
insert the sensor in water at that temperature. Use an
ohmmeter to read resistance value between thermis-
tor # and thermistor common. See Figure 27, page 38,
for sensor plug details.
Figure 25 Sensor resistance values
NOTE:
If no power at control verify if external LWCO is
LOCKED OUT.
If in Low Water condition, Power is disrupted to
control.
Control indicator lights —
HARD LOCKOUT Summary (Flashing LED’s)
MAY remove 120 VAC power for more than 2 seconds to clear
lockout OR ignition control will automatically restart sequence
of operation after 1 hour waiting period after fault condition is cleared.
INDICATOR LIGHT
CONDITION
POWER
Flashes once per second
120 VAC connection to boiler reversed
or there is insufficient earth ground.
Flash code 2*
Internal fault, microprocessor or memory.
Flash code 3*
Unused.
Flash code 4*
Unused.
Flash code 5*
Internal fault, water thermistors disagree.
Flash code 6*
Internal fault, gas valve circuit.
* Flash code pattern: POWER LED flashes 2, 3, etc. times rapidly
followed by 2 seconds off, then repeats.
ALL LED’S FLASHING
Failure to establish pilot flame after 4
attempts. Propane Gas Only requires
Manual Reset, see pages 26
and
27
to correct.
SOFT LOCKOUT Summary (Flashing LED’s)
MAY remove 120 VAC power for more than 2 seconds, cycle thermostat
for between 2 and 20 seconds, OR ignition control will automatically re-
start sequence of operation after 1 hour waiting period.
INDICATOR LIGHT
CONDITION
POWER + TSTAT/CIRC
High voltage detected on TSTAT circuit.
POWER + DAMPER
Damper stuck closed or unable to close end
switch within 45 seconds from TSTAT call.
POWER + FLAME
Flame sensed without call for heat or out
of sequence during ignition trial.
CAUTION Summary (Flashing LED’s)
INDICATOR LIGHT
CONDITION
DAMPER
Damper end switch opened after it had
been proven closed.
LIMIT
Fault detected in temperature sensing hardware.
FLAME
Flame loss or flame not sensed during trial
for ignition.
Troubleshooting the control module
See Figure 27
, page 38
, for location of harness plug receptacles
and plugs on the control module.
Figure 26
GWA Ignition control module
Control module
Solder or water
splatter between plugs
and circuit board can cause improper
operation of control module. Place a
shield over the boiler internal controls and
components during installation. Failure to
comply could result in severe personal
injury, death or substantial property dam-
age.
Make sure
ground wiring
is installed
per wiring diagram. Good grounding is
extremely important for proper operation.
The information on this page and
pages 38
through 44 apply only to spark-ignited
pilot GWA boilers. These boilers are
equipped with an ignition control module
that has indicator lights to show control
status. See
Charts 1
through
6
,
pages 39
- 44
, help you identify problems based on
indicator light conditions.